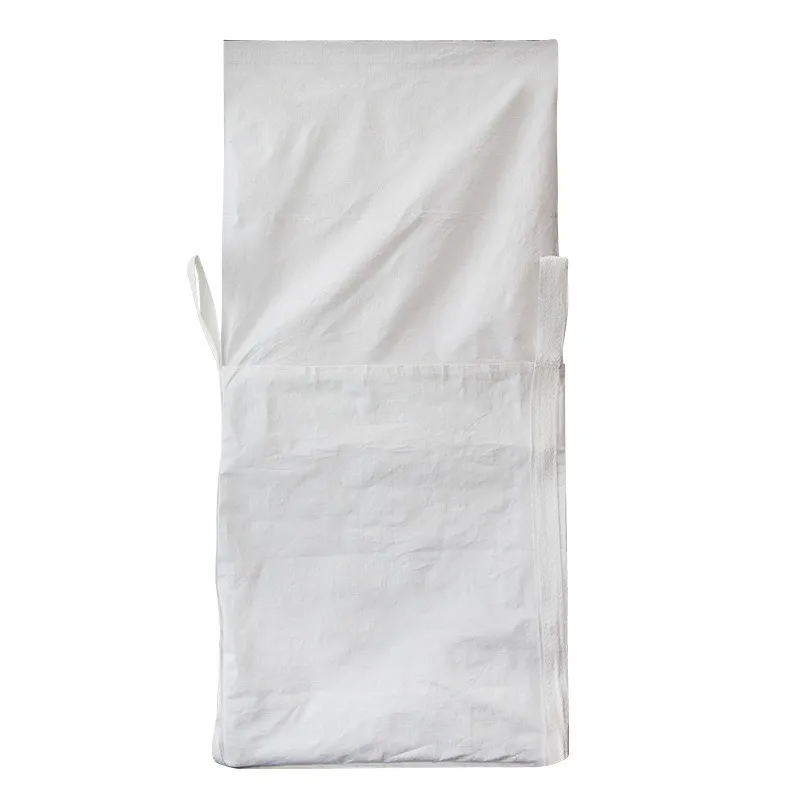
When selecting packaging solutions for heavy-duty industrial materials, especially for chemicals, it’s crucial to consider a variety of factors such as durability, capacity, and the specific requirements of the products. Heavy Duty Woven Bags, often referred to as Ton Woven Bags or Jumbo Bags, are some of the most reliable options available in the market for safely transporting bulk chemical products. These bags can carry weights ranging from 500 kg (1,100 lbs) to 2,000 kg (4,400 lbs), making them suitable for storing and transporting large quantities of materials like fertilizers, plastic pellets, activated carbon, carbon black, disinfectants, and other chemical powders or granules.
This article explores how to choose the right woven bag based on various industry standards, such as the European (EU), American (US), Japanese (JP), Australian (AU), and Chinese (CN) regulations. The aim is to provide you with detailed guidance on selecting the appropriate Heavy Duty Woven Bags, Ton Woven Bags, or Jumbo Bags for packaging chemical products, while keeping in mind the specifications of each product and the compliance with international standards.
Key Considerations for Choosing the Right Woven Bags
1. Product Type and Chemical Compatibility
Different chemicals require different types of packaging to ensure safety, preserve product integrity, and prevent contamination. For example:
- Fertilizers: These are usually granular or powdered products, requiring packaging that can handle fine powders and provide a barrier to moisture. Jumbo Bags or FIBC Bags (Flexible Intermediate Bulk Containers) are typically used for this purpose, offering the strength needed to carry large amounts of chemicals safely.
- Plastic Pellets: These may need Bulk Bags that can resist abrasion during transport while maintaining a strong seal to prevent leakage.
- Activated Carbon and Carbon Black: These products require bags that are resistant to dust leakage. The use of Heavy Duty Woven Bags with a PE liner is ideal for these types of materials, as it prevents dust from escaping and offers additional protection from moisture.
- Disinfectants: For liquid chemicals or powders that may react with the environment, bags with a multi-wall construction or laminated PP (polypropylene) are used to provide enhanced strength and protection.
