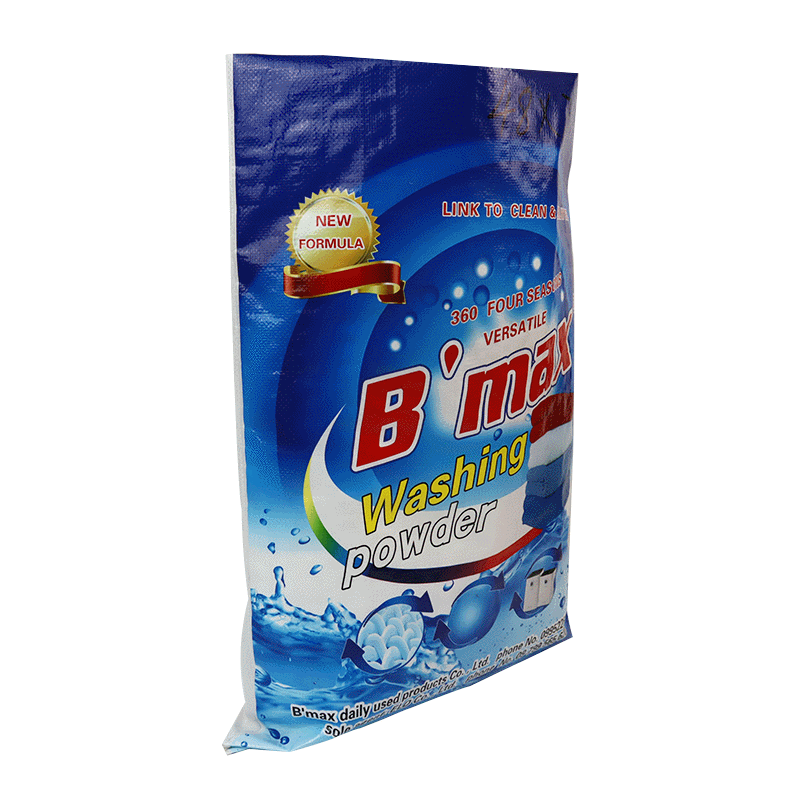
When it comes to industrial woven packaging bags, their role in safeguarding products during transportation and storage cannot be overstated. Used across various industries, from agriculture to construction, industrial packaging sacks are essential for bulk material handling. The quality, durability, and efficiency of these industrial PP bags depend significantly on the manufacturing processes used to create them, including bag design, sewing techniques, and material choices. In this article, we will discuss the factors that should guide the selection of the appropriate sewing and bag-making techniques for industrial woven bags.
What Are Industrial Woven Bags?
Woven bags are versatile, durable packaging solutions made from woven polypropylene (PP) fabric. They are widely used in industries like agriculture, chemicals, and construction due to their ability to withstand harsh conditions and heavy loads. These bags can hold a variety of materials, from grains and fertilizers to bulk chemicals and cement.
One of the key aspects of these bags is the production process. Industrial woven packaging bags come in several variations, each suited for different purposes, such as PP woven sacks, valve bags, or open mouth bags. Each design and manufacturing technique offers specific benefits, such as ease of loading, high load capacity, and protection against environmental factors like moisture.
To fully understand the process and make the right choice, manufacturers need to focus on various aspects such as sewing techniques, sealing methods, and the materials used.
Key Manufacturing Techniques for Woven Bags
1. Sewing Techniques and Thread Selection
The choice of sewing method and thread material can affect the strength, durability, and functionality of the final product. Here’s a breakdown of the most common options:
Bottom Sewing
Bottom sewing involves stitching the base of the bag after it has been filled. The strength of the seam here is crucial, as this area bears much of the weight and pressure when the bag is filled with heavy materials. The most common thread material used for this purpose is polyester or nylon due to their resistance to abrasion and UV degradation. The sewing density (i.e., the number of stitches per inch) also affects the strength of the seam. A higher stitch density provides a stronger seal, which is particularly important for bags that will carry heavy or sharp-edged materials.
Edge Sewing
Edge sewing is used for securing the bag’s sides. The goal is to ensure that the edges do not unravel and that the bag holds its shape. In this case, polypropylene (PP) thread is typically used for cost-effectiveness and to ensure the bag’s resistance to breaking under stress.
Cross-seam Sewing
For bags subjected to frequent handling and stacking, cross-seam sewing can improve durability. This technique reinforces the sides and base of the bag, preventing it from tearing when moved or stacked.
