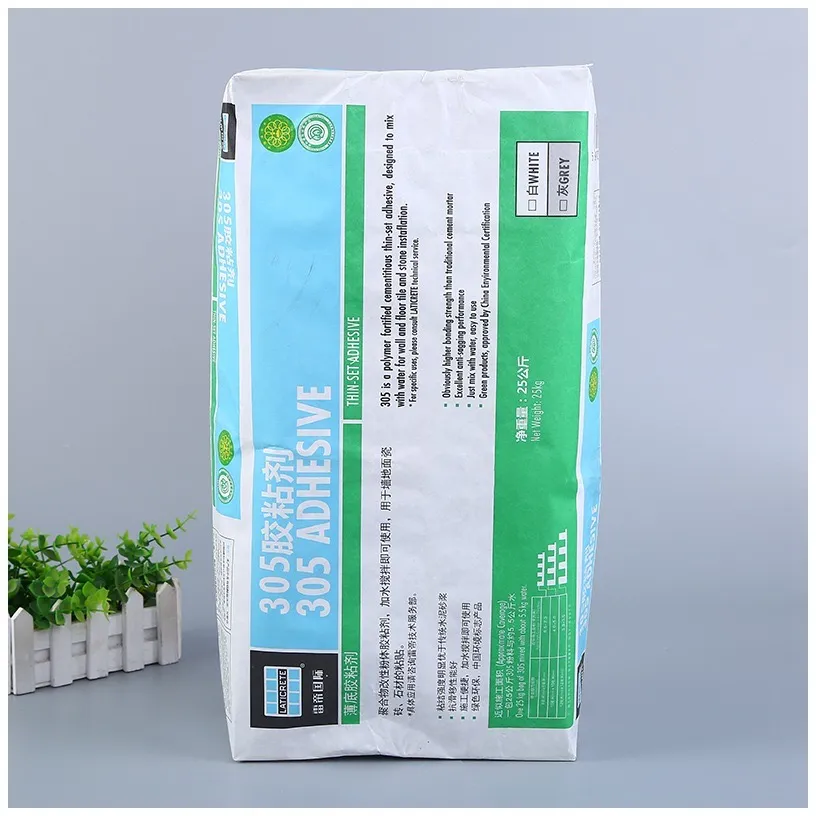
Block Bottom Valve Bags are revolutionizing the packaging industry with their innovative design and advanced manufacturing processes. These bags offer a unique combination of strength, flexibility, and ease of use, making them ideal for a variety of applications. This article provides a comprehensive overview of Block Bottom Valve Bags, their valve types, and the production process that ensures their superior quality and performance.
Understanding Block Bottom Valve Bags
Block Bottom Valve Bags are characterized by their block bottom construction and valve closure system. The block bottom provides a stable base for stacking, while the valve allows for controlled discharge of the contents. These features make them suitable for handling bulk materials such as chemicals, food products, and construction materials.
Valve Types in Block Bottom Valve Bags
The valve design is a critical component of Block Bottom Valve Bags. The main types of valves used include:
- Spout Valve: This is a simple and common type of valve that allows for a controlled flow of the contents.
- Butterfly Valve: Named for its shape, the butterfly valve provides a wide opening for quick and easy discharge.
- Slider Valve: This valve type offers a tight seal and can be opened and closed by sliding a panel.
- Piston Valve: Known for their durability, piston valves provide a controlled and precise flow.
Production Process of Block Bottom Valve Bags
The production process of Block Bottom Valve Bags involves several stages, each of which is executed with precision using state-of-the-art equipment from Starlinger.
Extrusion and Yarn Formation
The process begins with the extrusion of polypropylene (PP) or polyethylene (PE) to form yarns. These yarns are then used in the weaving process to create the fabric for the bags.
Weaving
The yarn is woven into fabric using advanced looms provided by Starlinger. The weaving process can vary, with different techniques such as plain weave, twill weave, and satin weave being used to achieve the desired strength and flexibility.
Cutting and Sewing
The woven fabric is then cut into specific dimensions and sewn to form the bag. This stage also involves the attachment of the valve and the block bottom.
Printing and Coating
Custom printing is applied to the bags during this stage, using special inks that ensure the print is resistant to fading and wear. The bags may also be coated with additional layers for enhanced protection against moisture or chemicals.
Quality Control and Packaging
Each bag undergoes rigorous quality control checks to ensure it meets the required standards for strength, durability, and print quality. The bags are then packaged and prepared for shipment.
Product Parameters of Block Bottom Valve Bags
To ensure the quality and performance of Block Bottom Valve Bags, we adhere to strict product parameters:
Parameter | Description | Importance |
---|---|---|
Material Type | Determines the type of polymer used for the bag’s construction. | Essential for meeting environmental standards and industry requirements. |
Bag Capacity | Measures the volume of material each bag can hold. | Critical for ensuring the bag meets the specific application needs. |
Tensile Strength | Measures the maximum load the bag can withstand before breaking. | Ensures the bag can carry heavy loads without failure. |
Valve Type | Determines the type of valve used for controlled discharge. | Essential for ensuring the bag’s functionality and ease of use. |
Chemical Resistance | Assesses the bag’s resistance to the chemicals it will contain. | Essential for preventing leakage and preserving the contents. |
UV Resistance | Evaluates the bag’s resistance to degradation from UV exposure. | Important for outdoor storage and longevity. |
Print Quality | Measures the clarity and durability of the printed design. | Critical for brand representation and product identification. |
Conclusion
Block Bottom Valve Bags represent a significant advancement in packaging technology, offering a unique combination of strength, functionality, and ease of use. The use of advanced materials and state-of-the-art production techniques ensures that these bags meet the highest standards of quality and performance. As the industry continues to evolve, the commitment to innovation and efficiency remains a priority, ensuring that Block Bottom Valve Bags continue to provide reliable and effective packaging solutions.
For more information on Block Bottom Valve Bags and their production excellence, visit our website: Block Bottom Valve Bags.