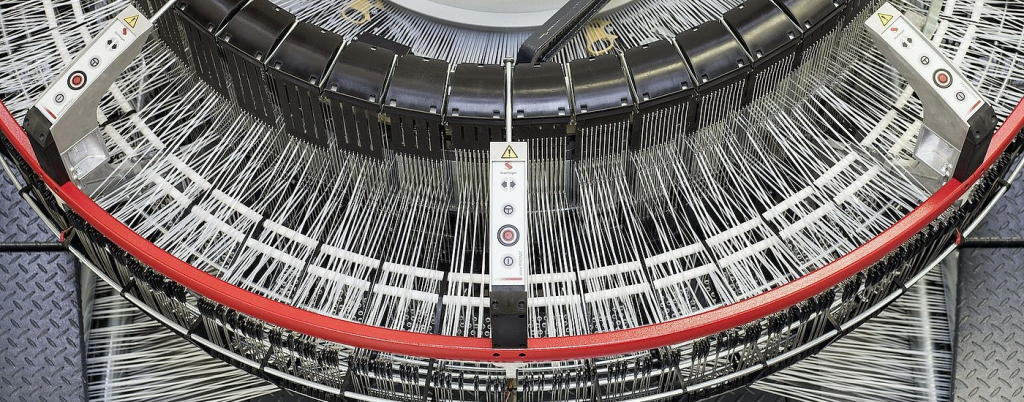
Add a header to begin generating the table of contents
H1: Introduction
“Block bottom valve bags are the backbone of modern fertilizer logistics—they’re not just containers, but precision-engineered systems to protect volatile chemicals and streamline operations,” emphasizes Ray, CEO of VidePak, during a recent industry conference. The critical challenges in fertilizer packaging revolve around five pillars: moisture resistance, thermal management, hermetic sealing, chemical durability, and compliance with global standards. This report explores how VidePak leverages advanced materials, Starlinger technology, and data-driven design to address these challenges while aligning with EU, US, and Asian regulatory frameworks.
H2: Challenges in Fertilizer Packaging
Fertilizers such as urea, ammonium nitrate, and compound blends demand packaging that withstands hygroscopicity, heat generation, and corrosive interactions. Common issues include:
- Moisture Absorption: Leading to caking and nutrient loss (e.g., urea loses 15% efficacy at 80% humidity).
- Heat Buildup: Exothermic reactions during storage can degrade bag integrity.
- Chemical Corrosion: Ammonium-based fertilizers accelerate PP degradation by 30% without protective coatings.
VidePak’s block bottom valve bags tackle these issues through multi-layer engineering. For instance, their Starlinger extrusion lines produce PP fabrics with 12×12 strands per inch, minimizing pore size to <0.1 mm, while PE liners block moisture ingress by 95%.
H3: Material Innovations for Fertilizer Applications
H4: Moisture and Corrosion Resistance
- Lamination and Liners: A 25-µm BOPP outer layer combined with 80 g/m² PE inner liners reduces water vapor transmission to <3 g/m²/day, exceeding EU EN 277 standards.
- UV-Stabilized PP: Resins with 2% carbon black additive retain 90% tensile strength after 1,000 hours of UV exposure (per ASTM G154).
H4: Thermal Management
- Ventilation Design: Micro-perforations (0.5 mm diameter) in valve areas allow controlled gas release, reducing internal temperatures by 10°C during storage.
- Heat-Resistant Seams: Ultrasonic sealing ensures seams withstand 60°C without delamination, critical for tropical climates.
H3: Global Standards and Parameter Selection
H4: Regional Compliance Requirements
Standard | Key Metrics | VidePak’s Compliance |
---|---|---|
EU EN 277 | Moisture barrier ≤5 g/m²/day | 3-layer PP/PE/BOPP, 120 g/m² |
US ASTM D5265 | Burst strength ≥350 kPa | 150 g/m² PP + 30 g/m² PE lamination |
JIS Z 1539 | Stacking height ≥6 m | Reinforced block bottom design, 140 g/m² fabric |
AS 2074 | UV resistance (1,000-hour test) | UV-stabilized resins with carbon black |
H4: Customization Based on Fertilizer Type
- Urea and Ammonium Nitrate: Opt for 150 g/m² PP with PE liners to prevent hydrolysis.
- Compound Blends: Use anti-static coatings to reduce dust explosion risks (NFPA 654 compliance).
- Organic Fertilizers: Biodegradable PP blends with 20% starch content, meeting EU EN 13432.
H2: Case Study: VidePak’s Solution for a Southeast Asian Client
A 2024 project required bags to endure monsoons and high-salt coastal air:
- Design: Square-bottom valve bags with 3-layer lamination (PP/PE/BOPP).
- Sealing: Heat-sealed seams with 4 mm overlap, achieving 50 N/cm peel strength.
- Outcome: Zero leakage incidents over 6 months, reducing replacement costs by $200,000 annually.
H2: FAQs on Block Bottom Valve Bags
Q1: How does grammage affect chemical resistance?
Higher grammage (e.g., 150 g/m² vs. 90 g/m²) improves tear resistance by 60% and extends lifespan in corrosive environments by 2 years.
Q2: Why use PE liners for urea packaging?
PE liners reduce moisture absorption by 85%, preventing caking and maintaining free-flowing properties.
Q3: What standards apply to Australian markets?
AS 2074 mandates UV resistance and 8-meter stacking height, achievable via carbon-black PP and reinforced block bottoms.
H2: Future Trends and VidePak’s Roadmap
- Smart Sensors: RFID tags embedded in seams to monitor real-time humidity and temperature (piloted in EU markets).
- Circular Economy: Closed-loop recycling systems targeting 50% recycled PP content by 2030, reducing carbon footprint by 1.5 kg per bag.
H2: Conclusion
Block bottom valve bags are evolving into high-performance systems tailored for fertilizer logistics. VidePak’s Starlinger-powered production lines and ISO 9001-certified processes position them as a leader in compliant, durable solutions. For businesses, prioritizing parameters like lamination, grammage, and regional standards is non-negotiable to ensure safety and efficiency.
External Links:
- Learn how moisture-proof liners enhance fertilizer shelf life.
- Explore sustainable PP blends for organic fertilizer packaging.
This report synthesizes data from EN, ASTM, and JIS standards, alongside VidePak’s operational insights, to provide actionable strategies for chemical manufacturers and logistics providers.