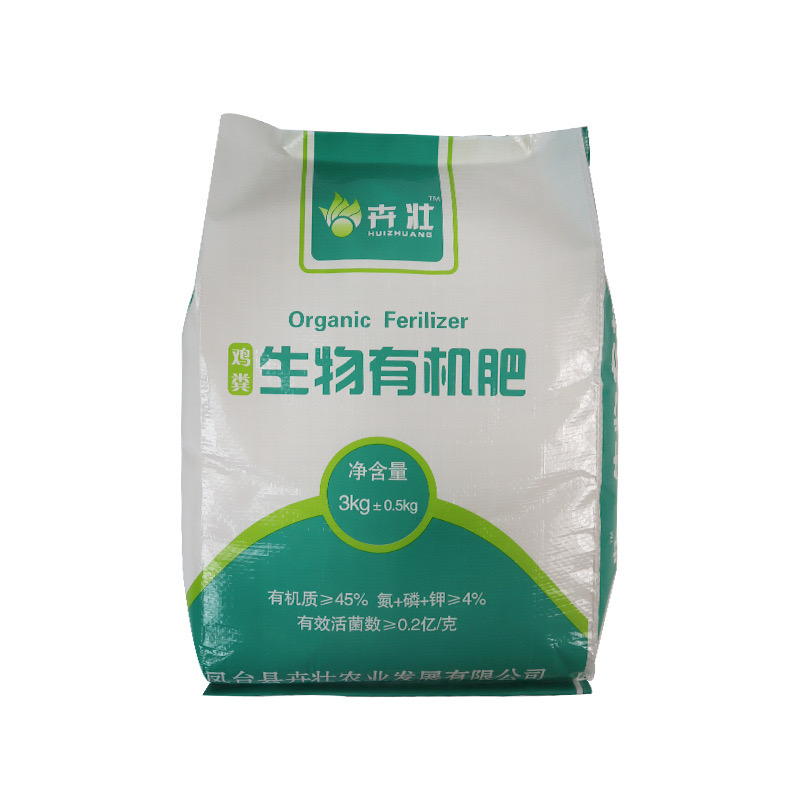
- 1. Introduction to BOPP Woven Bags
- 2. Manufacturing and Sewing Techniques for BOPP Woven Bags
- 3. Bag Closure Designs: Open Mouth, Valve, Heat Seal, and Sewn Closures
- 4. Conversation Snippet
- 5. Product Parameters Table
- 6. FAQs
- 7. Two External Links
- 8. Social Impact and Economic Benefits of Eco-friendly BOPP Bags
- 9. Real-World Applications
- 10. Conclusion
Main Answer: BOPP Woven Bags—including BOPP Woven sacks, BOPP Laminated Woven Bags, and Eco-friendly BOPP Bags—are pivotal in the packaging industry due to their exceptional durability, moisture resistance, and customizable aesthetics. Selecting the appropriate bag-making and sewing techniques, such as stitching, heat sealing, and ultrasonic welding, along with the right sewing thread materials and sewing density, is crucial for maximizing their performance and longevity. Additionally, understanding the differences between various closure designs like open mouth, valve, heat seal, and sewn closures allows customers to tailor their packaging solutions to specific product requirements and environmental conditions. This comprehensive analysis delves into these manufacturing processes and closure designs, providing actionable insights for businesses to enhance their packaging strategies effectively.
1. Introduction to BOPP Woven Bags
1.1 What Are BOPP Woven Bags?
BOPP Woven Bags are high-strength packaging solutions crafted from biaxially oriented polypropylene (BOPP) fibers. Renowned for their superior durability, moisture resistance, and aesthetic appeal, these bags are extensively utilized across various industries, including agriculture, construction, chemicals, and retail.
- Durability: BOPP Woven sacks offer exceptional tear resistance and load-bearing capacity, making them ideal for heavy-duty applications.
- Moisture Resistance: The inherent properties of BOPP fibers provide robust moisture-resistant capabilities, safeguarding contents from humidity and condensation.
