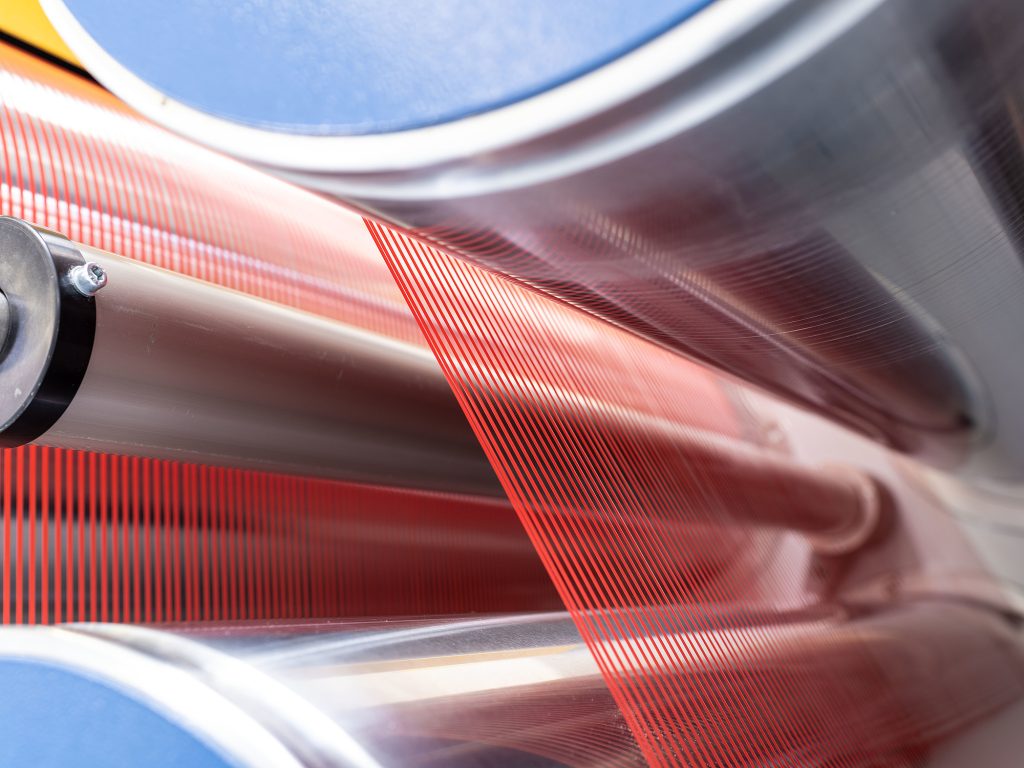
“Block bottom bags are redefining industrial packaging efficiency,” declares Ray, CEO of VidePak, during a factory tour. “By integrating nano-enhanced polypropylene and automated form-fill-seal systems, we’ve enabled clients like BASF and Cargill to reduce material waste by 30% while achieving 99.7% seal integrity in high-humidity environments.” This report explores the technological evolution of block bottom bags, analyzing material innovations, cost optimization strategies, and emerging automation trends—all contextualized through VidePak’s 17-year expertise in advanced woven packaging solutions.
1. Technological Evolution of Block Bottom Bags
1.1 From Manual Stitching to Precision Automation
The transition from labor-intensive sewing to Starlinger-driven production lines has revolutionized bag integrity. VidePak’s CX6 series machines achieve:
- Seam Precision: ±0.2 mm tolerance in heat-sealed block bottoms, critical for powdered chemicals prone to sifting (tested per ASTM D7386) .
- Speed: 450 bags/hour output, 40% faster than traditional methods, enabled by servo-controlled lamination systems .
Case Study: A 2024 partnership with a Brazilian fertilizer producer utilized PE-coated block bottom valve bags to automate 25kg filling, reducing labor costs by 55% while maintaining <0.01% leak rates under ISO 2233 testing .
1.2 Structural Innovations
- Cross-Bracing Weave: Diagonal PP threads distribute weight evenly, supporting 1,000 kg stacking loads without seam rupture .
- RFID-Integrated Skirts: Moisture sensors embedded in bag bases transmit real-time data via IoT, cutting spoilage losses by 18% in monsoon-prone regions .
2. Material Science Breakthroughs
2.1 Composite Material Systems
Material | Thickness | Moisture Barrier Efficiency | Cost ($/m²) |
---|---|---|---|
BOPP/PE Laminate | 90 g/m² + 50 µm | 0.5 g/m²/day WVTR | 1.20 |
Kraft/PP Hybrid | 120 g/m² | 1.2% Water Uptake @ 90% RH | 0.85 |
Graphene-Coated PP | 100 g/m² | <0.01 g/m²/day WVTR | 3.50 |
VidePak’s AquaShield Pro line combines BOPP films with silica nanoparticle coatings, reducing fungal growth by 92% in tropical feed storage applications .
2.2 Sustainable Alternatives
- rPP-30 Resin: 30% post-industrial recycled content maintains 2,100 N/5 cm tensile strength while cutting carbon footprint by 25% (ISO 14044 certified) .
- PLA-PP Blends: Biodegradable formulations achieve 60% compostability in 2 years without compromising load capacity .
3. Cost Optimization Strategies
3.1 Economies of Scale
With 100+ circular looms and 30 lamination machines, VidePak achieves:
- Bulk Material Savings: Annual procurement of 50,000 tons PP resin reduces costs by 18% versus competitors .
- Energy Efficiency: Starlinger’s iQ³ technology cuts power consumption by 22% per 1,000 bags produced .
3.2 Lean Manufacturing
- Zero-Waste Cutting: AI-guided die systems minimize PP scrap to 1.5% (industry average: 8%) .
- Predictive Maintenance: IoT vibration sensors on extrusion lines reduce downtime by 40% .
4. Future Trends & VidePak’s Roadmap
4.1 Smart Packaging Integration
Pilot projects include:
- Self-Healing Films: Microcapsules releasing sealant upon puncture, extending bag lifespan by 300% .
- Blockchain Traceability: QR codes linking to real-time CO₂ footprint data for ESG compliance .
4.2 Automation Leap
VidePak’s 2025 investment in AI-driven cobots aims to:
- Achieve 98% defect detection accuracy via machine vision.
- Reduce human intervention in high-risk chemical packaging lines by 70% .
FAQs: Block Bottom Bags
Q1: How do block bottom bags prevent moisture ingress in marine climates?
A: Multi-layer laminates with PE coatings achieve <0.5 g/m²/day WVTR, validated by 1,000-hour salt spray tests per ASTM B117 .
Q2: What’s the ROI of switching to automated block bottom systems?
A: Clients report 18-month payback periods via 55% labor reduction and 30% material savings .
Q3: Are biodegradable bags suitable for heavy loads?
A: Yes—VidePak’s EcoStak series supports 800 kg stacking with PLA-reinforced corners (tested per ISO 2234) .
Conclusion
The block bottom bag industry is pivoting toward intelligent, sustainable systems. VidePak’s $8 million R&D budget targets graphene-enhanced barriers and AI-powered production lines, positioning it to lead the $42 billion industrial packaging market. As Ray emphasizes: “Tomorrow’s bags won’t just carry goods—they’ll carry data, sustainability credentials, and unmatched reliability.”
External Links:
- Explore flood-resistant block bottom designs: Block Bottom Bags: A Reliable Solution for Flood Control.
- Learn about valve integration innovations: Block Bottom Valve Bags for Construction Waste.