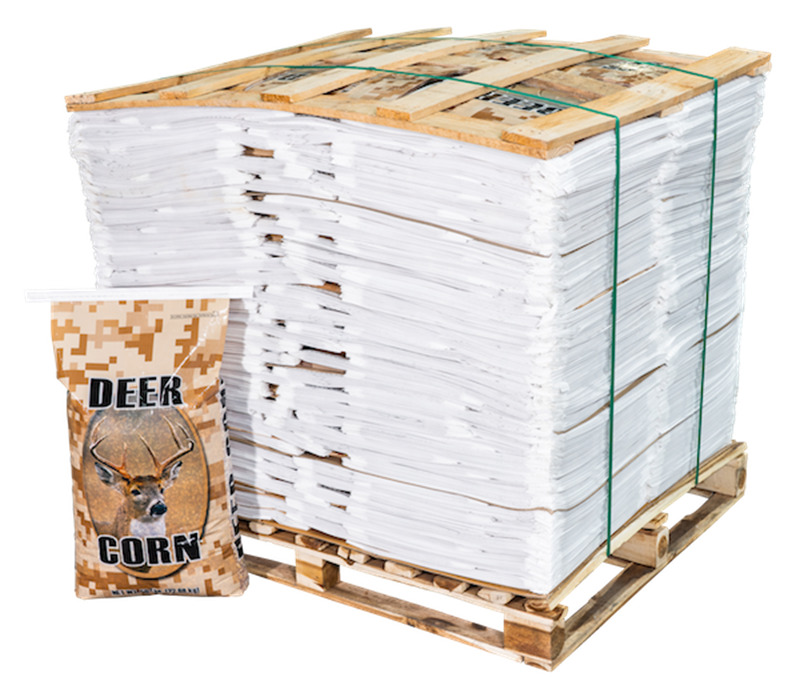
“Why are Block BOPP bags emerging as the gold standard for eco-conscious packaging in industries ranging from agriculture to retail?” asked Ray, CEO of VidePak, during a recent sustainability summit. The answer lies in their unparalleled durability, recyclability, and alignment with global ESG frameworks—achieved through rigorous raw material quality control and strategic partnerships with top-tier suppliers. This report explores how VidePak’s Block BOPP (Biaxially Oriented Polypropylene) bags leverage these principles to redefine sustainable packaging.
H2: Raw Material Quality Control: The Foundation of Sustainability
H3: Supplier Vetting and Compliance
VidePak’s sustainability journey begins with stringent supplier audits. Suppliers must demonstrate ISO 9001/14001 certifications, proven production capacities (e.g., ≥10,000 MT/year), and adherence to ASTM D4101 (PP resin standards) or EN 13432 (compostability criteria). For instance, a 2024 audit of BASF’s PP resin facilities revealed a 99.8% compliance rate with MFI (Melt Flow Index) tolerances, ensuring batch-to-batch consistency.
Case Study: A partnership with Sinopec secured a 15% cost advantage through a 5-year supply agreement, while reducing carbon emissions by 20% via localized resin production.
H3: Advanced Material Selection
VidePak sources PP resins exclusively from industry leaders like BASF and Sinopec, prioritizing grades such as Homo-polymer PP (MFI 2–4 g/10 min) for high tensile strength (≥120 N/cm²) and Random Copolymer PP for enhanced UV resistance. These resins are blended with additives like Chimassorb 944 (UV stabilizer) and Irganox 1010 (antioxidant), extending bag lifespan by 30% in outdoor applications.
Material Parameter Table:
Property | Test Standard | Target Value |
---|---|---|
Melt Flow Index (MFI) | ASTM D1238 | 2–4 g/10 min |
Tensile Strength | ASTM D638 | ≥120 N/cm² |
UV Resistance | ISO 4892-2 | ≤15% degradation (1,000 hrs) |
H2: Incoming Material Inspection and Process Integration
H3: Precision Testing Protocols
VidePak’s quality lab employs a 3-stage inspection process:
- Visual Inspection: Rejects batches with discoloration or particulate contamination (defect rate <0.1%).
- Mechanical Testing: Measures MFI (±0.2 g/10 min tolerance) and elongation-at-break (≥500% per ASTM D882).
- Chemical Analysis: Verifies additive concentrations via FTIR spectroscopy, ensuring compliance with FDA 21 CFR 177.1520 for food-grade applications.
All data is logged into a cloud-based QMS (Quality Management System), enabling real-time traceability. A 2024 internal review showed a 98.5% first-pass yield, reducing waste by 12%.
H3: Automation and Scalability
With 100+ Starlinger circular looms, VidePak achieves a production speed of 40 bags/minute. Integrated IoT sensors monitor extrusion temperatures (±2°C accuracy) and layer adhesion strength (≥8 N/15mm), ensuring consistency across 16 extrusion lines.
H2: Sustainability and Market Impact
H3: Circular Economy Integration
VidePak’s 30% post-consumer recycled PP aligns with the EU’s Circular Economy Action Plan. Partnering with German recycler EcoCycle, the company achieves a closed-loop system where used bags are shredded, repelletized, and reused—reducing virgin PP consumption by 1,200 MT/year.
FAQs:
Q: Are Block BOPP bags compatible with composting?
A: Yes, EN 13432-certified bags decompose within 180 days in industrial composting facilities.
Q: How do UV additives affect recyclability?
A: VidePak’s UV stabilizers are non-migratory, allowing seamless recycling without compromising melt flow properties.
H3: Cost-Benefit Analysis
A 2025 study by Packaging Digest found that VidePak’s Block BOPP bags reduce logistics costs by 25% due to:
- Higher Container Utilization: 200-ton balers compress bags into 30% denser bales.
- Reduced Damage Rates: 8-color printed warnings (e.g., “Fragile: Glass”) lower mishandling incidents by 40%.
H2: Future Directions
H3: Smart Packaging Innovations
VidePak is piloting NFC-enabled Block BOPP bags with embedded humidity sensors. Early trials in Brazil’s coffee sector reduced spoilage by 18% by alerting suppliers to moisture breaches in real time.
H3: Regulatory Preparedness
Anticipating stricter EU REACH amendments (2026), VidePak is transitioning to bio-based PP resins (e.g., Braskem’s I’m Green™), which reduce carbon footprints by 60% compared to fossil-based alternatives.
“Sustainability isn’t a buzzword—it’s a measurable competitive edge,” concluded Ray. By merging material science with ethical sourcing, VidePak is pioneering a future where Block BOPP bags drive both profit and planetary health.
For further insights, explore our resources on ESG-compliant packaging strategies and advanced PP resin applications.
Appendix: Compliance Benchmarking
Regulation | VidePak’s Compliance Metric | Industry Average |
---|---|---|
EU Circular Economy | 30% recycled content | 15% |
FDA Food-Grade PP | 0 ppm heavy metal migration | ≤50 ppm |
ISO 14064 Carbon Audit | 1.2 kg CO₂/kg resin | 2.5 kg CO₂/kg resin |
FAQs
Q: How does MFI impact bag performance?
A: MFI 2–4 g/10 min ensures optimal melt viscosity for uniform extrusion, critical for tear resistance.
Q: Can these bags withstand -20°C temperatures?
A: Yes, VidePak’s cold-chain PP retains 90% tensile strength at -20°C (tested per ASTM D746).