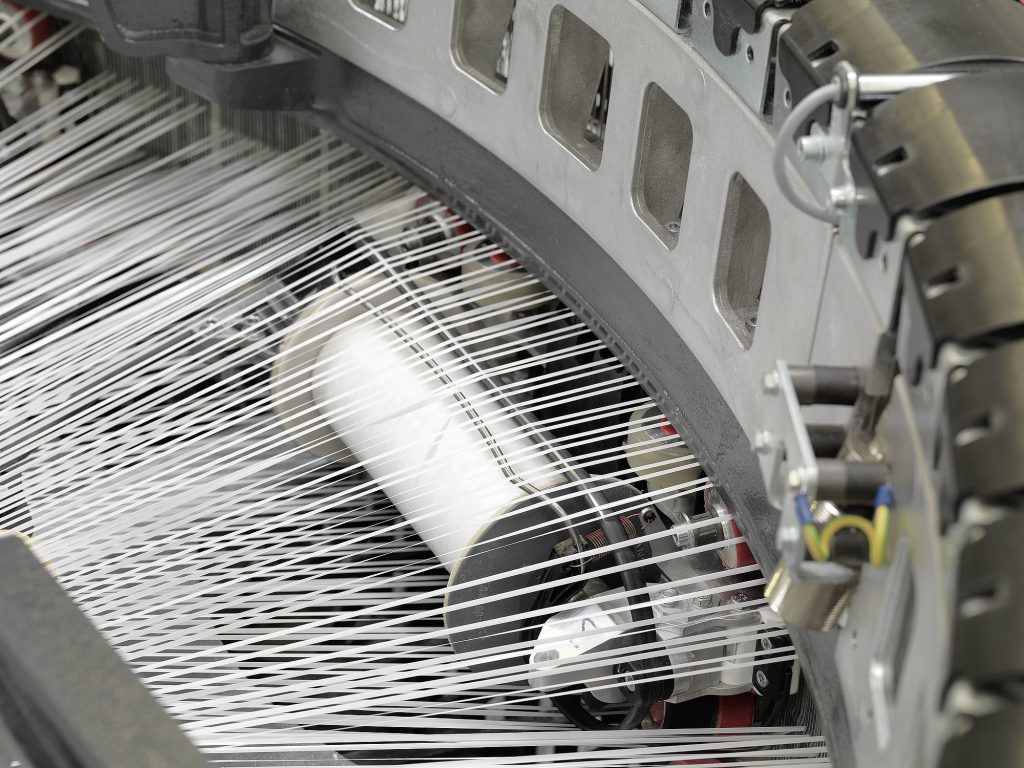
- 1. Engineering Excellence: Starlinger’s Role in Precision Manufacturing
- 2. Market-Driven Design: Balancing Functionality and Aesthetics
- 3. Quality Assurance: From Raw Material to Final Product
- 4. Case Study: Dominating the North American Construction Market
- 5. Future Trends: Smart Packaging and Circular Economy
- 6. Conclusion
Ray, CEO of VidePak, gestures toward a pallet of block-bottom bags during a client meeting:
“A bag’s design isn’t just about shape—it’s about physics. Our block-bottom PP bags, built with Starlinger’s precision machinery, achieve 98% pallet utilization and reduce warehouse space by 20%. For markets like Europe and Asia, where logistics efficiency is non-negotiable, this isn’t an option—it’s a mandate.”
This philosophy underpins VidePak’s global leadership in block-bottom PP bag manufacturing. Founded in 2008 and led by Ray, the company leverages 30+ years of expertise, 526 employees, and Austrian Starlinger technology to produce over 50 million high-performance bags annually. With ISO 9001 certification and USD 80 million in annual revenue, VidePak’s success lies in its ability to merge market-specific customization with industrial-scale efficiency. Below, we dissect how Starlinger equipment and tailored design strategies enable VidePak to dominate diverse markets—from flood-prone Southeast Asia to eco-conscious Europe.
