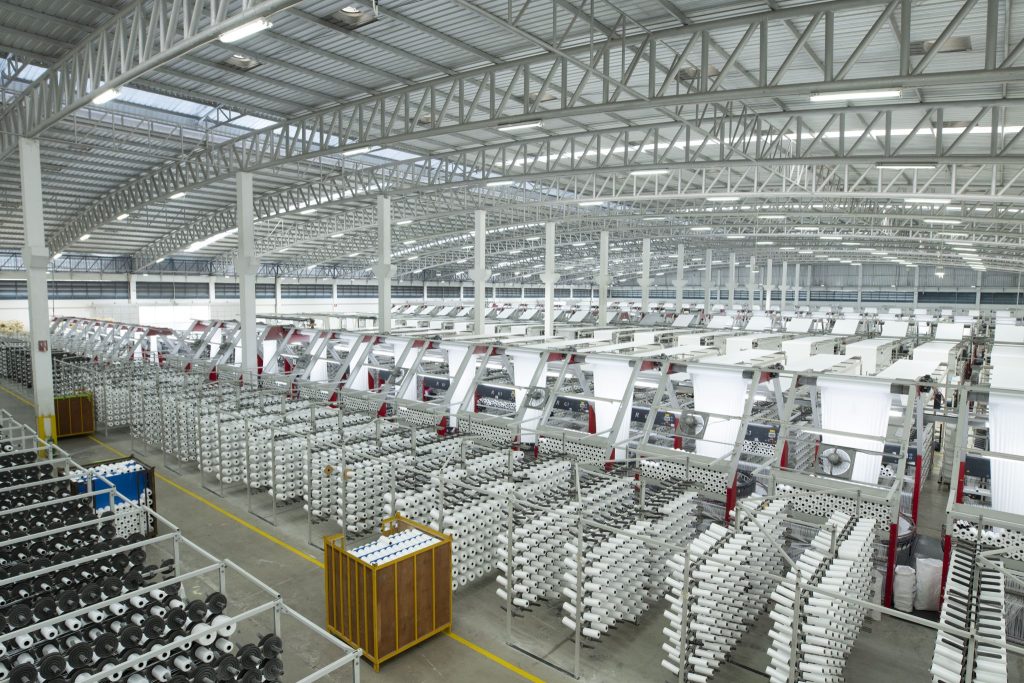
Block bottom bags, also known as square-bottom or block-bottom woven polypropylene (PP) bags, have emerged as one of the most efficient and reliable solutions for packaging chemical products. These bags combine the strength and durability of woven PP fabric with a specialized design that offers superior stability, easy handling, and cost-effectiveness. In industries dealing with chemicals, ensuring product safety, integrity, and compliance with environmental standards is of utmost importance, and block bottom bags are uniquely suited to meet these challenges.
In this article, we will explore the features, benefits, and applications of block bottom bags for chemical products, as well as address common questions and provide insights into the latest trends in chemical packaging.
What Are Block Bottom Bags?
Block bottom bags are a specific type of woven polypropylene bag designed with a square or “block” bottom that offers a stable and upright stance. This design ensures that the bag maintains its shape even when filled, making it ideal for stacking and transporting heavy or bulky products. The bag’s rectangular base creates a wider footprint that distributes weight evenly, reducing the risk of toppling and making it easier to store and handle.
These bags are typically used in various industries, including agriculture, chemicals, food, and construction. For chemical products, block bottom bags are particularly valuable due to their ability to handle large quantities of granular or powdered substances while protecting the contents from environmental factors such as moisture, air, and contamination.
Key Features of Block Bottom Bags for Chemical Products
To understand why block bottom bags are a preferred packaging option for chemical products, it’s essential to highlight their key features:
Feature | Description |
---|---|
Material | Made from high-quality woven polypropylene (PP), which provides strength, durability, and resistance to tearing and punctures. |
Design | The block bottom design allows the bag to stand upright, offering better load distribution, stability, and ease of stacking. |
Closure Options | Options include heat-sealed, stitched, or pasted valve closures, ensuring secure sealing for various chemical applications. |
Moisture Resistance | These bags can be treated with water-repellent coatings or laminated with films to enhance moisture resistance, which is crucial for storing chemicals that are sensitive to humidity. |
Customization | Block bottom bags can be customized with different sizes, prints, and colors to meet specific branding and regulatory needs. |
Eco-Friendly | Made from recyclable polypropylene, these bags offer an eco-friendly alternative to other types of packaging, such as plastic drums or metal containers. |
Advantages of Block Bottom Bags for Chemicals
Block bottom bags offer numerous advantages that make them an ideal choice for packaging chemical products:
- Enhanced Stability and Load Capacity: The square bottom design increases the load-bearing capacity and ensures that the bags remain stable during transportation and storage. This feature is particularly important for heavy chemicals, as the risk of spillage or damage is minimized.
