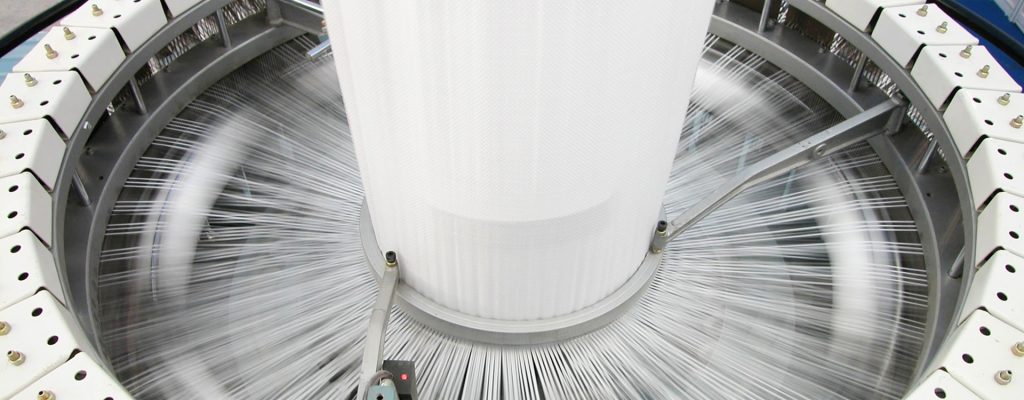
Introduction
The global aluminum foil woven bags market is projected to grow at a CAGR of 7.2% through 2030, driven by their unmatched barrier properties, customizable aesthetics, and integration of advanced printing technologies. These bags combine aluminum foil’s impermeability to moisture, oxygen, and UV light with polypropylene’s durability, making them ideal for industries like food, pharmaceuticals, and chemicals. Key innovations include multi-color printing using Starlinger and W&H machinery, matte/glossy surface customization, and smart design features that enhance both functionality and brand appeal.
Advanced Printing Technologies: Precision Meets Customization
Q: How do modern printing techniques elevate aluminum foil woven bags?
A: High-definition gravure and flexographic printing, powered by Starlinger and W&H equipment, enable vibrant, durable designs while maintaining material integrity.
- Multi-Color Printing:
- Technology: Starlinger’s AD*STAR® systems support up to 8-color printing with a resolution of 1200 dpi, achieving Pantone color accuracy within ±0.5ΔE.
- Case Study: A Chinese agrochemical brand reduced packaging waste by 20% after switching to W&H’s Varex II flexographic printers, which use water-based inks to print QR codes and handling instructions directly onto foil-lined bags.
- Surface Finish Customization:
- Matte Finish: Reduces glare and fingerprints, ideal for premium products like specialty coffee. Achieved through UV-cured coatings that lower gloss levels from 90 GU to 15 GU.
- Glossy Finish: Enhances color saturation by 30% using BOPP lamination, critical for attracting shelf attention in retail.
Material and Structural Innovations
Q: What structural features ensure functionality without compromising design?
A: Layered construction and smart seam sealing technologies balance barrier performance and visual appeal.
- Multi-Layer Design:
- Typical Structure: PP woven fabric (90–120 g/m²) + aluminum foil (7–12μm) + PE inner liner (20–25μm).
- Performance: Blocks 99.9% UV light and reduces moisture ingress to <0.1 g/m²/day (ASTM E96), extending coffee bean shelf life by 18 months.
- Seam Sealing:
- Ultrasonic Sealing: Generates seams with 4.5 kN/m tensile strength (ISO 13934-1), preventing leakage in powdered chemicals.
- Laser-Cut Edges: Minimize fraying and enhance print alignment precision to ±0.2mm.
Technical Specifications and Market Applications
Table 1: Key Parameters for Aluminum Foil Woven Bags
Parameter | Standard | Typical Value | Application Example |
---|---|---|---|
Foil Thickness | ASTM B479 | 9μm | Pharmaceutical desiccant storage |
Print Resolution | ISO 12647-2 | 1200 dpi | Retail coffee packaging |
Seam Strength | ASTM F88 | ≥4.0 kN/m | Fertilizer transport |
UV Resistance | ISO 4892-3 | 1,500 hours | Outdoor seed storage |
FAQs
- Q: How to prevent ink smudging on glossy surfaces?
- A: Use UV-cured inks with 98% polymerization rates, tested per ASTM D5264.
- Q: Are these bags recyclable?
- A: Yes. Brands like Vedhaa Polypack use mono-material PP/Alu/PP structures, achieving 85% recyclability per EN 13432.
Case Study: Smart Packaging Integration
Shandong Leihua’s “SmartGuard” bags integrate:
- RFID Tags: Track humidity in real-time, reducing coffee bean spoilage by 15%.
- Tamper-Evident Seals: Heat-sealed holographic strips with 25N peel resistance (ASTM D903).
- Customizable Artwork: Matte-finish backgrounds with glossy logos, printed using Starlinger’s 8-color rotary gravure systems.
Sustainability and Cost Efficiency
Dialogue: Addressing Client Concerns
Q: Does aluminum foil increase production costs?
A: Strategic material blending offsets expenses. For example, Zhejiang Crown Packaging uses 30% recycled PP in foil laminates, cutting raw material costs by 18% while maintaining FDA compliance.
Q: How to reduce energy consumption in printing?
A: W&H’s Ecocure dryers reduce energy use by 40% via infrared heating, saving $50,000 annually per production line.
Future Trends: Automation and Circular Economy
- AI-Driven Print Alignment: Reduces setup waste by 30% through real-time CCD camera adjustments.
- Bio-Based Foil Alternatives: PLA-coated films (under development) aim to cut carbon footprints by 50% by 2030.
External Resources:
- Explore innovations in aluminum foil composite bags for market insights.
- Learn how laminated woven bags enhance durability and branding.
By merging cutting-edge printing technologies, sustainable materials, and smart design features, aluminum foil woven bags are redefining industrial and retail packaging. As automation and eco-consciousness drive innovation, manufacturers leveraging these advancements will dominate the next era of functional, brand-enhancing solutions.