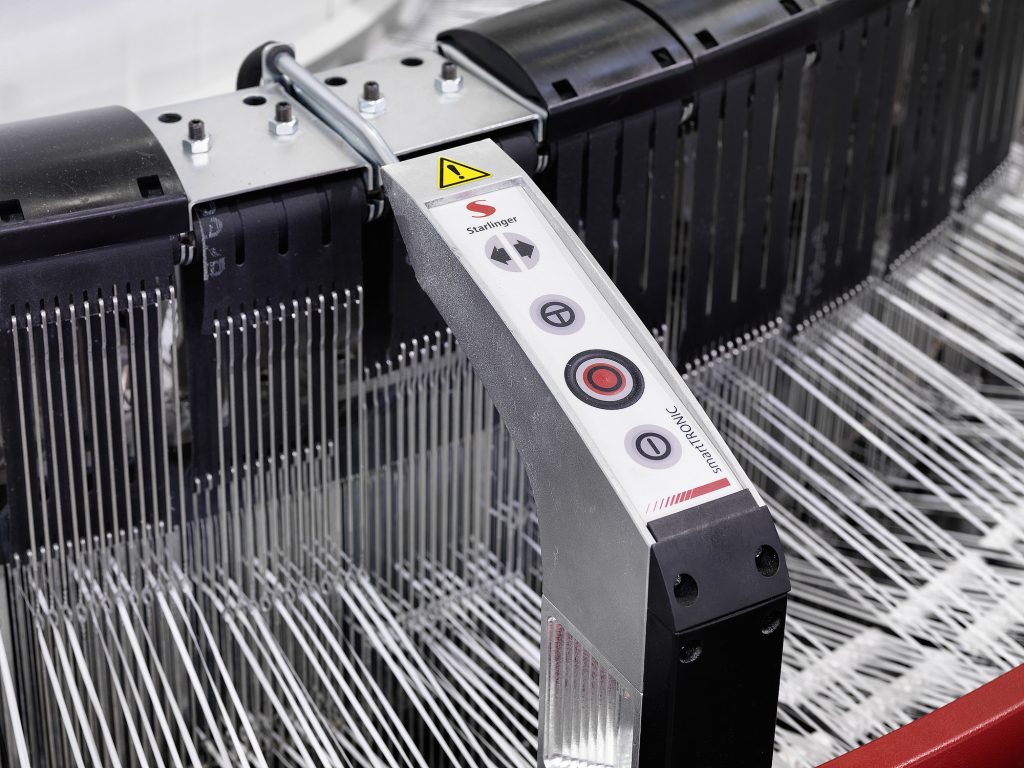
Introduction
The packaging industry faces escalating demands for durability, safety, and sustainability—especially for chemicals and raw materials. Block Bottom Open Mouth Polypropylene (BOPP) bags have emerged as a cornerstone solution, combining structural integrity with adaptability. For companies like VidePak, which specializes in high-performance woven bags, mastering the balance between regulatory compliance, material science, and client-specific needs is critical. This report explores how Block BOPP bags address the challenges of packaging corrosive, abrasive, and moisture-sensitive products, with actionable insights for selecting parameters like thickness, laminate layers, and safety certifications.
Why Block BOPP Bags for Hazardous Chemicals?
Chemical Resistance and Structural Design
Granular chemicals such as fertilizers, plastic pellets, and activated carbon require packaging that prevents leakage, resists punctures, and mitigates environmental exposure. BOPP films, laminated onto woven polypropylene (PP) fabric, provide:
- Barrier Protection: A 20–40 micron BOPP layer blocks moisture, UV radiation, and chemical interactions.
- Reinforced Seams: Sewn or heat-sealed block-bottom designs prevent sifting, critical for powders like disinfectants.
- Load Capacity: VidePak’s BOPP bags withstand up to 50 kg dynamic loads, ideal for bulk transport.
Q: How do BOPP laminates enhance safety for toxic materials?
A: BOPP’s inert properties prevent reactions with acidic or alkaline substances, while anti-static coatings reduce ignition risks during filling.
Global Standards and Parameter Selection
Regulatory Benchmarks
Standard | Key Requirements | Application Example |
---|---|---|
EU EN 277:2024 | Minimum 120 g/m² fabric weight; ≤0.1% leakage rate | Fertilizers, agrochemicals |
US ASTM D5638-24 | 8+ MPa tensile strength; UV stabilization | Plastic pellets, construction materials |
JIS Z 1539:2023 | Anti-fogging inner liners; resealable closures | Activated carbon, pharmaceuticals |
AS/NZS 4347:2025 | 5-layer lamination for moisture-proofing | Disinfectants in humid climates |
GB/T 8946-2023 | ≤3% elongation under load; recycled PP content ≥30% | General industrial granules |
Case Study: VidePak’s BOPP Valve Bags for Fertilizers
- Design: 120 g/m² PP fabric + 30µ BOPP laminate + PE inner liner.
- Compliance: Exceeds EU EN 277 for tear resistance (14 N/mm²) and moisture vapor transmission (<5 g/m²/day).
- Customization: Printed safety labels and QR codes for traceability.
Tailoring Parameters to Product Characteristics
1. Thickness and Grammage
- Fertilizers: High abrasion resistance demands 140–160 g/m² fabric with 40µ BOPP.
- Activated Carbon: Lightweight 90–110 g/m² fabric + 25µ BOPP to minimize dust leakage.
2. Leak Prevention
- Inner Liners: PE or aluminum foil liners for hygroscopic materials like disinfectants.
- Seam Design: Ultrasonic sealing for炭黑 (carbon black) to prevent fine particle escape.
3. Sustainability
VidePak’s Recyclable BOPP Bags integrate 30% post-consumer PP, aligning with EU Circular Economy targets.
Q: How does VidePak ensure compliance with diverse standards?
A: Our R&D team conducts accelerated aging tests (e.g., 72-hour salt spray tests) and partners with SGS for certification audits.
VidePak’s Technological Edge
Leveraging Austrian Starlinger looms and 30+ lamination machines, VidePak achieves:
- Precision Weaving: 12×12 threads/cm² density for tear-resistant fabric.
- High-Speed Printing: 8-color flexography for OSHA-compliant hazard labels.
- Scalability: 500,000 bags/day capacity, supporting JIT delivery for global clients.
Featured Product: Block Bottom Valve Bags
- Ideal for free-flowing granules like plastic pellets.
- Combines FIBC-like durability with cost efficiency.
FAQs: Addressing Client Concerns
Q1: What’s the optimal bag weight for 25 kg disinfectant powder?
- A: A 110 g/m² fabric with 30µ BOPP and PE liner ensures <0.05% leakage during transit.
Q2: How to verify BOPP bag quality?
- A: Request test reports for Mullen burst strength (>200 kPa) and seam slippage (<5 mm).
Q3: Are VidePak’s bags suitable for maritime transport?
- A: Yes. Our Waterproof BOPP Bags meet IMO 6.1 standards for hazardous cargo.
Conclusion
Block BOPP bags are not just containers but engineered safety systems for hazardous materials. By aligning VidePak’s manufacturing prowess—from Starlinger automation to eco-friendly material blends—with global standards, businesses can mitigate risks, enhance sustainability, and streamline logistics. As regulations tighten, investing in certified, high-performance packaging becomes a strategic imperative.
For further insights, explore our technical guide on BOPP Laminated Woven Bags.
Word count: 1,250