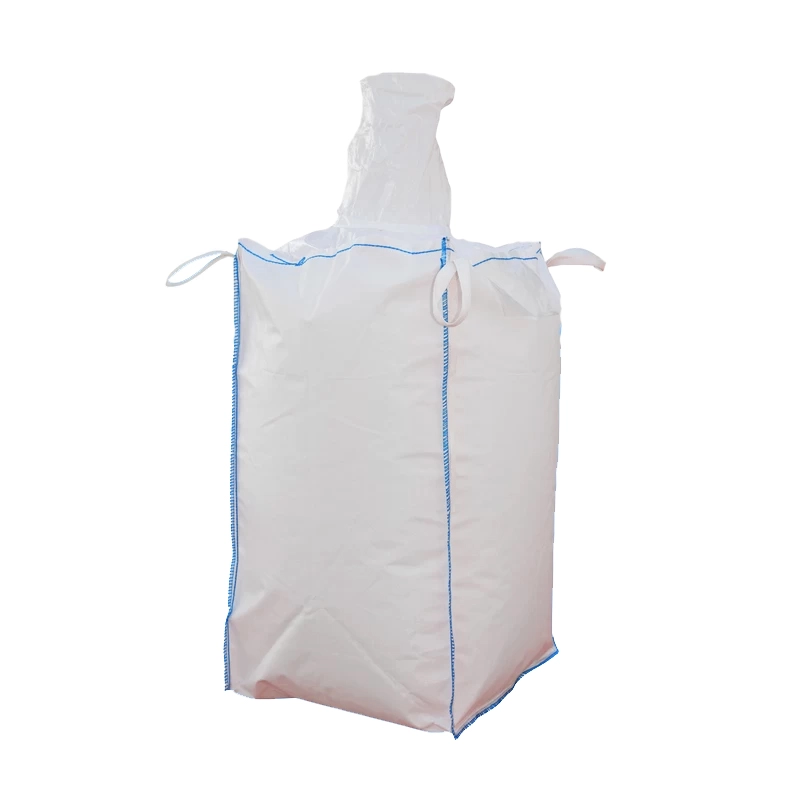
The Role of Anti-Bulge FIBC Bags in Enhancing Load Capacity and Safety
Anti-Bulge FIBC Bags, also known as bulk bags, ton bags, or jumbo bags, play an essential role in modern industrial packaging. These high-strength containers are designed to hold and transport bulk materials securely while mitigating risks such as bursting or deformation during use. The unique design of Anti-Bulge FIBC Bags significantly increases their weight-bearing capacity by improving structural integrity and ensuring even weight distribution.
One of the critical innovations in these bags is their ability to minimize bulging, even under high-stress loads. Traditional FIBC Bags often experience outward expansion when filled, which can compromise safety and lead to breakage. Anti-Bulge FIBC Bags use advanced reinforcement techniques such as internal baffles or multi-layered woven polypropylene (PP) to combat this issue effectively.
The structural enhancement allows these bags to safely carry heavy materials like sand, cement, chemicals, and agricultural products. For example, while standard bulk bags might have a load-bearing capacity of 1,000 kilograms, Anti-Bulge FIBC Bags can handle weights exceeding this without the risk of material leakage or structural failure.
Key Benefits
Features | Advantages | Applications |
---|---|---|
Reinforced corners and sides | Improved weight distribution | Construction materials, grains, and chemicals |
Multi-layered woven PP | Greater tear resistance and load capacity | Mining and heavy industrial materials |
Integrated baffles | Prevents outward bulging and deformation | Fertilizer, powdered products |
Heat-sealed seams | Enhanced safety and reduced spillage | Hazardous and fine-powder substances |
Selecting Optimal Craftsmanship for Anti-Bulge FIBC Bags
To ensure maximum performance and durability, careful consideration must be given to the bag’s production techniques and material specifications. Here are critical factors to consider:
Bottom Construction
The bottom design of an Anti-Bulge FIBC Bag significantly influences its weight capacity and handling characteristics. Commonly employed methods include:
- Cross-corner Loops: These loops provide even weight distribution and make the bags easier to lift with forklifts or cranes.
- Double-stitched Bottoms: For enhanced durability and resistance to tearing.
Sealing Techniques
Proper sealing ensures that FIBC Bags maintain their structural integrity under heavy loads:
- Heat Sealing: Ideal for fine-grain or powdered materials, this technique eliminates weak points in the bag’s seams, ensuring maximum containment.
- Ultrasonic Welding: This advanced technology provides seamless bonding, which is particularly effective in creating leakproof bags. Ultrasonic seams can support greater stress loads and reduce the risk of tears.
- Sewn Seams: While traditional, this method offers flexibility for customization. Stitching density and thread quality are crucial in determining overall strength.
Material and Stitch Density
The thread material and stitch density greatly impact the durability and load capacity of the bag:
Stitch Type | Recommended Thread Material | Applications |
---|---|---|
Lockstitch | High-tenacity polyester thread | Heavy-duty materials such as sand and ore |
Overlock Stitch | UV-stabilized polypropylene thread | Agricultural and chemical products |
Double Overlap Stitch | Multi-filament nylon thread | Hazardous and abrasive materials |
Higher stitch density improves load-bearing performance and minimizes seam failure risks.
Bag Opening Designs
Anti-Bulge FIBC Bags come with various opening styles, each suited to specific operational requirements:
- Open Top: Best for quick filling of non-hazardous materials.
- Spout Top: Facilitates controlled filling, ideal for fine or granular substances.
- Duffle Top: Provides additional closure, suitable for outdoor storage.
- Valve Top: Designed for easy automation during filling processes.
Each design can be enhanced with additional features such as dust-proof sealing or UV protection for extended outdoor use.
Choosing the Best Techniques for Enhanced Performance
Anti-Bulge FIBC Bags are crafted using diverse techniques tailored to specific industrial needs:
Heat Sealing
Heat sealing is the process of joining PP layers using high temperatures, ensuring an airtight seal. This method is particularly advantageous for products that require contamination-free storage, such as food-grade materials or chemicals.
Ultrasonic Welding
Ultrasonic welding uses high-frequency vibrations to fuse PP layers. Its precision and strength make it the go-to choice for heavy-duty applications. This technology is especially effective in high-stress scenarios, as it prevents weak points in the bag’s structure.
Traditional Sewing
While sewing remains a cost-effective method, its effectiveness relies heavily on the choice of thread and stitching density. For example:
- UV-resistant threads improve outdoor durability.
- High-density stitching ensures strength and stability for high-capacity loads.
Conclusion
The performance of Anti-Bulge FIBC Bags depends on the strategic selection of materials, designs, and craftsmanship techniques. By leveraging advancements in manufacturing technologies, these bags provide unparalleled weight-bearing capabilities and safety. Companies seeking superior bulk packaging solutions can rely on Anti-Bulge FIBC Bags to meet their diverse needs efficiently.
For more insights into Anti-Bulge FIBC Bags, visit Advancements in Anti-Bulge FIBC Bags and explore related innovations in bulk bags at The Versatility and Benefits of FIBC Bulk Bags.