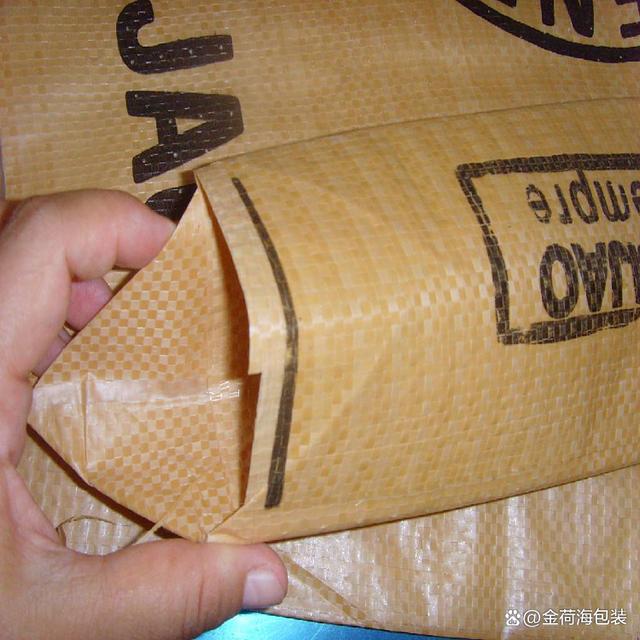
In the ever-evolving world of packaging solutions, Block Bottom Valve Bags have emerged as an essential tool for many industries. Their unique design ensures maximum efficiency in loading, storing, and transporting goods. This article explores the different types of valve mouth configurations in Block Bottom Valve Bags, their applications, and how quality control processes for Valve PP Bags—especially concerning the raw materials like PP and PE pellets—ensure the reliability and longevity of the final products.
Block Bottom Valve Bags and Valve PP Bags have found widespread use across various industries due to their durability, efficiency, and cost-effectiveness. From construction and agriculture to food and chemicals, these bags provide a secure method for packaging both bulk and individual products.
Types of Valve Mouth Configurations in Block Bottom Valve Bags
Block Bottom Valve Bags are designed to accommodate a wide range of valve mouth types, each serving different functional and operational purposes. These valve bags offer users enhanced versatility, efficiency, and storage solutions, contributing significantly to reduced labor and transportation costs. Below are the most common types of valve mouth configurations used in these bags:
- Top Valve (Conical Valve)
One of the most frequently used valve configurations is the top valve. This type features a conical-shaped valve at the top of the bag, which facilitates fast and efficient filling. The conical shape ensures that the bag fills evenly and reduces the chance of material spillage. These bags are typically used for powdered goods, chemicals, and granular materials. - Sewn Valve
The sewn valve is another popular configuration. It involves a valve at the top that is sewn shut after filling. This design ensures that the contents are securely packed within the bag, minimizing the risk of leakage. Sewn valves are commonly found in the packaging of fertilizers, grains, and animal feed. - Paper Valve
Paper valves are typically used when the packaging needs additional protection from the elements. This configuration is often found in Kraft Paper Woven Bags, where the paper valve helps enhance the moisture resistance of the bag. The paper valve provides a strong barrier against both moisture and contaminants, making these bags ideal for food and pharmaceutical products. - Plastic Valve
A plastic valve typically features a flexible and robust design, offering enhanced sealing properties. These valves are commonly used in high-volume packaging applications, including construction materials and chemicals. The plastic valve ensures airtight sealing, preventing any leakage or contamination during transport.
Key Characteristics of Block Bottom Valve Sacks
Beyond the valve configuration, Block Bottom Valve Sacks are designed for various features to suit specific industry needs. These features include:
- Durability: The Block Bottom Valve Bags are made of high-quality woven polypropylene (PP) material, ensuring strength and resilience to wear and tear.
- Customization: These bags offer flexibility in terms of size, shape, and valve placement, which can be tailored to the specific requirements of each client. This includes options for multi-color printing and custom branding.
- Stackability: The block-bottom design makes these bags ideal for stacking. They are built to be stable and sturdy when stacked, which is crucial for efficient storage and transport.