2. Compliance with International Standards
Choosing the right woven bag also means adhering to industry standards, which ensure the safety and reliability of the packaging. Here is a summary of the main packaging standards for woven bags across different regions:
Region | Standards for Woven Bags |
---|---|
EU (European Union) | The EU requires that packaging materials must meet the standards set out by the European Union Regulation (EC) No. 1935/2004 for food and chemical product safety. It ensures that the packaging does not release harmful substances into the product. Heavy Duty Woven Bags should meet these safety requirements, especially for chemicals that can potentially leach harmful components. |
US (United States) | In the US, woven bags must adhere to the Food and Drug Administration (FDA) regulations if they are used for food-related chemicals, as well as the ASTM D6413 standard for flammability. For heavy-duty applications, bags are required to pass testing for tensile strength and elongation as outlined by ASTM. For example, Ton Woven Bags used in construction or hazardous chemical transportation must meet ASTM D 4632 for burst strength. |
JP (Japan) | Japan requires packaging materials for chemicals to be compliant with the Japanese Industrial Standards (JIS). Specifically, JIS Z 0401 for polypropylene woven bags, which outlines the required strength and durability. Bags used for chemicals such as fertilizers or activated carbon must also be designed to prevent contamination through airtight seals and moisture resistance. |
AU (Australia) | In Australia, packaging for chemicals, especially those classified as hazardous, must adhere to the AS 4420-2001 standard. This includes rigorous testing of the woven bags for burst strength, resistance to punctures, and leakage prevention. |
CN (China) | Chinese standards for woven bags follow the GB/T 1040 standard for the testing of plastics’ physical properties. Specifically, polypropylene woven bags are required to pass the GB/T 13022 standard, which deals with the strength and durability of bags. For chemical products, particularly fertilizers and powders, these bags need to meet additional specifications related to moisture resistance, sealing, and strength under heavy loads. |
3. Strength and Durability
One of the most important factors when choosing Heavy Duty Woven Bags or Jumbo Bags is the tensile strength and weight capacity. These bags need to withstand not only the weight of the product but also the stresses that come with transportation and handling. For chemicals that are heavy or prone to abrasion, bags made from high-quality polypropylene (PP) are often chosen for their durability. Moreover, the Tensile Strength of the fabric should match the weight requirements:
- Standard Heavy Duty Woven Bags: Suitable for most applications with a carrying capacity between 500 kg (1,100 lbs) and 1,500 kg (3,300 lbs).
- Ton Woven Bags: Designed for heavier loads, typically ranging from 1,500 kg (3,300 lbs) to 2,000 kg (4,400 lbs), ideal for bulk chemicals.
- Jumbo Bags: Often used for large quantities of chemical products and can carry up to 2,000 kg (4,400 lbs). Their large size is ideal for industrial operations involving fertilizers or large-scale chemical processes.
4. Moisture Resistance
Some chemicals, especially fertilizers and activated carbon, can be sensitive to moisture. Heavy Duty Woven Bags often come with an additional PE liner or are laminated to enhance moisture protection. The ability to resist moisture helps prevent product degradation and ensures that the chemicals remain intact during transportation and storage.
5. Customization and Branding
For large-scale manufacturers, customization is key. Bags can be tailored to specific size requirements, as well as for branding purposes. Printing on woven bags not only serves as a marketing tool but also provides essential product information, such as handling instructions, safety warnings, and material specifications.
How to Choose the Right Woven Bag for Your Chemical Products
When choosing between Heavy Duty Woven Bags, Ton Woven Bags, or Jumbo Bags, consider the following steps:
- Weight and Load Requirements: Ensure that the selected bag can safely handle the weight of the product. For large volumes, Jumbo Bags or FIBC Bags are ideal.
- Chemical Compatibility: Check that the woven bag is compatible with the type of chemicals you are packing. Some chemicals require specific liners or multi-wall construction.
- Regulatory Compliance: Ensure that the bags meet regional and international standards for packaging chemical products.
- Durability and Strength: Choose bags that have been tested for strength, particularly for heavy and abrasive materials. Bags that meet ASTM, JIS, and EU standards are a good starting point.
- Moisture Protection: If your chemical products are susceptible to moisture, ensure the bags feature an additional moisture-resistant layer.
- Customization: For larger operations, customized bags with your company logo or product details can enhance branding and provide clear handling instructions.
Conclusion
Selecting the right Heavy Duty Woven Bags, Ton Woven Bags, or Jumbo Bags for chemical products involves considering product characteristics, durability, regulatory standards, and moisture resistance. Adhering to the appropriate standards ensures that your chemical products are safely and efficiently transported while maintaining product integrity. By choosing the right packaging solution, you can protect your chemicals and optimize your supply chain efficiency.
For more information on packaging solutions, explore more about Heavy Duty Woven Bags, Ton Woven Bags, and Jumbo Bags for your industrial needs.