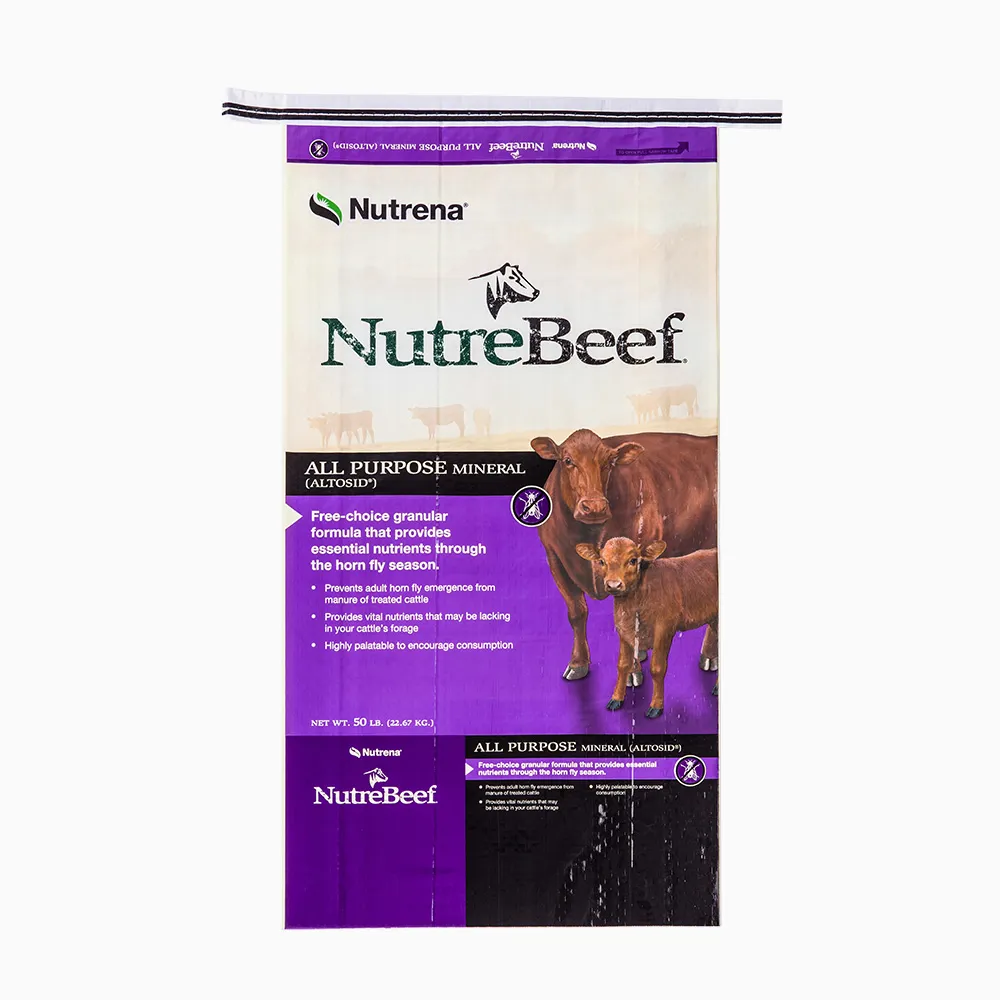
In the world of packaging, efficiency, durability, and cost-effectiveness are paramount. As the demand for high-quality packaging materials increases, the industry has witnessed innovations such as Aluminum Foil Composite Bags and Composite Woven Bags. Both products offer specific advantages, and their use cases vary depending on the requirements of the product being packaged. In addition to these packaging materials, advancements in machinery and packaging processes have also revolutionized the way goods are packaged, loaded, and transported. One such advancement is the use of a 200-ton packing machine that enables the efficient and safe transportation of goods.
In this article, we will explore the key differences between Aluminum Foil Woven Bags and Composite Woven Sacks, highlighting the strengths of each. Additionally, we will discuss the benefits of utilizing a modern 200-ton packing machine in combination with pallets and stretch film to enhance packaging efficiency and improve transportation safety.
The Key Differences: Aluminum Foil Composite Bags vs. Woven Bags
When it comes to selecting packaging materials, both Aluminum Laminated Woven Bags and traditional woven sacks have their merits. To help you decide which type of bag is right for your specific application, let’s look at the advantages of each:
1. Material Composition and Structure
Aluminum Foil Composite Bags are designed with a multi-layer structure. The outer layers are typically made of a durable woven polypropylene fabric, while the inner layers incorporate an aluminum foil laminate. This unique design makes them particularly effective at providing excellent moisture, light, and oxygen barriers, which is why they are often used in food, pharmaceutical, and chemical industries.