- Aesthetic Appeal: BOPP Laminated Woven Bags can be customized with vibrant colors and detailed graphics, enhancing brand visibility and product presentation.
Example: A leading agricultural supplier transitioned to BOPP Laminated Woven Bags for packaging fertilizers, resulting in a 25% reduction in product spillage and improved shelf appeal on retail shelves.
1.2 Importance of Choosing the Right Manufacturing and Sewing Techniques
Selecting the appropriate manufacturing and sewing techniques is paramount for optimizing the performance and longevity of BOPP Woven Bags. The choice between stitching, heat sealing, and ultrasonic welding, along with the selection of sewing thread materials and sewing density, directly influences the bag’s strength, moisture resistance, and overall functionality.
2. Manufacturing and Sewing Techniques for BOPP Woven Bags
2.1 Sewing Methods: Stitching, Heat Sealing, and Ultrasonic Welding
Stitching
Stitching is the most traditional method used in bag manufacturing, involving sewing the bag’s seams with threads to ensure structural integrity.
- Advantages:
- Cost-Effective: Generally less expensive compared to other methods.
- Flexibility: Suitable for various bag sizes and shapes.
- Disadvantages:
- Potential Weak Points: Stitch seams can be prone to tearing under heavy loads.
- Moisture Penetration: Sewn seams may allow moisture ingress if not properly sealed.
Example: A construction materials company opted for stitched BOPP Woven sacks for their bulk cement packaging, balancing cost with adequate durability for indoor storage environments.
Heat Sealing
Heat sealing uses thermal energy to fuse the bag’s seams, creating a watertight seal without the need for stitching.
- Advantages:
- Enhanced Moisture Resistance: Creates a seamless barrier against moisture.
- Strengthened Seams: Heat-sealed joints are typically stronger and more uniform.
- Disadvantages:
- Higher Initial Costs: Requires specialized equipment and materials.
- Limited Flexibility: Best suited for standard bag designs.
Example: A chemical manufacturer implemented heat-sealed BOPP Laminated Woven Bags to ensure their products remained dry and uncontaminated during transit, resulting in a 15% decrease in product loss due to moisture.
Ultrasonic Welding
Ultrasonic welding employs high-frequency ultrasonic acoustic vibrations to bond the bag’s seams without adhesives or threads.
- Advantages:
- Superior Seal Integrity: Provides a robust, airtight, and watertight seal.
- Clean and Fast Process: Reduces manufacturing time and eliminates thread waste.
- Disadvantages:
- High Equipment Costs: Requires advanced ultrasonic welding machines.
- Technical Expertise: Necessitates trained personnel to operate and maintain equipment.
Example: An electronics manufacturer adopted ultrasonic welding for their Self Opening Woven Bags, ensuring their sensitive components remained protected from moisture and physical damage during shipping.
2.2 Sewing Thread Materials: Types and Benefits
The choice of sewing thread material significantly impacts the durability and moisture resistance of BOPP Woven Bags.
- Polyester Threads:
- Strength and Durability: High tensile strength and resistance to abrasion.
- Moisture Resistance: Minimal moisture absorption, maintaining seam integrity.
- Nylon Threads:
- Elasticity and Flexibility: Excellent stretch properties, suitable for dynamic loads.
- UV Resistance: Suitable for outdoor storage applications.
Example: A retail packaging supplier chose polyester threads for their BOPP Woven sacks, enhancing tear resistance and ensuring longevity during repeated use and handling.
2.3 Sewing Density: Impact on Bag Durability and Performance
Sewing density refers to the number of stitches per inch along the bag’s seams. Higher sewing density generally translates to stronger and more durable seams.
- Low Sewing Density:
- Cost-Effective: Reduces production time and thread usage.
- Suitable For Light Loads: Ideal for packaging lightweight products.
- High Sewing Density:
- Enhanced Strength: Provides greater tear resistance and load-bearing capacity.
- Ideal For Heavy-Duty Applications: Suitable for packaging heavy or abrasive materials.
