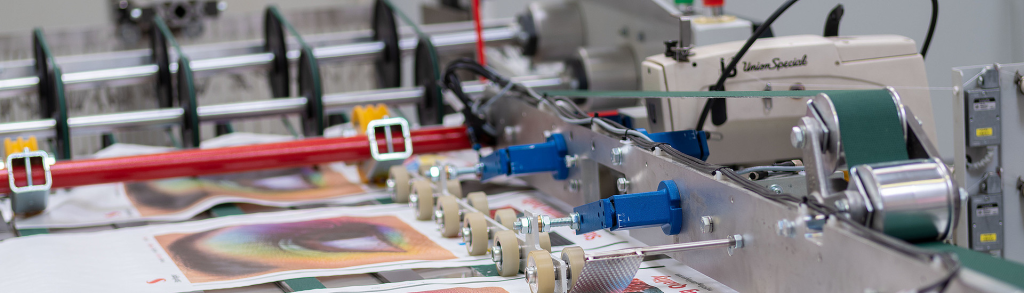
Block BOPP (Biaxially Oriented Polypropylene) bags are a transformative packaging solution designed to meet the stringent requirements of the chemical powder industry. Combining advanced materials with cutting-edge manufacturing processes, these bags provide superior durability, moisture resistance, and customizability, making them indispensable for chemical packaging.
1. Evolution of Block BOPP Bags
The evolution of Block BOPP bags reflects the increasing demand for robust, high-performance packaging in industries like chemicals, fertilizers, and food. Early woven bags, while practical, lacked the protective features needed for fine powders. The introduction of BOPP film addressed these gaps, enabling manufacturers to meet both functional and branding needs.
Why BOPP Bags Outperform Traditional Solutions:
- Moisture Protection: The laminated BOPP film creates an impermeable barrier, essential for preventing powder degradation.
- Enhanced Strength: Polypropylene fabric offers high tensile strength, reducing the risk of tears or punctures.
- Custom Printability: BOPP’s smooth surface supports high-definition printing, ensuring clear branding and compliance with labeling regulations.
By integrating these features, Block BOPP bags deliver performance that traditional kraft or multi-wall paper bags cannot match.
2. Materials and Manufacturing Process
Block BOPP bags are constructed using 100% virgin polypropylene, ensuring consistency and strength. Their multi-layered design includes a woven polypropylene base laminated with BOPP film, offering a combination of flexibility, durability, and aesthetic appeal.
Technical Breakdown of Manufacturing:
- Tape Extrusion: Virgin polypropylene is melted and stretched into flat tapes, providing the base for high-strength woven fabric.
- Fabric Weaving: The tapes are woven into circular or flat fabric, forming the structural core of the bag.
- BOPP Lamination: A biaxially oriented film is laminated onto the woven fabric, enhancing moisture resistance and enabling high-quality printing.
- Cutting and Stitching: Bags are cut and stitched to precise dimensions, ensuring uniformity and reliability.
- Printing: Advanced printing machines apply multi-color graphics for branding and product information.
Feature | Technical Advantage |
---|---|
Material | 100% virgin polypropylene for consistent strength |
Lamination | BOPP film for water resistance and UV protection |
Capacity | Supports weights from 5 kg to 50 kg |
Printing Quality | High-definition, multi-color printing for branding |
Durability | Resistant to punctures and tears, even under heavy loads |
3. Cost Control Strategies
Effective cost control is critical for manufacturers and end-users alike. Block BOPP bags address cost concerns through innovative design and efficient production.
How Costs Are Minimized:
- Material Efficiency: The use of virgin polypropylene and optimized lamination reduces material waste while maintaining quality.
- Automation in Production: Automated processes for cutting, stitching, and printing reduce labor costs and improve consistency.
- Durability Reducing Waste: High-strength materials minimize the risk of damage during handling and transport, reducing losses due to bag failure.
These strategies not only lower production costs but also provide long-term savings for users by reducing waste and ensuring reliable performance.
4. Future Trends: Automation and Sustainability
The future of Block BOPP bags lies in integrating advanced automation and sustainable practices, ensuring these bags remain competitive in an increasingly eco-conscious market.
Automation Enhancements:
- Smart Manufacturing: Real-time monitoring systems powered by IoT enhance quality control, reducing defects and downtime.
- Robotic Systems: Robots for stitching and printing ensure uniformity, speeding up production while maintaining precision.
Sustainability Focus:
- Recyclable Materials: Efforts to improve the recyclability of BOPP films are driving innovations in material science.
- Energy Efficiency: Manufacturers are adopting energy-efficient machinery to reduce the carbon footprint of production.
- Circular Economy: Used bags can be repurposed into new products, aligning with global sustainability goals.
For further insights into sustainable practices, explore industrial woven packaging bags aligning with policies and ESG standards.
5. FAQs
Q1: Why are Block BOPP bags ideal for chemical powders?
A1: The BOPP film layer provides superior moisture resistance, essential for preserving the quality of fine powders. Additionally, the woven fabric prevents tears, ensuring safe storage and transport.
Q2: How do Block BOPP bags support branding?
A2: Their smooth, laminated surface allows for high-definition multi-color printing, making it easier to display brand logos and product details with clarity.
Q3: Are these bags environmentally friendly?
A3: While not biodegradable, Block BOPP bags are fully recyclable, and advancements in material design are enhancing their sustainability.
Q4: How do these bags compare to Kraft Paper bags?
A4: Block BOPP bags provide superior durability and moisture resistance, making them better suited for fine powders. For more on Kraft Paper bags, check out Kraft Paper Bags laminated with woven fabric.
6. Conclusion
Block BOPP bags are the gold standard for chemical powder packaging, offering unmatched durability, moisture resistance, and cost-effectiveness. Backed by advanced manufacturing techniques and a focus on sustainability, these bags address the critical needs of industries while paving the way for future innovation.
By choosing Block BOPP bags, businesses not only ensure product safety and quality but also contribute to a more efficient and sustainable packaging ecosystem.