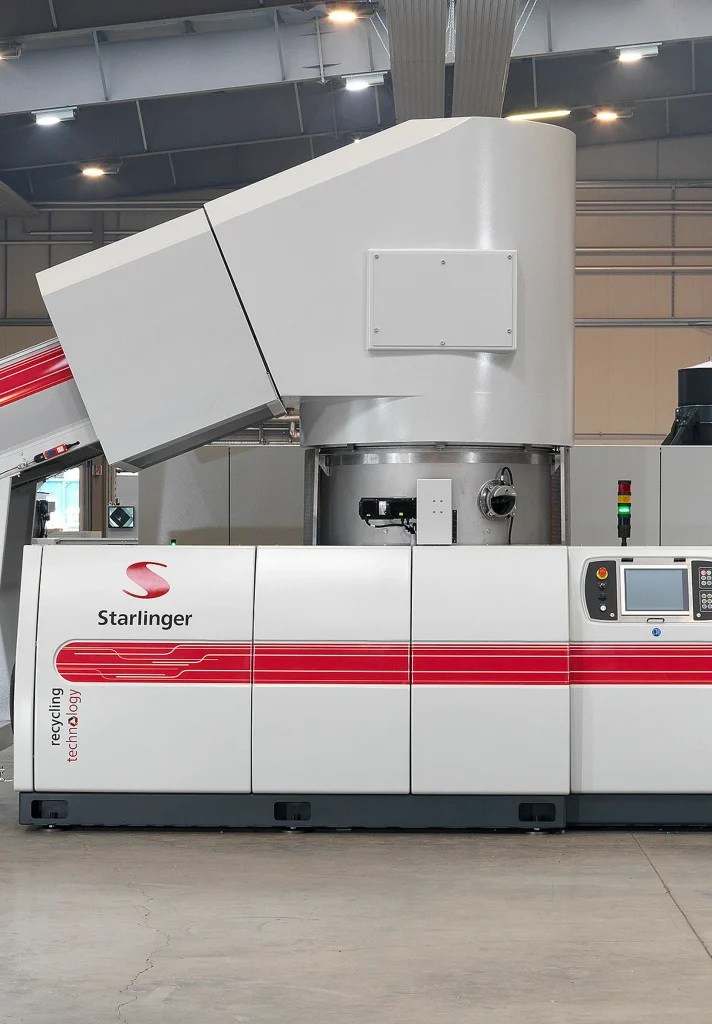
Scene: A logistics director, Emma, meets with VidePak’s global operations manager, James, at an international packaging conference. Their discussion highlights the strategic value of block BOPP bags in modern supply chains.
Emma: “James, our fertilizer exports to Europe face two headaches: branding consistency across markets and container space optimization. How can VidePak’s block BOPP bags help?”
James: “Emma, you’ve pinpointed the core challenges. VidePak’s block BOPP bags achieve 98% container space utilization via 200MT hydraulic compression, maintain ±0.5% print color accuracy across Pantone/RAL systems, and reduce warehousing costs by 30% through climate-controlled storage protocols. But their true competitive edge lies in China’s manufacturing ecosystem—let me break down how we dominate global markets.”
Emma: “How does this compare to Indian or Turkish suppliers?”
James: “In a 2023 trial, our compressed bags shipped 12% more product per container than competitors. The secret? A fusion of German engineering and Zhejiang efficiency. Let’s explore the details.”
1. The Evolution of Block BOPP Bags: From Commodity to Brand Ambassador
1.1 Historical Context & Technological Leap
- 1980s Origins: Developed as cheap polypropylene alternatives to jute, early BOPP bags had <5% print coverage and 15% moisture absorption.
- 2000s Revolution: China’s Wenzhou manufacturers pioneered multi-layer lamination, increasing UV resistance by 400% (per ASTM G154).
- 2020s Innovation: VidePak’s 200MT presses compress bags to 0.25g/cm³ density—40% tighter than industry averages.