Sewing Type | Common Thread Material | Common Applications | Stitch Density |
---|---|---|---|
Bottom Sewing | Polyester/Nylon | Heavy-duty bags, chemical packaging | High density |
Edge Sewing | PP Thread | Lightweight packaging | Medium density |
Cross-seam Sewing | PP or Polyester | Agricultural and construction packaging | High density |
2. Sealing Methods: Heat Seal vs. Ultrasonic Welding
In addition to sewing, heat sealing and ultrasonic welding are common methods used to secure the edges of woven bags, especially for bags that need to be moisture-resistant.
Heat Sealing
Heat sealing is the process of using heat to fuse the edges of the fabric together. This technique is commonly used for bags that require a strong and durable closure. The benefit of heat sealing is that it can be applied quickly and uniformly, making it ideal for mass production. It also creates a waterproof barrier, preventing moisture from entering the bag, which is important when packaging food products or chemicals.
Ultrasonic Welding
Ultrasonic welding is a newer method that uses high-frequency ultrasonic vibrations to create frictional heat at the interface of two materials, which then bond together. This technique is more energy-efficient than heat sealing and results in stronger, cleaner seals. It is particularly useful for industrial PP bags that require precise, clean seals to prevent material leakage. Ultrasonic welding is also used to produce bags with a stronger seam that can withstand extreme conditions, such as high temperature or rough handling.
3. Choosing the Right Bag Mouth Design
The choice of bag mouth design significantly impacts the ease of filling and sealing. Each type of bag mouth comes with its own set of advantages:
Open Mouth Bags
Open mouth bags are the most common type of woven bags and feature an unsealed top, allowing for easy filling. Once filled, the top is typically sealed using stitching or heat sealing. These bags are ideal for products that need to be loaded manually or via conveyor systems. Open mouth bags are commonly used in the agricultural and food industries.
Valve Bags
Valve bags are designed for automatic filling systems, and they feature a built-in valve that can be sealed after filling. This makes them perfect for high-volume production where automated filling is necessary. The valve mouth ensures a quick and efficient sealing process, reducing labor costs and speeding up production.
Heat Sealed Bags
Heat-sealed bags are designed to close the top of the bag securely after filling. The heat-sealing process is preferred for products that need airtight or watertight protection. For example, BOPP woven bags often use this technique, as it offers a secure seal that maintains the integrity of the contents.
Mouth Design | Key Benefits | Common Applications |
---|---|---|
Open Mouth | Easy to fill, low cost | Agriculture, bulk food packaging |
Valve Mouth | Quick, automated sealing | Chemicals, cement, fertilizers |
Heat Sealed | Airtight, watertight | Food packaging, pharmaceuticals |
4. Material Considerations for Woven Bags
Choosing the right material is essential for ensuring that the bag performs optimally for its intended use. PP woven sacks are made from polypropylene, a durable and lightweight material. Other materials such as BOPP film are often laminated onto woven PP bags to provide added strength and protection from UV rays and moisture.
The thickness of the fabric, as well as any additional layers or coatings, will also influence the bag’s performance. For example, laminated woven bags offer enhanced barrier properties, such as resistance to moisture and dust, making them ideal for storing and transporting powders or grains.
Choosing the Right Manufacturing Technique
The final decision on the manufacturing process depends on the type of materials to be packed, the handling conditions, and the requirements of the end user. For heavy-duty applications, industrial woven packaging sacks need to be durable enough to withstand wear and tear from transportation and storage. On the other hand, more specialized bags, such as those used in food packaging, may require airtight sealing and specific hygiene standards.
Ultimately, the choice of the right technique involves a balance of cost, durability, and efficiency.
For instance, industrial woven bags used in agriculture may need to resist UV degradation and allow for moisture management. Therefore, heat sealing or ultrasonic welding may be ideal for bags used in those conditions.
For bulk chemicals or heavy construction materials, valve bags or open-mouth bags with cross-seam sewing can offer durability and ease of use, while minimizing product leakage.
Industrial Packaging Bags play a critical role in many industries, providing an effective solution for packaging, storage, and transportation. When choosing the right manufacturing process, consider the specific needs of the bag and the type of materials you will be handling.
For a deeper understanding of industrial PP bags, it is essential to evaluate the different types of seals, threads, and bag designs to ensure optimal protection and efficiency for your products.