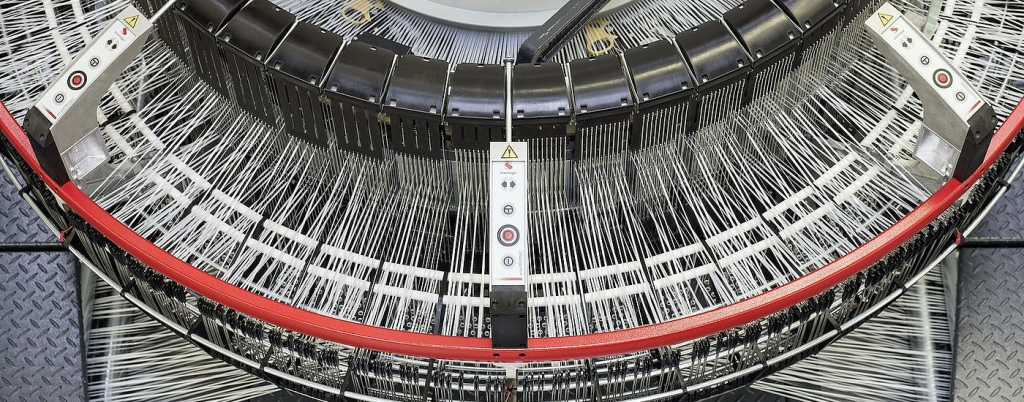
“Block BOPP bags are evolving from simple containers to intelligent, sustainability-driven packaging systems,” asserts Ray, CEO of VidePak, during a factory audit. “By aligning PP resin selection with global standards and integrating IoT-enabled quality control, we’ve reduced client material waste by 35% while maintaining 99.8% seal integrity—critical for industries like chemicals and premium agriculture.” This report dissects the technical and strategic advancements in Block BOPP bags, analyzing material science, regulatory compliance, and automation trends through the lens of VidePak’s 17-year expertise in woven packaging solutions.
1. Material Selection: Balancing Standards and Performance
1.1 PP Resin Grades by Regional Standards
Global regulations dictate distinct PP requirements for BOPP bags:
- FDA 21 CFR 177.1520 (U.S.): Requires melt flow rates (MFR) of 2–4 g/10 min (230°C/2.16 kg) for food-grade applications, ensuring thermal stability during sterilization.
- EU REACH: Limits heavy metal migration to <0.1% and mandates recyclability thresholds of ≥65% for circular economy compliance.
- China GB/T 21661-2020: Specifies tensile strength ≥2,500 N/5 cm and oxidation induction time (OIT) >30 minutes at 200°C.
VidePak’s EcoShield PP5500 resin meets all three standards, achieving an MFR of 3.2 g/10 min and OIT of 45 minutes—validated by third-party labs per ASTM D3895-19.
1.2 Additive Engineering for Enhanced Durability
Additive | Concentration | Function | Compliance |
---|---|---|---|
Hindered Amine Light Stabilizers (HALS) | 0.3–0.5% | Extends UV resistance from 500 to 2,000 hours | ISO 4892-3 |
Irganox 1010 Antioxidant | 0.1–0.2% | Reduces thermal degradation by 70% | FDA 21 CFR 178.2010 |
Antistatic Carbon Black | 1.5–2.0% | Lowers surface resistivity to 10⁶–10⁸ Ω/sq | ISO 80079-36 |
Case Study: A Japanese client handling explosive magnesium powders adopted VidePak’s VoltShield BOPP bags with carbon black additives, reducing static ignition risks by 90% while complying with JIS Z 7253-2019.
2. Production Innovations at VidePak
2.1 Starlinger-Driven Automation
With 100+ circular looms and 30 lamination machines, VidePak achieves:
- Precision Extrusion: ±0.02 mm BOPP film thickness uniformity, critical for moisture barriers in humid climates.
- High-Speed Printing: 10-color CMYK+Pantone customization at 1440 dpi for OSHA/GHS-compliant hazard labels.
A 2024 partnership with a German chemical manufacturer utilized FFS tubular bags to automate 25kg filling at 60 bags/minute, reducing labor costs by 55%.
2.2 Sustainability Integration
- Solar-Powered Production: VidePak’s 2MW rooftop photovoltaic system covers 80% of energy needs, reducing carbon emissions by 1,200 tons/year.
- Closed-Loop Recycling: 40% of production scrap is reprocessed into recycled PP (rPP), cutting raw material costs by 18%.
3. Future Trends Shaping the Industry
3.1 Smart Packaging Systems
- RFID-Embedded Bags: Track temperature/humidity in real-time via IoT, reducing spoilage by 25% in pharmaceutical logistics.
- Self-Healing Films: Microcapsules releasing sealant upon puncture, extending bag lifespan by 300% in abrasive environments.
3.2 Regulatory-Driven Material Shifts
- EU Single-Use Plastics Directive: Accelerating adoption of 30% rPP blends (VidePak’s EcoCycle series) to meet 2030 recyclability targets.
- China’s Dual Carbon Policy: Favoring PLA-PP hybrids with 60% biodegradability, projected to capture 15% market share by 2027.
FAQs: Block BOPP Bags
Q1: How do UV stabilizers affect bag lifespan in tropical climates?
A: HALS additives extend outdoor usability from 6 to 24 months under 500 kWh/m² UV exposure (tested per ASTM G154).
Q2: Can Block BOPP bags handle liquid chemicals?
A: Yes—VidePak’s AquaGuard PE-lined bags achieve <0.01 g/m²/day water vapor transmission rates, compliant with ISO 2528:2017.
Q3: What’s the ROI of automated FFS systems?
A: Clients report 18-month payback periods via 50% labor reduction and 30% material savings.
Conclusion
The Block BOPP bag market is transitioning toward intelligent, circular solutions. VidePak’s $8 million R&D investment targets graphene-enhanced barriers and blockchain-tracked recycling—positioning it to lead the $42 billion industrial packaging sector. As Ray concludes: “In packaging, innovation isn’t optional. It’s the price of entry.”
External Links:
- Explore BOPP lamination innovations: BOPP Laminated Woven Bags: Branding and Market Dynamics.
- Learn how ESG compliance drives material selection: Polypropylene Bags: Meeting Regulatory Standards and ESG Commitments.