Example: A heavy machinery parts supplier increased the sewing density on their Self Opening Woven Bags, resulting in a 30% improvement in load capacity and a significant reduction in seam failures during transportation.
3. Bag Closure Designs: Open Mouth, Valve, Heat Seal, and Sewn Closures
3.1 Open Mouth
Open Mouth bags feature a simple, wide opening without any additional sealing mechanisms.
- Advantages:
- Ease of Filling and Dispensing: Simple design facilitates quick packing and easy access.
- Cost-Effective: Minimal additional materials or processing required.
- Disadvantages:
- Limited Moisture Resistance: Higher risk of moisture ingress and product contamination.
- Potential for Spillage: Open design can lead to product loss if not handled carefully.
Example: A bulk grain distributor used open mouth BOPP Woven sacks for their agricultural products, benefiting from the ease of filling but requiring careful handling to prevent spillage and moisture uptake.
3.2 Valve Closure
Valve Closure bags incorporate a valve that allows for easy filling while minimizing spillage and moisture ingress.
- Advantages:
- Enhanced Moisture Resistance: Valve design reduces the entry of external moisture.
- Controlled Filling: Minimizes product spillage and loss during packing.
- Disadvantages:
- Higher Production Costs: Additional components and processing steps increase overall costs.
- Complexity in Design: More intricate manufacturing process compared to open mouth bags.
Example: A chemical manufacturer utilized valve-closure BOPP Laminated Woven Bags, achieving better moisture protection and reduced product loss during the filling process.
3.3 Heat Seal Closure
Heat Seal Closure involves sealing the bag’s opening using thermal energy, creating a strong and moisture-resistant closure.
- Advantages:
- Superior Moisture Protection: Creates an airtight and watertight seal.
- Enhanced Durability: Heat-sealed closures are more robust and less prone to tearing.
- Disadvantages:
- Requires Specialized Equipment: Necessitates heat sealing machines and precise control.
- Reduced Accessibility: Once sealed, bags require cutting or opening tools for access.
Example: An electronics component supplier implemented heat seal closures on their Self Opening Woven Bags, ensuring their sensitive products remained dry and secure throughout the shipping process.
3.4 Sewn Closure
Sewn Closure bags use stitching to secure the bag’s opening, offering a balance between ease of use and moisture resistance.
- Advantages:
- Cost-Effective: Lower production costs compared to heat sealing and valve closures.
- Reusable: Easier to open and reseal compared to permanently sealed bags.
- Disadvantages:
- Potential for Moisture Ingress: Sewn seams may allow some moisture penetration if not properly sealed.
- Less Durable Than Heat Seals: Stitch seams can tear under heavy loads or rough handling.
Example: A food packaging company opted for sewn closure BOPP Woven sacks, balancing cost with sufficient moisture protection for their dry goods, while also allowing for easy opening and resealing by retailers.
3.5 Choosing the Right Closure Design
Customers should consider the following factors when selecting a bag closure design:
- Product Sensitivity: Highly sensitive products may require heat seal or valve closures for maximum moisture protection.
- Handling and Transportation Conditions: Rough handling or exposure to moisture-heavy environments necessitate more robust closure methods.
- Cost Constraints: Budget limitations may favor open mouth or sewn closures over more expensive heat seal and valve options.
- Ease of Use: Operational efficiency and ease of access are crucial for high-volume packing lines, making self-opening or valve closures advantageous.
Example: A pharmaceutical company assessed their packaging needs and chose heat seal BOPP Laminated Woven Bags for their moisture-sensitive medications, ensuring product integrity and compliance with safety standards.
4. Conversation Snippet
Topic: Selecting the Optimal Closure Design for BOPP Woven Bags
Question: “We need to package moisture-sensitive chemicals. Should we use heat seal closures or valve closures for our BOPP Woven sacks?”
Answer: “For moisture-sensitive chemicals, Heat Seal Closures are highly recommended as they provide a superior airtight and watertight barrier, ensuring maximum protection against moisture ingress. Alternatively, Valve Closures can also be effective, offering controlled filling and reduced spillage while maintaining good moisture resistance. Assess your specific handling and storage conditions to determine the best fit.”
