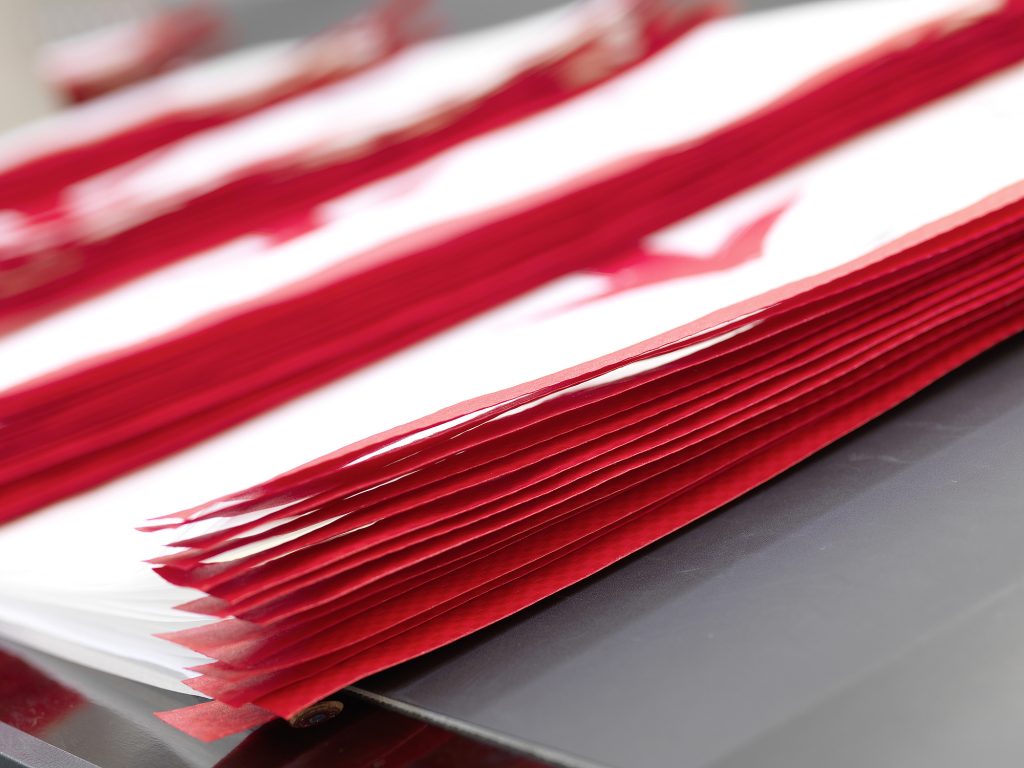
“Why are BOPP valve woven bags revolutionizing industrial storage systems?”
The answer lies in their precision-engineered yarn design and advanced manufacturing processes, which optimize durability, printability, and cost-efficiency—tailored to specific storage needs. At VidePak, leveraging Austrian Starlinger and German W&H machinery, we’ve mastered the art of balancing filament thickness (fine vs. coarse) to deliver bespoke solutions for industries ranging from agriculture to chemicals.
1. Defining Fine and Coarse Filaments in Woven Bags
In polypropylene (PP) woven bag production, filament width directly impacts performance. Industry standards classify filaments as:
- Fine filaments: 1.5–2.5 mm width, typically woven at 120–160 denier.
- Coarse filaments: 3.0–4.5 mm width, woven at 200–300 denier.
VidePak’s Starlinger circular looms achieve ±0.1 mm tolerance in filament extrusion, ensuring consistency critical for load-bearing applications. For instance, coarse filaments used in heavy-duty valve bags for cement storage require 3.2 mm width to withstand 50 kg loads without deformation.
2. Comparative Analysis: Fine vs. Coarse Filaments
2.1 Performance Metrics
Parameter | Fine Filaments | Coarse Filaments |
---|---|---|
Tensile Strength | 25–30 MPa | 35–40 MPa |
Flexibility | High (ideal for contours) | Moderate (rigid structure) |
Surface Smoothness | 8–10 Ra (µm) | 12–15 Ra (µm) |
Print Resolution | 1200 dpi achievable | 600–800 dpi |
Abrasion Resistance | 5,000 cycles (ASTM D4966) | 8,000+ cycles |
Cost per kg | $1.20–$1.50 | $0.90–$1.10 |
Data sourced from ASTM D5265 and VidePak’s 2024 Q3 material testing reports.
Case Study: A Brazilian coffee exporter reduced packaging tears by 40% using VidePak’s fine-filament bags (2.0 mm width), which accommodated irregular bean shapes without compromising print clarity for branding.
2.2 Application-Specific Recommendations
- Fine filaments: Ideal for retail-grade BOPP bags (e.g., pet food, flour) requiring high-resolution printing and lightweight design (≤25 kg loads).
- Coarse filaments: Optimal for industrial storage (e.g., fertilizers, construction materials) where tensile strength and UV resistance outweigh aesthetics.
3. VidePak’s Technological Edge: Starlinger & W&H Machinery
VidePak’s 100+ Starlinger AD*Star looms and W&H extrusion lines enable:
- Precision weaving: 200 RPM speed with <0.5% filament variation, critical for maintaining bag integrity under dynamic loads.
- Multi-layer lamination: Coarse filaments paired with 20-µm BOPP coatings achieve moisture vapor transmission rates (MVTR) of ≤1.0 g/m²/day, meeting ISO 2230 standards for hygroscopic chemicals.
Production Workflow:
- Filament extrusion: W&H lines process virgin PP resin (MFI 2–4 g/10 min) into uniform filaments.
- Weaving: Starlinger looms interlace filaments at 12 picks/cm for coarse yarns vs. 18 picks/cm for fine yarns.
- Valve integration: Automated systems attach PE-coated valves with ±0.3 mm positional accuracy, ensuring airtight seals.
4. Cost-Benefit Analysis and Market Trends
A 2024 McKinsey report highlights that fine-filament bags command a 15–20% price premium but reduce logistics costs by 8% through weight savings. Conversely, coarse-filament designs dominate the $12.3B agrochemical packaging market due to their 10-year lifespan in outdoor storage.
VidePak’s Hybrid Solution:
For a German pesticide manufacturer, we developed dual-filament bags combining 3.0 mm coarse base layers with 2.2 mm fine outer layers. This reduced material costs by 12% while maintaining 1,200 N/5 cm tensile strength—validated by TÜV Rheinland certification.
5. FAQs
Q: How does filament width affect printing quality?
A: Fine filaments enable 1200 dpi prints with ±0.1 mm registration accuracy, whereas coarse filaments limit resolution due to surface texture. VidePak’s 12-color rotary printers mitigate this via adaptive ink viscosity controls.
Q: Are coarse filaments recyclable?
A: Yes. VidePak’s coarse PP filaments are 100% recyclable (ISO 15270 compliant), with a 92% recovery rate in closed-loop systems.
6. Conclusion
The choice between fine and coarse filaments in BOPP valve bags is not merely technical—it’s strategic. VidePak’s integration of Starlinger’s precision and W&H’s material science expertise allows clients to optimize storage efficiency without trade-offs. As e-commerce drives demand for visually striking yet durable packaging, dual-filament innovations will redefine industry standards.
For insights into valve bag engineering, explore our analysis of BOPP valve bags in retail logistics, or discover how Starlinger technology enhances production precision.