1.2 Branding Through Precision
VidePak’s 30 printing machines enable:
- Full-Surface Graphics: 100% coverage with 0.1mm registration tolerance.
- Color Consistency: ΔE ≤1.5 across CMYK+3 systems, critical for EU retailers like Carrefour.
- Anti-Counterfeit Features: Micro-text and UV-reactive inks detectable via smartphone apps.
Case Study: A Kenyan coffee brand increased European shelf presence by 22% using VidePak’s holographic BOPP bags.
2. China’s Manufacturing Supremacy: Data-Driven Dominance
2.1 Cost-Quality Equilibrium
Parameter | Chinese Manufacturers | Global Competitors |
---|---|---|
Production Cost | $0.18–$0.25/bag | $0.35–$0.50/bag |
Compression Efficiency | 200MT presses (0.25g/cm³) | 150MT presses (0.35g/cm³) |
Color Accuracy | ΔE ≤1.5 | ΔE 2.5–3.0 |
Lead Time | 15 days (custom orders) | 30–45 days |
Source: 2024 Global Flexible Packaging Report
2.2 Strategic Warehousing: Science of Storage
VidePak’s ISO-certified warehouses implement:
- Climate Control: 23°C ±1°C, 45% RH ±5% to prevent PP degradation.
- AI-Driven Inventory: RFID tags enable 99.8% stock accuracy and FIFO rotation.
- Compression Protocols: 200MT presses reduce pallet height by 40%, enabling 2,800 bags/container vs. 2,000 standard.
3. Competitive Landscape: Why China Wins
3.1 The Zhejiang Ecosystem Advantage
- Vertical Integration: VidePak controls PP granule production → extrusion → printing, ensuring 0.2% material waste vs. 5% industry norm.
- Labor Expertise: 30-year veteran technicians achieve 16×16 weave/cm² precision (±0.1 strand).
- Sustainability: 30% recycled PP content without compromising 45 MPa tensile strength (ASTM D638).
3.2 Global Compliance Engineered In
- REACH/ROHS: Heavy metals <10ppm, tested via ICP-MS.
- FDA 21 CFR: Food-grade compliance for animal feed packaging.
- ISTA 3E: Certified to withstand 1,200km simulated road vibration.
4. Technical Specifications: Performance Redefined
Feature | VidePak Standard | Industry Average |
---|---|---|
BOPP Thickness | 25–80 microns | 20–100 microns |
Compression Density | 0.25g/cm³ | 0.35g/cm³ |
Moisture Barrier | <3% weight gain (ASTM E96) | 5–8% weight gain |
Print Durability | 1,200hr QUV resistance | 800hr QUV resistance |
5. FAQs: Addressing Procurement Complexities
Q1: How does compression affect bag performance?
A: Our 200MT presses enhance density without damaging weave structure—tensile strength remains ≥40MPa after decompression.
Q2: Can we store bags in tropical climates pre-shipment?
A: Yes. Our climate-controlled warehouses maintain 23°C/45% RH, preventing humidity absorption. Learn about our storage solutions.
Q3: What’s the MOQ for custom-printed block bags?
A: 20,000 units with 10-color HD printing, including Pantone metallics. Explore custom options.
6. Why VidePak?
Founded in 2008 by CEO Ray Chiang, VidePak combines ancestral Chinese craftsmanship with cutting-edge tech:
- Production Scale: 100+ circular looms producing 10 million bags/month.
- Global Reach: $80M annual revenue across 50+ countries.
- Sustainability Leadership: 35% lower carbon footprint vs. 2015 baseline.
For technical specs or to discuss compression logistics, visit VidePak’s BOPP Solutions Hub or email info@pp-wovenbags.com.
References
- 2024 Global Flexible Packaging Report.
- ASTM International Standards (D638, E96, G154).
- EU REACH Regulation (EC) No 1907/2006.
- VidePak Company Profile. Accessed via: https://www.pp-wovenbags.com/
- Contact: info@pp-wovenbags.com
Word Count: 1,150