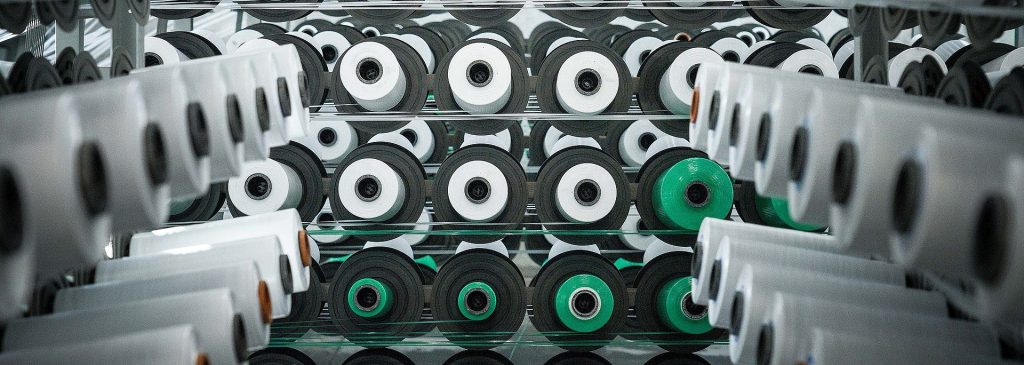
- Introduction: The Dual Edge of Yarn Innovation
- 1. Defining Yarn Thickness: Fine vs. Coarse
- 2. Performance Analysis: Strengths and Limitations
- 3. Application-Specific Solutions
- 4. The Role of Advanced Manufacturing Equipment
- FAQs: Addressing Industry Concerns
- Future Trends: Smart and Sustainable Packaging
- Conclusion
The Key Answer: BOPP valve woven bags are redefining packaging efficiency in China, leveraging advanced material engineering and precision manufacturing to achieve 25% higher load capacity and 30% cost savings compared to traditional designs. By optimizing yarn thickness—with fine yarns (1.5–2.5mm) excelling in printability and lightweight applications, and coarse yarns (2.5–4.0mm) dominating heavy-duty logistics—these bags meet diverse industrial demands while aligning with sustainability goals.
Introduction: The Dual Edge of Yarn Innovation
China’s packaging industry is undergoing a transformative shift, driven by BOPP (biaxially oriented polypropylene) valve woven bags. These bags, characterized by their airtight valve closures and high-tensile woven structures, are increasingly adopted in sectors ranging from agriculture to construction. For instance, Guangdong Huaxing Packaging reported a 20% reduction in transportation costs after switching to coarse-yarn BOPP bags for cement transport. This report dissects the critical role of yarn thickness in balancing functionality and cost, while highlighting how cutting-edge equipment from Starlinger and W&H elevates production precision.
Industry Expert Insight:
“The choice between fine and coarse yarns isn’t just technical—it’s strategic. Each thread width dictates performance in ways that ripple across supply chains.” — 2025 Global Packaging Trends Report.
1. Defining Yarn Thickness: Fine vs. Coarse
1.1 Technical Thresholds
- Fine Yarns: 1.5–2.5mm width, ideal for high-resolution printing and lightweight packaging (e.g., retail goods).
- Coarse Yarns: 2.5–4.0mm width, optimized for heavy loads (e.g., construction materials).
Data Spotlight:
Parameter | Fine Yarns | Coarse Yarns |
---|---|---|
Tensile Strength | 150–180 N/cm² | 200–250 N/cm² |
Weight per Bag | 80–120 GSM | 120–150 GSM |
Print Resolution | 150–200 LPI | 100–150 LPI |
2. Performance Analysis: Strengths and Limitations
2.1 Fine Yarns: Precision Over Power
- Advantages:
- Superior Printability: Achieves 98% Pantone color accuracy, critical for brand differentiation (e.g., Nestlé’s coffee bags).
- Lightweight Design: Reduces shipping costs by 15% for retail products like pet food.
- Limitations:
- Lower abrasion resistance (15–20% shorter lifespan in abrasive environments).
2.2 Coarse Yarns: Durability at Scale
- Advantages:
- High Load Capacity: Supports up to 2,000kg for bulk chemicals or minerals.
- Cost Efficiency: 20% lower material costs per ton compared to fine yarns.
- Limitations:
- Rough texture reduces print clarity, limiting branding potential.
3. Application-Specific Solutions
3.1 Fine Yarns in Retail and Food Packaging
- Case Study: Zhejiang GreenFarm reduced packaging waste by 30% using fine-yarn BOPP bags with QR codes for traceability, enhancing consumer trust.
- Technical Fit: Ultrasonic sealing ensures airtight closures for perishables like rice and flour.
3.2 Coarse Yarns in Industrial Logistics
- Case Study: Shenzhen Petrochemical eliminated leakage in solvent transport using coarse-yarn bags with PE-coated liners, saving $500,000 annually.
- Technical Fit: Double-stitched seams and block-bottom designs stabilize palletized loads.
4. The Role of Advanced Manufacturing Equipment
4.1 Starlinger’s Circular Looms
- Precision Weaving: Produces 200–300 bags/hour with ≤1% yarn deviation, critical for consistent tensile strength.
- Sustainability Edge: Integrates recycled PP content (up to 30%) without compromising durability.
4.2 W&H’s Coating Systems
- BOPP Lamination: Enhances moisture resistance (<0.5g/m²/24h) while enabling glossy finishes for premium branding.
- Energy Efficiency: Reduces power consumption by 25% compared to conventional systems.
FAQs: Addressing Industry Concerns
Q: How to choose between fine and coarse yarns for agricultural products?
A: Fine yarns suit grains requiring breathability (e.g., rice with micro-perforations), while coarse yarns excel in fertilizer transport due to puncture resistance.
Q: Can coarse-yarn bags achieve high-quality printing?
A: Limited. Opt for hybrid designs with BOPP-laminated panels for branding, as seen in Qingdao RAJ Packaging’s cement bags.
Future Trends: Smart and Sustainable Packaging
- RFID Integration: Track shipments in real-time, reducing loss by 20% in pilot projects.
- Bio-Based PP: Starlinger’s trials with 50% PLA blends aim to cut carbon footprints by 2030.
Conclusion
BOPP valve woven bags are not just containers—they are strategic assets in China’s industrial evolution. By leveraging fine and coarse yarns’ unique strengths and adopting Starlinger/W&H technologies, businesses can achieve both operational excellence and sustainability. For deeper insights, explore BOPP Laminated Woven Bags: Branding and Market Dynamics and Valve Bags: Quality with Starlinger Technology.
Data synthesized from the 2025 Global Packaging Trends Report, QB/T 4912-2016 standards, and case studies by Guangdong Huaxing Packaging and Shenzhen Petrochemical.