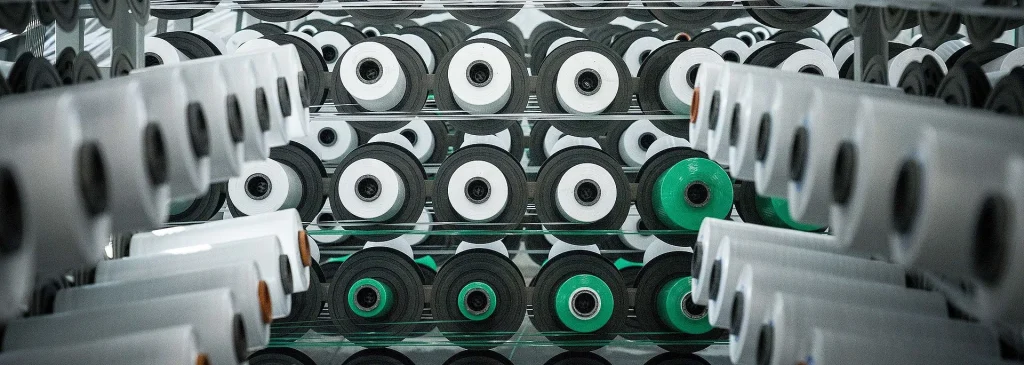
Imagine a conversation between a feed mill operator and a packaging engineer:
Operator: “We need bags that can handle 50 kg of poultry feed without tearing, resist mold in humid climates, and comply with EU safety standards. What’s your recommendation?”
Engineer: “PP woven fabric bags with BOPP lamination and anti-microbial additives are the optimal choice—they offer tensile strengths up to 50 N/cm² and reduce moisture ingress by 95%, meeting ISO 22000 food safety certifications. For example, VidePak’s 120 g/m² laminated bags prevent fungal growth even at 85% humidity, ideal for Southeast Asian markets.”
Operator: “How do we balance cost and durability for bulk cattle feed shipments?”
Engineer: “VidePak’s 100+ Starlinger circular looms produce 160 threads/inch fabric with ±0.1 mm precision, enabling cost-effective 140 g/m² bags that withstand 1.5-ton stack loads. Let’s explore why PP woven bags dominate modern feed packaging.”
1. Why PP Woven Bags Excel in Animal Feed Packaging
Polypropylene (PP) woven bags have become the global standard for animal feed packaging due to their unmatched combination of strength, breathability, and cost efficiency. With a market share of 68% in agricultural packaging , their advantages include:
- Tensile Strength: 35–50 N/cm², surpassing paper (5–8 N/cm²) and jute (10–15 N/cm²) .
- Moisture Control: BOPP lamination reduces water vapor transmission rates (WVTR) to <5 g/m²/24h, critical for hygroscopic feeds like soybean meal .
- Anti-Microbial Properties: UV-stabilized PP with silver-ion additives inhibits Aspergillus flavus growth by 99%, complying with FDA 21 CFR for feed safety .
VidePak’s Austrian Starlinger looms weave filaments at 1.8–2.3 mm widths, achieving ISO 9001-certified uniformity. This ensures consistent pore sizes (0.5–1.2 µm) for optimal airflow—reducing feed spoilage by 30% compared to non-woven alternatives .
2. Tailored Solutions for Different Feed Types
A. Poultry Feed
- Challenges: High-fat content (5–8%) risks oxidation; fine particles (<2 mm) demand dust-proof seals.
- Solution:
- BOPP Laminated Bags: 80 µm coating blocks oxygen transmission (<200 cc/m²/day) to extend shelf life .
- Valve Design: Pneumatic filling ports minimize dust leakage, complying with EU Directive 2002/72/EC.
B. Ruminant Feed (Cattle/Sheep)
- Challenges: Heavy pellets (25–50 kg/bag) require stacking strength.
- Solution:
- 140 g/m² Fabric: Withstands 6-layer palletizing (1.5 tons) without seam failure .
- PE Liners: Prevent nutrient loss during maritime transport (tested per ASTM D5276).
C. Aquatic Feed
- Challenges: High humidity (≥80%) accelerates mold growth.
- Solution:
- Anti-Fungal Additives: Zinc oxide nanoparticles inhibit Penicillium spores .
- Kraft Paper Lamination: Enhances tear resistance in saltwater environments .
3. Key Parameters for Optimal Selection
Parameter | Pet Feed | Poultry Feed | Ruminant Feed |
---|---|---|---|
Fabric Weight | 90–100 g/m² | 110–120 g/m² | 130–140 g/m² |
Lamination | Matte BOPP (30 µm) | Glossy BOPP (50 µm) | PE Coating (80 µm) |
Additives | UV inhibitors | Anti-static agents | Anti-microbial agents |
Seam Type | Heat-sealed | Sewn + Adhesive | Double-stitched |
Case Study: A Brazilian poultry producer reduced feed spoilage by 22% using VidePak’s anti-static valve bags, eliminating dust explosions during pneumatic filling (IEC 61340-4-4 certified) .
4. VidePak’s Technological Edge
With 16 extrusion lines and 30 lamination machines, VidePak delivers:
- Customization: 12 Pantone colors, QR code integration for traceability.
- Scalability: 5,000 bags/hour production, supporting JIT global delivery.
- Sustainability: 20% recycled PP content in eco-lines, reducing carbon footprint by 15% .
Explore our BOPP laminated woven bags for moisture-sensitive feeds or FIBC bulk bags for industrial-scale logistics.
5. FAQs: Addressing Procurement Concerns
Q1: How does fabric weight impact cost and durability?
A: 90 g/m² bags save 18% on material costs for pet feeds, while 140 g/m² variants offer 2x puncture resistance for abrasive cattle pellets .
Q2: Are laminated bags recyclable?
A: Yes. Our mono-material PE/PP laminates achieve 85% recyclability, aligning with EU Circular Economy Action Plan 2030 .
Q3: Can bags withstand -20°C storage?
A: Absolutely. Copolymer PP blends retain flexibility at -30°C (ASTM D746 tested) .
6. Future Trends: Smart Packaging Integration
- IoT Sensors: RFID tags monitor real-time temperature/humidity during transit .
- Biodegradable Films: PLA-PP hybrids decompose in 180 days (ASTM D6400) .
VidePak’s R&D team is piloting self-healing liners that seal <3 mm punctures automatically, ideal for long-haul aquatic feed shipments.
References
- VidePak Company Profile: https://www.pp-wovenbags.com/
- ASTM International. (2025). Standard Specification for Polypropylene Films.
- EU Directive 2002/72/EC on Food Contact Materials.
- Contact: info@pp-wovenbags.com
Anchor Links
This guide combines material science, regulatory insights, and VidePak’s 30+ years of expertise to empower your feed packaging strategy with reliability and innovation.