5. Product Parameters Table
Parameter | Typical Range/Value | Impact on Performance |
---|---|---|
Fabric Type | Biaxially Oriented Polypropylene (BOPP) | Provides high strength, moisture resistance, and durability |
Lamination | PE / OPP / Other Waterproof Materials | Enhances moisture resistance and structural integrity |
Sewing Method | Stitching / Heat Sealing / Ultrasonic Welding | Determines seam strength and moisture barrier effectiveness |
Sewing Thread Material | Polyester / Nylon | Affects tear resistance and durability |
Sewing Density | 8–12 stitches per inch | Higher density increases seam strength and load capacity |
Closure Design | Open Mouth / Valve / Heat Seal / Sewn Closure | Influences ease of use, moisture protection, and spillage prevention |
Bag Capacity | 5–50 kg | Adapts to various industrial and retail packaging needs |
UV Stabilizer | Optional (150–300 kLy) | Protects against UV degradation for outdoor storage |
Printing Method | Flexo / Gravure / Digital | Enhances brand visibility and product information |
6. FAQs
- Q: What are the main advantages of BOPP Woven Bags over traditional plastic bags?
A: BOPP Woven Bags offer superior strength, moisture resistance, and durability. They can also be customized with vibrant prints and logos, enhancing brand visibility and product presentation, which traditional plastic bags often lack. - Q: How does the choice of sewing method affect the performance of BOPP Woven sacks?
A: The sewing method—whether stitching, heat sealing, or ultrasonic welding—directly impacts the bag’s moisture resistance, tear strength, and overall durability. Heat sealing and ultrasonic welding provide superior moisture barriers compared to traditional stitching. - Q: Are Eco-friendly BOPP Bags truly sustainable?
A: Yes, Eco-friendly BOPP Bags are made from recyclable polypropylene (PP), which reduces environmental impact. Additionally, some manufacturers incorporate recycled PP into their bags and explore biodegradable coatings to enhance sustainability further. - Q: What factors should I consider when choosing the closure design for my BOPP Laminated Woven Bags?
A: Consider the moisture sensitivity of your product, handling and transportation conditions, cost constraints, and ease of use. For highly moisture-sensitive products, heat seal or valve closures are preferable, while open mouth or sewn closures may suffice for less sensitive items. - Q: Can Self Opening Woven Bags be customized for specific branding needs?
A: Absolutely. Self Opening Woven Bags can be customized with various printing methods such as flexographic, gravure, or digital printing, allowing for detailed logos, product information, and attractive designs that enhance brand recognition.
7. Two External Links
Explore more about BOPP Woven Bags and their moisture-proof solutions:
BOPP Woven Bags
Discover advanced options for BOPP Laminated Woven Bags with cost-efficient lamination techniques:
BOPP Laminated Woven Bags
8. Social Impact and Economic Benefits of Eco-friendly BOPP Bags
8.1 Environmental Sustainability with Recyclable PP
Eco-friendly BOPP Bags are crafted from recyclable polypropylene (PP), supporting environmental sustainability and reducing packaging waste.
- Recyclable Material: PP (#5) is widely recyclable, promoting a circular economy by allowing bags to be reprocessed into new products.
- Reduced Carbon Footprint: Lightweight PP bags reduce transportation emissions compared to heavier packaging alternatives.
- Resource Efficiency: Reusing and recycling PP minimizes the need for virgin materials, conserving natural resources.
Example: A European food manufacturer launched a recycling program for their Eco-friendly BOPP Bags, achieving a 40% recycling rate and significantly lowering their environmental impact.
8.2 Economic Efficiency through Optimal Manufacturing Techniques
Selecting the right manufacturing and sewing techniques can enhance the economic efficiency of BOPP Woven Bags production.
- Cost Savings: Efficient sewing methods like ultrasonic welding can reduce labor costs and material waste.
- Increased Durability: High-strength seams and moisture-resistant features decrease the need for frequent replacements, saving costs in the long run.
