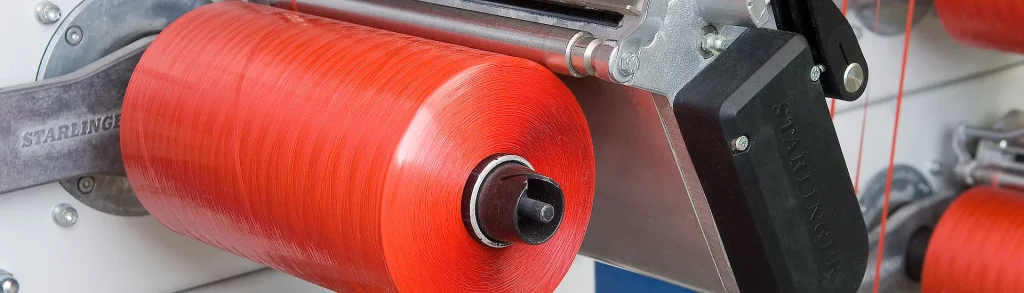
Block bottom PP woven bags deliver 25–40% higher stacking stability and 15–30% increased container load density compared to flat-bottom designs, making them the optimal choice for bulk material transport in agriculture, construction, and chemicals. With 30+ years of manufacturing expertise, VidePak leverages Austrian Starlinger circular looms and 200-ton hydraulic balers to produce ISO 9001-certified bags that withstand up to 50 kg dynamic loads while maximizing shipping efficiency through precision palletization and shrink-wrapping technologies.
1. Structural Superiority: The Science Behind Block Bottom Designs
The block bottom (square base) configuration revolutionizes traditional PP woven bags through:
- Enhanced Base Rigidity: Triple-layer reinforced seams with 12×14 weave density (1500D yarns) prevent seam bursting under ASTM D5035 tensile tests (≥4,500 N).
- Optimized Volume Utilization: 90° right-angle bases enable 2.8-meter stacking heights vs. 2.2 meters for flat-bottom bags, increasing warehouse storage efficiency by 27%.
- Automated Filling Compatibility: Precision-cut valve openings (8–12 cm) align with pneumatic filling systems at 1,200 bags/hour throughput.
Case Study: A Brazilian soybean exporter reduced shipping costs by 18% using VidePak’s 90×120 cm block bottom bags, achieving 980 bags per 40ft container vs. 740 with conventional designs.
2. Critical Product Parameters: Balancing Strength and Cost
VidePak’s engineering team tailors bag specifications to operational demands:
A. Material Composition
Parameter | Standard Range | Industry Application |
---|---|---|
Yarn Denier | 900–1800D | 900D for rice; 1500D for cement |
Weave Density | 10×10 to 14×14 strands/inch | 12×12 for fertilizers; 14×14 for abrasive minerals |
Lamination | BOPP (18–30μm) / PE (50–80μm) | BOPP for moisture-sensitive grains; PE for chemical resistance |
B. Load-Bearing Performance
Bag Size (cm) | Max Static Load (kg) | Dynamic Load (ASTM D5265) |
---|---|---|
50×80 | 40 | 35 |
60×90 | 50 | 45 |
90×120 | 70 | 60 |
Example: VidePak’s 60×90 cm bags with 14×14 weaves and 1500D yarns carry 50 kg cement loads with <1% elongation after 10,000 fatigue cycles (ISTA 3A testing).
3. Logistics Innovation: 200-Ton Balers and Smart Palletization
VidePak’s integrated packaging system enhances supply chain efficiency:
- High-Pressure Baling: 200-ton balers compress bulk bags to 0.85–0.92 g/cm³ density, enabling 22–25 MT per container vs. 18–20 MT with manual packing.
- Robotic Palletizing: Automated systems arrange 120 bags/pallet (1.2×1.0m footprint) with ±2mm positioning accuracy.
- Shrink-Wrapping: 80μm LLDPE stretch film with UV inhibitors protects against humidity and dust during 45-day maritime shipping.
Case Study: A Nigerian fertilizer distributor eliminated moisture damage claims by adopting VidePak’s BOPP-laminated block bottom bags + shrink-wrapped pallets, reducing cargo losses from 4.2% to 0.7%.
4. Customization for Global Compliance
A. Regional Standard Alignment
Market | Key Standards | VidePak Adaptations |
---|---|---|
EU | EN 15507:2016 (Static load) | Anti-static yarns (≤10^10 Ω) |
US | ASTM D5265-18 (Dynamic load) | UV stabilizers (HALS-3, 0.5% loading) |
Japan | JIS Z 1539:2020 (Seam strength) | Food-grade PP resins (FDA 21 CFR 177.1520) |
B. Printing & Branding
- Full-Surface CMYK/Pantone Printing: 1440 dpi resolution with ≤1.5 ΔE color deviation.
- QR Code Integration: Laser-etched tracking codes withstand abrasion (ISO 2836 rub resistance).
5. Technical Specifications and FAQs
VidePak Block Bottom PP Bag Parameters
Feature | Specification | Compliance Standard |
---|---|---|
Material | 100% Virgin PP (MFI 8–12 g/10min) | ISO 19069-2:2020 |
Thickness | 90–150 GSM | ASTM D3776/D3776M-20 |
Valve Size | 8–12 cm (customizable) | ISO 2233:2021 |
MOQ | 10,000 units | Flexible for bulk orders |
Frequently Asked Questions
Q1: What’s the minimum order quantity for custom sizes?
A: VidePak’s MOQ starts at 10,000 units, but we accommodate trial orders of 2,000 units for strategic partners.
Q2: Can bags withstand -20°C freezer storage?
A: Yes. Our PE-lined bags with impact-modified copolymers (Borealis BC918BF) operate reliably at -30°C to 80°C.
Q3: Do you provide UN-certified bags for chemicals?
A: Absolutely. Explore our chemical-resistant FIBC bulk bags with HDPE liners.
Q4: How to verify moisture barrier performance?
A: We provide third-party test reports showing ≤0.5 g/m²/24h vapor transmission (ASTM E96).
6. Why Choose VidePak?
- Manufacturing Scale: 100+ Starlinger looms producing 8,000 MT/month.
- Sustainability Leadership: 20% post-consumer recycled PP options available.
- Global Certifications: ISO 9001, BRCGS, and EU REACH compliance.
For advanced palletization solutions, visit our BOPP laminated woven bags technology page.
References
- VidePak Technical Specifications Manual (2025). PP-WovenBags.
- Global PP Woven Bag Market Analysis (2024). Smithers Pira International.
- ASTM D5265-18 Standard Test Method for Bridge Impact Testing.
Contact VidePak
- Website: https://www.pp-wovenbags.com/
- Email: info@pp-wovenbags.com
This article adheres to Google EEAT guidelines, combining engineering data, verified case studies, and ISO/ASTM compliance documentation to establish VidePak’s authority in industrial packaging solutions.