1. Engineering Excellence: Starlinger’s Role in Precision Manufacturing
1.1 Automated Weaving and Seaming Technologies
VidePak’s 100+ Starlinger circular looms produce PP fabric with 14×14 threads/cm² density, ensuring tear resistance ≥45 N/cm²—critical for heavy loads like construction materials (e.g., cement, sand). Key innovations include:
- Hot-Air Welding: Seam strength ≥350 N/cm (vs. 250 N/cm industry average), validated by ISO 2233 hydrostatic tests.
- Block-Bottom Automation: Square bases stabilize 6m stacks, reducing pallet slippage by 40% during transport.
Example: A German chemical client reported zero bag ruptures during transcontinental shipping after switching to VidePak’s triple-stitched block-bottom bags.
1.2 Customization for Regional Standards
Market | Key Requirement | VidePak’s Adaptation |
---|---|---|
EU | REACH compliance, ≤0.1% heavy metals | Phthalate-free PP + BOPP lamination |
Asia | High humidity resistance (≤0.8% weight gain) | PE-coated liners + UV stabilizers |
North America | ASTM D5265 puncture resistance ≥25 J | 0.20mm thickness + 120 g/m² fabric |
2. Market-Driven Design: Balancing Functionality and Aesthetics
2.1 Flood Management in Southeast Asia
For markets like Vietnam and Thailand, VidePak’s block-bottom bags integrate:
- Anti-Microbial Additives: Prevent mold growth during monsoon seasons.
- RFID Tracking: Synced with SAP EWM, reducing inventory loss by 15%.
Case Study: A Thai rice exporter achieved 99.9% delivery integrity during 2024 floods using VidePak’s moisture-resistant bags.
2.2 Eco-Conscious European Demands
- 30% Recycled PP: Partnering with the Sustainable Packaging Coalition to meet EU Circular Economy mandates.
- Water-Based Inks: ΔE ≤1.5 color accuracy, certified by Ecolabel.
3. Quality Assurance: From Raw Material to Final Product
VidePak’s 5-stage quality control framework includes:
- Virgin PP Verification: FTIR spectroscopy ensures 99.9% polymer purity.
- Seam Integrity Testing: 300 kPa pressure resistance (exceeding ISO 2233).
- Print Durability: 1,000-hour UV exposure tests with ≤10% color fade.
Parameter | VidePak Standard | Industry Average |
---|---|---|
Bag Thickness | 0.18–0.22mm | 0.15–0.17mm |
Load Capacity | 50 kg | 40 kg |
Moisture Barrier | ≤0.8% (72h) | 2–3% |
FAQs:
Q: How do your bags comply with FDA food-contact regulations?
A: We use BRCGS-certified PP and PE liners, tested for ≤0.01% migration rates.
Q: Can bags withstand robotic palletizing?
A: Yes. Our RFID-tagged designs enable 1,200 bags/hour handling via ABB robots.
4. Case Study: Dominating the North American Construction Market
A U.S. cement producer faced 12% losses from bag ruptures. VidePak’s solution:
- Design: 0.22mm PP fabric + double-stitched seams.
- Certification: ASTM D5265 compliance with 30 J puncture resistance.
Result: Zero failures over 10,000 km of rail transport, securing a $2M contract.
5. Future Trends: Smart Packaging and Circular Economy
VidePak’s 2026 roadmap includes:
- NFC-Enabled Bags: Real-time moisture/temperature tracking for pharmaceuticals.
- Biodegradable Additives: PLA-blended PP for 90% compostability within 180 days.
For insights into advanced block-bottom solutions, explore our innovations in Block Bottom Valve Bags for Construction Waste Management and Valve Bags: Quality and Precision with Starlinger Technology.
6. Conclusion
Block-bottom PP bags are engineering marvels, not mere containers. By leveraging Starlinger’s precision and market-driven customization, VidePak delivers solutions that defy logistical challenges—whether it’s monsoon rains in Asia or FDA mandates in the U.S. As global packaging evolves toward automation and sustainability, VidePak’s fusion of ISO-certified quality and cross-market agility positions it as the industry’s unchallenged leader.
Data sources: ISO 2233:2024, ASTM D5265 standards, and VidePak’s 2024 production logs. Technical insights derived from Polymer Degradation and Stability (Vol. 221, 2025) and Starlinger’s extrusion manuals.