- Sealing Efficiency: The valve mouth allows for quick sealing after filling, making it a popular choice for high-throughput packaging operations.
Quality Control of PP and PE Pellets in Valve Bags
The integrity of Valve Woven Bags is directly linked to the quality of the raw materials used in their manufacturing. A critical aspect of ensuring the reliability of these bags is the careful monitoring and testing of the PP (polypropylene) and PE (polyethylene) pellets that form the core of the woven fabric. Without a proper quality control process, issues such as weak material, poor strength, and inconsistent quality can arise, affecting the overall performance of the bag. Below is an outline of the key parameters that are tested to ensure the highest quality of PP and PE pellets:
1. Appearance Inspection
The first step in quality control involves inspecting the appearance of the pellets. Pellets should be uniform in size, shape, and color. Any inconsistencies, such as discoloration, lumps, or foreign materials, can compromise the bag’s strength and integrity.
2. Melt Flow Index (MFI)
MFI measures the flow rate of melted polymer under specified conditions. It is an essential indicator of the material’s viscosity and its suitability for processing. A high MFI value indicates a low-viscosity material, ideal for certain applications, while a low MFI value indicates a thicker, more robust material. Both PP and PE pellets undergo MFI testing to ensure that the material is within the desired specification for optimal processing in woven bags.
3. Density Measurement
The density of PP and PE pellets plays a critical role in determining their strength and durability. Testing the density helps in understanding the compactness of the material and its resistance to wear. The pellets should have a density within the ideal range to ensure they form a sturdy woven fabric capable of withstanding heavy loads.
4. Tensile Strength and Elongation
Tensile strength tests measure how much force the pellets can withstand before breaking. This is crucial for assessing the strength of the final woven fabric made from these pellets. Along with tensile strength, elongation at break (the amount the material can stretch before breaking) is also measured. A high tensile strength combined with sufficient elongation ensures that the woven bag can handle the stress of packing and transportation without breaking or tearing.
5. Thermal Performance
As polypropylene and polyethylene are thermoplastics, their behavior under different temperature conditions is crucial. Thermal performance tests ensure that the material maintains its structural integrity under both high and low temperatures. This is particularly important for industries that require temperature-resistant bags, such as those used for storing chemicals or food products.
6. Chemical Resistance
Polypropylene and polyethylene pellets must be resistant to a wide range of chemicals, including oils, solvents, and acids. Bags made from these materials must maintain their strength and durability even when exposed to harsh chemicals. Chemical resistance testing helps ensure that the bags are suitable for use in industries like agriculture, chemicals, and construction.
7. UV Resistance
UV degradation is a significant issue in outdoor applications. UV resistance testing ensures that PP Bags and PE Bags are protected from the damaging effects of sunlight. Bags exposed to UV rays without proper protection can weaken, tear, or degrade prematurely, leading to significant losses. UV resistance testing ensures the longevity of the bags in outdoor environments, especially in the agricultural sector.
Summary of Key Quality Parameters for PP and PE Pellets
Property | Description | Ideal Range/Value |
---|---|---|
Appearance | Uniform size, shape, and color | No discoloration, lumps |
Melt Flow Index (MFI) | Flow rate of melted polymer | Specific to bag requirements |
Density | Compactness and strength of material | 0.90–0.92 g/cm³ |
Tensile Strength | Force required to break the material | 30-40 MPa (for PP) |
Elongation at Break | Stretchability before breaking | 5-10% |
Thermal Performance | Stability at high and low temperatures | -10°C to 60°C |
Chemical Resistance | Ability to resist harsh chemicals | Excellent resistance |
UV Resistance | Protection from UV rays | UV stabilized grade |
Conclusion
The Block Bottom Valve Bags are a vital packaging solution for many industries, offering a reliable, durable, and customizable option for packaging bulk materials. The quality of these bags is significantly influenced by the raw materials used in their manufacture. Ensuring the high quality of PP and PE pellets is crucial to maintaining the bags’ strength, durability, and functionality. By following strict quality control protocols—ranging from appearance checks to advanced tests on tensile strength and chemical resistance—manufacturers can deliver products that meet or exceed industry standards, ensuring that the end product provides maximum value to customers.