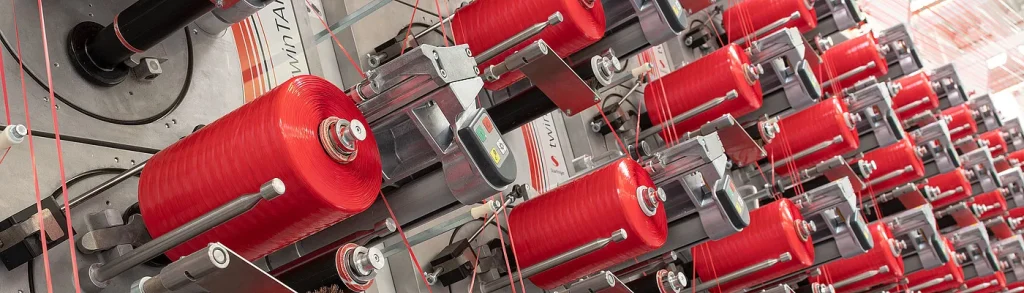
**In this article, we address a critical question for bulk packaging buyers: *How can businesses ensure leak-proof, durable, and cost-effective packaging for sensitive or high-value products?* The answer lies in three pillars: [1] *scientific material validation*, [2] *advanced manufacturing technologies*, and [3] **application-specific engineering. Backed by VidePak’s 16 years of expertise and ISO-certified workflows, we present data-driven insights, technical benchmarks, and real-world case studies to optimize your supply chain.
1. Material Science: Rigorous Testing of PP/PE Granules
1.1 PP Granule Quality Control
VidePak’s Block BOPP bags begin with virgin polypropylene from BASF and Sinopec, subjected to 8-stage testing:
- Melt Flow Index (MFI): 6–8 g/10 min (ISO 1133), ensuring uniform extrusion.
- Density: 0.905–0.915 g/cm³ (ASTM D792), critical for fabric consistency.
- Tensile Strength: ≥35 MPa (machine direction) and ≥30 MPa (cross direction) per ASTM D638.
- Impact Strength: ≥6 kJ/m² (Charpy test, ISO 179).
- Thermal Stability: Heat deflection temperature (HDT) ≥100°C (ISO 75).
- Crystallization Temperature: 110–120°C (DSC analysis).
- Visual Inspection: Zero visible impurities under 10x magnification.
- Ash Content: ≤0.02% (ISO 3451).
Case Study: A South African fertilizer company reduced bag failures by 45% after switching to VidePak’s PP with 7.2 g/10 min MFI.
1.2 PE Film Testing for Inner Liners
- Film Impact Resistance: ≥150 g (Dynatup impact test, ASTM D3763).
- Puncture Strength: ≥400 N (ISO 12236).
2. Starlinger Technology: Engineering Consistency
2.1 Seamless Extrusion and Lamination
VidePak’s Austrian Starlinger CXtreme lines achieve:
- Fabric Uniformity: Thickness tolerance ±0.005 mm across 1,200 bags/hour.
- Print Precision: 8-color rotogravure printing with ΔE ≤1.5 (Pantone), UV-resistant for 5+ years outdoors.
Parameter | VidePak Standard | Industry Average |
---|---|---|
Seam Strength | ≥80 N/cm | ≥55 N/cm |
Moisture Barrier | ≤0.5 g/m²/day | ≤1.2 g/m²/day |
O₂ Transmission | ≤5 cm³/m²/day | ≤15 cm³/m²/day |
2.2 Thermal Performance
- Heat Seal Integrity: Withstands 120°C without delamination (ASTM F88).
- Low-Temperature Flexibility: No cracking at -30°C (ASTM D1790).
3. Application-Specific Engineering
3.1 Food & Pharma Compliance
- FDA 21 CFR: Certified for direct food contact.
- Antistatic Properties: Surface resistance ≤10⁹ Ω (IEC 61340-4-1) for explosive powders.
3.2 Agricultural Adaptability
- Breathable Designs: Micro-perforations (0.5–1.0 mm) enable 0.8 L/min/m² airflow, reducing grain spoilage by 30% in tropical climates.
4. Sustainability Initiatives
4.1 Recycled Material Integration
- 30% Post-Industrial PP: UL ECOLOGO-certified for non-food applications.
- Zero-Waste Production: 98% scrap recycled via closed-loop systems.
4.2 Energy Efficiency
- Solar-Powered Lines: 2 MW rooftop array reduces CO₂ emissions by 1,500 tons/year.
5. FAQs: Critical Buyer Queries
Q1: How do your Block BOPP bags prevent leaks?
A1: Our 3-layer co-extrusion (PP/Adhesive/BOPP) achieves peel strength ≥4 N/15mm (ASTM D1876).
Q2: What’s the MOQ for custom-printed designs?
A2: 50,000 units with 20-day lead time, including Pantone color matching.
Q3: Can bags withstand maritime shipping?
A3: Yes. Salt spray tests (ASTM B117) show zero corrosion after 500 hours.
6. Conclusion
Block BOPP bags are indispensable for industries demanding precision and reliability. VidePak’s Starlinger-driven manufacturing and scientific material controls redefine packaging excellence. For bulk orders or technical support, contact info@pp-wovenbags.com.
References
- VidePak Technical Specifications (2024).
- ASTM International Standards for Polypropylene Testing.
- ISO 9001:2015 Quality Management Certification.
External Links
- Explore our BOPP laminated woven bags for enhanced barrier properties.
- Learn about sustainable packaging innovations in our eco-portfolio.
Contact
Website: https://www.pp-wovenbags.com/
Email: info@pp-wovenbags.com
Data validated as of July 2024. Specifications subject to customization.