- Easy Handling and Storage: Block bottom bags are easy to handle due to their uniform shape and sturdy base. Their ability to stand upright also facilitates stacking and efficient use of warehouse space.
- Cost-Effectiveness: Compared to rigid containers, block bottom bags are more affordable and lightweight, reducing shipping and storage costs. Their bulk-packaging capability further enhances cost-efficiency.
- Protection Against Contamination: For chemical products, it’s crucial to protect the contents from contamination. Block bottom bags can be treated or laminated to prevent moisture infiltration, reduce UV degradation, and offer protection against dirt or dust.
- Customization for Brand Recognition and Compliance: With the ability to print logos, product information, and safety instructions, block bottom bags help in brand visibility while ensuring compliance with regulatory requirements.
Common Chemical Products Packaged in Block Bottom Bags
Block bottom bags are versatile and can accommodate a wide variety of chemical products. Some of the common chemical products that benefit from this packaging include:
- Fertilizers: Granular fertilizers, such as ammonium nitrate or urea, are often packaged in block bottom bags due to their durability and protection against moisture.
- Powdered Chemicals: Chemicals like calcium carbonate, magnesium oxide, or various detergents can be safely transported in block bottom bags, which prevent leakage and contamination.
- Industrial Chemicals: Liquid additives, catalysts, and industrial solvents can be packaged in block bottom bags that are laminated to provide an additional layer of protection.
- Pesticides and Herbicides: The bag’s strong construction helps in securely containing these hazardous chemicals during handling and transportation.
Trends in Chemical Packaging
The chemical industry has seen an increasing demand for more sustainable, safe, and efficient packaging solutions. This trend is also evident in the growing use of block bottom bags for chemical products. Here are some key trends:
- Sustainability: As more companies focus on reducing their environmental footprint, the use of recyclable and eco-friendly materials like polypropylene for packaging is gaining traction. Block bottom bags, being made from PP, offer a sustainable packaging solution as they can be recycled and reused in various applications.
- Tamper-Evident Packaging: Security and tamper-evident packaging are becoming more important for chemical products. Block bottom bags can be designed with tamper-evident features such as adhesive seals or tear strips to ensure the integrity of the product during transportation.
- Customization for Compliance: With increased regulation in the chemical industry, packaging needs to meet specific safety and labeling requirements. Block bottom bags can be customized with labels for hazardous material identification, safety instructions, and regulatory symbols to ensure compliance with international standards.
- Barrier Technology: The use of laminated or multi-layered film technology in block bottom bags enhances the protection of chemicals from moisture, oxygen, and light. This is especially important for sensitive chemicals that require a controlled environment during storage and transportation.
FAQs about Block Bottom Bags for Chemical Products
Q1: What chemicals are best suited for packaging in block bottom bags? Block bottom bags are ideal for packaging a wide range of chemicals, including granular substances like fertilizers, powdered chemicals such as detergents, and liquids like industrial solvents. Their ability to protect against moisture, UV exposure, and contamination makes them suitable for both dry and liquid chemicals.
Q2: Are block bottom bags resistant to environmental factors? Yes, block bottom bags can be treated to enhance their resistance to environmental factors such as moisture, UV rays, and temperature fluctuations. Laminated versions offer superior protection for chemicals that are sensitive to these factors.
Q3: Can block bottom bags be customized for my product? Yes, block bottom bags are highly customizable. They can be manufactured in different sizes and designs, with options for custom printing, color coding, and specific closure types to meet your product and branding needs.
Q4: How do block bottom bags compare to other types of chemical packaging? Compared to rigid containers such as drums or metal cans, block bottom bags are more cost-effective, lightweight, and space-efficient. They are also easier to handle and dispose of, making them a more environmentally friendly alternative.
Q5: Are block bottom bags environmentally friendly? Yes, block bottom bags are made from recyclable polypropylene, making them an environmentally sustainable option for chemical packaging. Furthermore, advancements in biodegradable materials are expected to increase their environmental benefits in the future.
Conclusion
Block bottom bags for chemical products provide a robust and efficient packaging solution for businesses that prioritize stability, safety, and sustainability. Their design offers several advantages, such as easy handling, cost-effectiveness, and the ability to withstand environmental factors. As the chemical industry continues to demand more sustainable and compliant packaging, block bottom bags are positioned as a key player in addressing these needs.
For more insights on how block bottom bags can help improve packaging efficiency and sustainability, check out our article on Block BOPP Bags: Balancing Economic Benefits and Environmental Responsibility. Additionally, learn more about Optimizing Chemical Packaging with Woven Poly Bags: The Videpak Advantage.