Composite Woven Bags, on the other hand, generally consist of woven polypropylene fabric and may or may not include additional laminations for extra strength. These bags are highly versatile, offering protection from physical damage and are well-suited for bulk packaging in a wide range of industries, from agriculture to construction.
Feature | Aluminum Foil Composite Bags | Composite Woven Bags |
---|---|---|
Material Composition | Multi-layer: Woven fabric + Aluminum Foil | Woven polypropylene fabric |
Barrier Properties | Excellent: Moisture, light, oxygen | Moderate: Primarily physical barrier |
Strength and Durability | Moderate to High | High |
Customizability | High: Colors, prints, sizes | High: Colors, prints, sizes |
Use Cases | Food, pharmaceuticals, chemicals | Agriculture, construction, retail |
Environmental Impact | Recyclable but less eco-friendly | Fully recyclable and eco-friendly |
2. Performance and Protection
The Aluminum Laminated Woven Bags stand out for their exceptional protection against external elements. The aluminum foil provides an additional layer of protection against UV light, moisture, and gases, which can be crucial for products sensitive to environmental conditions. These bags are commonly used in industries such as food packaging, pharmaceuticals, and chemicals, where preserving product integrity is essential.
Composite Woven Sacks, while also robust, are primarily used for bulk products where environmental factors are less of a concern. They offer outstanding strength, load-bearing capacity, and are resistant to tears and punctures. These bags are often the go-to choice for packaging agricultural products like grains, fertilizers, and feed, as well as construction materials like sand and cement.
3. Cost Efficiency
One major factor to consider when choosing between Aluminum Foil Woven Bags and Composite Woven Bags is cost. While Aluminum Foil Composite Bags offer superior protection, they are generally more expensive due to the use of multiple layers and advanced materials. On the other hand, Composite Woven Bags are more affordable and provide sufficient durability and strength for less sensitive products.
4. Customization and Printing
Both Aluminum Foil Woven Bags and Composite Woven Sacks are highly customizable in terms of design and branding. Custom printing on both types of bags allows companies to create visually appealing and functional packaging. The main difference here lies in the types of printing processes used, with Aluminum Foil Woven Bags often using higher-end printing techniques due to their layered structure.
Enhancing Packaging Efficiency with a 200-Ton Packing Machine
While selecting the right type of packaging is crucial, the efficiency of the packaging process also plays a significant role in reducing costs and improving logistics. One innovation that has drastically improved packaging efficiency is the 200-ton packing machine, which is capable of handling large quantities of goods in a single operation.
1. Increased Capacity
The primary advantage of using a 200-ton packing machine is its ability to significantly increase the amount of product that can be packed into a container. Traditional packing methods often involve manual labor or smaller machines, which can limit the number of products that can be efficiently packaged in a given timeframe. However, with the 200-ton packing machine, packing operations can be scaled up, allowing businesses to load more products per shipment. This is particularly beneficial for industries that ship large volumes of bulk materials, such as agriculture, construction, and chemicals.
2. Reduced Handling and Labor Costs
The 200-ton packing machine automates much of the packing process, reducing the need for manual labor and decreasing the likelihood of errors. This efficiency helps cut down on handling and labor costs, allowing businesses to allocate resources more effectively. By streamlining the packaging process, companies can focus on other areas of their operations, such as production and customer service.
3. Enhanced Safety and Protection during Transport
The use of a 200-ton packing machine is further complemented by the use of pallets and stretch film to secure the packaged goods. Pallets help distribute the weight of the goods evenly and prevent shifting during transportation. Additionally, stretch film is used to wrap the load, providing a protective layer that shields the goods from external elements such as moisture, dust, and physical damage. This packaging method ensures that the goods remain intact and in optimal condition until they reach their destination.
4. Environmental Benefits
In addition to efficiency and cost-saving benefits, the use of stretch film and pallets also offers environmental advantages. The use of stretch film minimizes the need for excessive outer packaging, helping to reduce waste. Pallets are reusable, further contributing to sustainability efforts. These measures align with the growing trend of eco-friendly packaging solutions that aim to reduce the carbon footprint of the logistics industry.
Conclusion
Choosing between Aluminum Foil Composite Bags and Composite Woven Bags ultimately depends on the specific needs of your product. While Aluminum Foil Woven Bags offer superior protection against external factors such as moisture and light, Composite Woven Sacks provide a cost-effective solution for bulk packaging, offering excellent strength and durability.
In addition to selecting the right packaging material, investing in modern technology, such as the 200-ton packing machine, can significantly improve packaging efficiency. By combining the benefits of high-quality packaging materials with advanced machinery and processes, businesses can optimize their logistics, reduce costs, and ensure the safe transportation of goods.
For more information on Composite Woven Bags, you can explore this detailed guide. If you’re interested in learning more about Aluminum Foil Woven Bags, check out this article here.