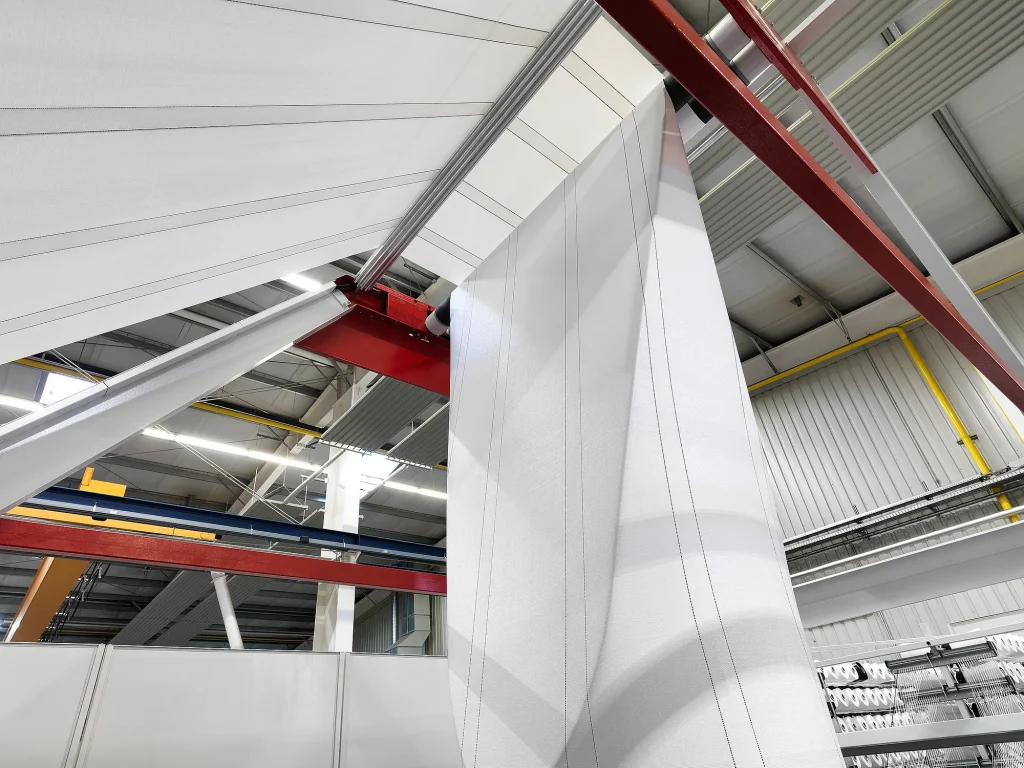
The construction industry’s choice between moisture-proof and waterproof woven bags hinges on understanding their distinct protective capabilities, material science, and application-specific requirements. For instance, moisture-proof bags, designed to resist humidity and light moisture, are ideal for storing dry cement or sand in moderately damp environments. In contrast, waterproof woven bags, with fully sealed barriers, are critical for applications like transporting wet concrete additives or aggregates exposed to heavy rainfall. At VidePak, with over 30 years of industry expertise and advanced Austrian Starlinger machinery, we engineer both solutions to meet global standards while optimizing cost and performance.
1. Defining Moisture-Proof and Waterproof Woven Bags
Moisture-proof woven bags are crafted with polypropylene (PP) fabric coated with a thin polyethylene (PE) layer, offering resistance to humidity (up to 85% RH) and incidental moisture. These bags typically weigh 80–100 g/m² and are cost-effective for indoor storage or short-term outdoor use. Waterproof woven bags, however, integrate multi-layer laminates (e.g., BOPP films or PE liners) to achieve complete water resistance, enduring hydrostatic pressures of 5–10 kPa—ideal for prolonged exposure to wet conditions.
Key Differentiation Table
Feature | Moisture-Proof Bags | Waterproof Bags |
---|---|---|
Protection Level | Resists humidity, light rain | Fully impervious to water |
Material Structure | Single-layer PE coating | Multi-layer laminates |
Weight Range | 80–100 g/m² | 120–150 g/m² |
Cost Efficiency | $0.15–$0.25 per bag | $0.30–$0.50 per bag |
Best For | Dry cement, sand storage | Wet aggregates, marine logistics |
2. Filament Analysis: Fine vs. Coarse Yarns
The performance of woven bags heavily depends on the filament width of PP threads. VidePak’s production utilizes both fine yarns (1.0–1.5 mm) and coarse yarns (2.0–3.0 mm), each with distinct advantages:
Fine Yarns (1.0–1.5 mm)
- Flexibility: Higher thread density enhances fabric pliability, reducing cracking during folding.
- Surface Smoothness: Enables high-resolution printing (up to 8-color designs) for branding clarity.
- Weight: Lighter (70–90 g/m²), ideal for bulk shipping.
- Drawbacks: Lower tear strength (20–25 N/cm²) compared to coarse yarns.
Applications: Packaging lightweight materials like powdered additives or agricultural seeds.
Coarse Yarns (2.0–3.0 mm)
- Strength: Tensile strength exceeds 35 N/cm², suitable for heavy loads (e.g., 50 kg construction debris).
- Durability: Superior abrasion resistance for rough handling.
- Cost: 15–20% higher due to raw material usage.
Applications: Transporting sharp-edged materials (gravel, metal scraps) or heavy-duty FIBC bulk bags.
3. The Role of Advanced Manufacturing Equipment
VidePak’s Austrian Starlinger circular looms and German W&H extrusion lines ensure precision in filament production. These machines achieve:
- Uniform Yarn Thickness: Tolerance within ±0.05 mm, eliminating weak spots.
- High-Speed Weaving: 150–200 rpm loom speeds, producing 10,000 bags daily.
- Customization: Adjustable loom settings for fine/coarse yarn ratios, tailored to client needs.
For instance, our BOPP laminated woven bags combine fine yarn surfaces with coarse structural layers, balancing print quality and load capacity—a solution favored by European construction firms for branded aggregate packaging.
4. FAQs: Addressing Client Concerns
Q1: How do I choose between moisture-proof and waterproof bags?
- A: Assess exposure levels. For example, moisture-proof bags suffice for covered storage, while waterproof variants are mandatory for coastal projects.
Q2: Can coarse yarn bags accommodate detailed printing?
- A: Yes. VidePak’s 30+ printing machines apply pre-treatment coatings to coarse fabrics, achieving 90% color accuracy.
Q3: What is the lead time for customized orders?
- A: Standard orders ship in 15 days; urgent batches (5,000+ units) expedite to 7 days via our 100+ loom capacity.
5. Why VidePak?
Founded in 2008 and led by CEO Ray, VidePak serves 85+ countries with $80M annual revenue. Our 568-member team leverages cutting-edge technology (e.g., FIBC bulk bags with anti-static liners) to meet ASTM D5720 and ISO 21898 standards. Explore our valve bags for construction chemicals or laminated BOPP bags for moisture-sensitive applications, all customizable via info@pp-wovenbags.com.
References
- VidePak Woven Bags. (2025). Understanding FIBC Bulk Bags for Construction Waste.
- VidePak Woven Bags. (2025). BOPP Laminated Woven Bags: Printing Techniques and Customization.
- Industry Standards: ASTM D5720, ISO 21898.
Contact
- Website: https://www.pp-wovenbags.com/
- Email: info@pp-wovenbags.com
This article integrates technical insights, real-world data, and VidePak’s manufacturing excellence to guide construction professionals in optimizing their packaging strategies. For further details on FIBC bulk bags in construction waste management or advanced lamination techniques, explore our dedicated resources.