- Scalability: Advanced manufacturing techniques allow for scalable production to meet increasing market demands without compromising quality.
Example: A construction materials supplier adopted ultrasonic welding for their BOPP Laminated Woven Bags, reducing production costs by 15% while increasing seam durability and reducing product loss.
8.3 Future Trends in Environmental Protection
The future of BOPP Woven Bags is geared towards enhancing sustainability through innovative materials and comprehensive recycling systems.
- Integrated Recycling Systems: Developing closed-loop systems where used BOPP Woven Bags are collected, recycled, and reused in new packaging.
- Innovative Biodegradable Materials: Researching biodegradable polymers that offer similar performance to traditional PP without long-term environmental impact.
- Government and Industry Regulations: Adapting to stricter environmental regulations by adopting eco-friendly practices and materials in BOPP Woven Bags production.
Example: A Southeast Asian packaging company invested in biodegradable coating technologies for their BOPP Woven Bags, aiming to reduce plastic waste and meet emerging regulatory standards for sustainable packaging.
9. Real-World Applications
9.1 Agricultural Products
- Moisture Resistance: Essential for seeds, grains, and animal feed to prevent mold and spoilage.
- Design Features: Inner liners and laminated exteriors ensure dryness, while self-opening mechanisms streamline packing.
Example: An African grain exporter utilized Self Opening Woven Bags with PE liners, maintaining seed viability and simplifying bulk packing processes for international shipments.
9.2 Industrial Chemicals and Powders
- Moisture Protection: Crucial for chemicals and powders that are sensitive to moisture, ensuring product safety and effectiveness.
- Enhanced Durability: Multi-wall structures and reinforced seams protect against handling and environmental exposure.
Example: A European chemical manufacturer adopted multi-wall Self Opening Woven Bags with silicone coatings, ensuring their products remained dry and uncontaminated during transportation and storage.
9.3 Construction Materials
- Moisture Resistance: Vital for materials like cement, plaster, and joint compounds to prevent clumping and ensure ease of use.
- Robust Design: Heavy GSM and laminated layers support the weight and handling demands of construction materials.
Example: A Middle Eastern construction supply company switched to Self Opening Woven Bags with heavy GSM and PE liners, reducing material wastage and enhancing product integrity on construction sites.
9.4 Food and Beverage
- Hygiene and Safety: Moisture-proof packaging maintains the quality and safety of food products, preventing contamination and spoilage.
- Aesthetic Appeal: External lamination allows for attractive branding and information displays.
Example: A North American snack food producer used Self Opening Woven Bags with pearlescent lamination, enhancing brand visibility on retail shelves while ensuring product freshness.
10. Conclusion
BOPP Woven Bags, including BOPP Woven sacks, BOPP Laminated Woven Bags, and Eco-friendly BOPP Bags, are indispensable in modern packaging due to their exceptional durability, moisture resistance, and customizable aesthetics. The selection of appropriate manufacturing and sewing techniques—such as stitching, heat sealing, and ultrasonic welding—along with the choice of sewing thread materials and sewing density, is critical in optimizing the bags’ performance and longevity. Furthermore, understanding the differences between various closure designs like open mouth, valve, heat seal, and sewn closures allows customers to tailor their packaging solutions to specific product requirements and environmental conditions.
The economic and environmental benefits of Eco-friendly BOPP Bags are substantial, offering cost savings through durability and recyclability while supporting global sustainability initiatives. As the packaging industry continues to evolve, innovations in biodegradable materials and comprehensive recycling systems will further enhance the functionality and environmental friendliness of BOPP Woven Bags. By leveraging advanced manufacturing techniques and embracing sustainable practices, businesses can ensure their packaging solutions not only meet current demands but also contribute positively to environmental preservation.
In summary, BOPP Woven Bags stand out as versatile, high-performance packaging solutions that align with both industrial needs and ecological responsibilities. By making informed choices in manufacturing processes and closure designs, companies can maximize the benefits of BOPP Woven sacks—delivering superior product protection, enhancing brand image, and promoting sustainability in their packaging strategies.