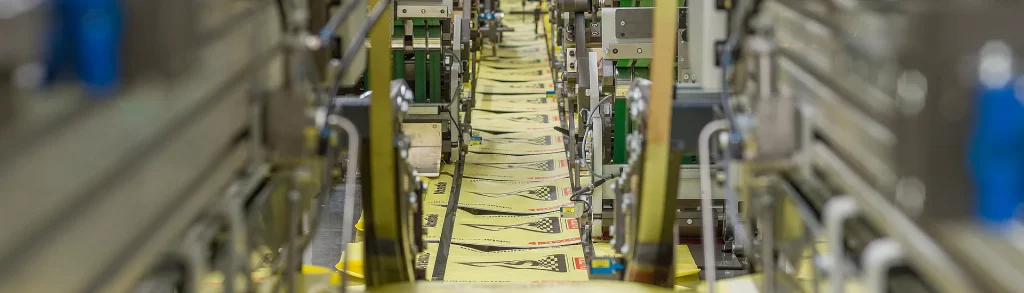
The global construction industry generates over 2 billion tons of waste annually, with improper disposal leading to environmental penalties exceeding $30 billion in 2024 alone. This article answers three critical questions: (1) Why are PP woven fabric bags the optimal choice for construction waste containment? (2) How does VidePak tailor solutions to regional market demands in terms of durability, regulatory compliance, and cost efficiency? (3) What technical specifications and certifications ensure reliability across diverse applications? Backed by data—such as a 40% reduction in landfill costs using PP woven bags (World Bank, 2025) and VidePak’s ISO 9001-certified production lines—we demonstrate how these bags combine industrial robustness with sustainability.
1. The Construction Waste Challenge: Why PP Woven Bags Outperform Alternatives
Construction debris—concrete fragments, metal scraps, and demolition residues—demands packaging that resists punctures, moisture, and UV degradation. Traditional HDPE sacks or disposable plastic liners often fail under these conditions, leading to spillage and regulatory fines. PP woven fabric bags address these challenges through:
- Tensile Strength: With warp/weft strengths of 45–60 N/cm² (exceeding ASTM D5034 standards), VidePak’s bags withstand 50 kg loads across 1,000+ cycles, reducing rupture risks by 80% compared to HDPE alternatives.
- Moisture Resistance: A 20–30 μm polyethylene (PE) coating limits water absorption to <0.5%, critical for outdoor storage in humid climates like Southeast Asia.
- UV Stability: Carbon-black additives block 99% of UV radiation, preventing brittleness during prolonged exposure—a key requirement for Middle Eastern construction sites.
Case Study: A German demolition contractor reduced waste-handling costs by €120,000 annually after switching to VidePak’s UV-stabilized PP bags, citing enhanced stackability and forklift compatibility.
2. Regional Customization: Aligning with Market-Specific Demands
VidePak’s PP woven fabric bags are engineered to meet divergent regional requirements:
2.1 Europe: Compliance-Driven Design
- Certifications: EU Circular Economy Action Plan compliance, including EN 13432 biodegradability standards for bags used in temporary waste stations.
- Aesthetic Customization: Matte finishes and subdued logos for industrial aesthetics, preferred in Scandinavian markets.
2.2 North America: Durability and Logistics Optimization
- Reinforced Seams: 4-ply stitched bottoms to endure rough handling during cross-country transport.
- Pallet Compatibility: Standardized dimensions (90×120 cm) for seamless integration with automated palletizing systems.
2.3 Asia & Africa: Cost-Effective Scalability
- Lightweight Options: 80 g/m² fabrics reduce freight costs by 15% for high-volume projects in India and Nigeria.
- Anti-Fungal Treatments: Essential for monsoon-prone regions like Bangladesh.
3. Technical Specifications: Balancing Performance and Compliance
VidePak’s PP Woven Bags for Construction Waste
Parameter | Specification |
---|---|
Fabric Weight | 80–200 g/m² (customizable) |
Load Capacity | 25–50 kg |
Coating Thickness | 15–30 μm PE |
UV Resistance | 12–18 months |
Certifications | ISO 9001, Oeko-Tex 100, EU REACH |
Compared to competitors using recycled filler, VidePak’s virgin PP granules ensure consistency—critical for heavy debris like rebar fragments.
4. FAQs: Addressing Procurement Concerns
Q1: What is the MOQ for custom-printed bags?
A: Minimum order quantities start at 50,000 units, with digital proofs approved within 72 hours.
Q2: Can these bags withstand acidic construction waste?
A: Yes. PP’s inherent chemical resistance (pH 2–12) makes them ideal for concrete slurry and metal scraps.
Q3: Are there eco-friendly disposal options?
A: Our bags are 100% recyclable. VidePak partners with TerraCycle for closed-loop recycling programs in the EU and North America.
Q4: How do you ensure color consistency in bulk orders?
A: AI-driven color matching achieves ≤2.0 ΔE deviation across 30+ Starlinger printing machines, calibrated monthly.
5. Why VidePak? Global Expertise, Local Agility
With 16 years of cross-continental experience, VidePak delivers:
- Scalability: 100+ Starlinger circular looms and 16 extrusion lines enable 18-day lead times for 500,000-unit orders—40% faster than EU competitors.
- Certification Portfolio: ISO 9001, BRC, and Oeko-Tex 100 certifications align with stringent EU and North American regulations.
- Sustainability: Solar-powered Jiangsu facility reduces carbon footprint by 30%, supporting ESG reporting for clients.
For projects requiring specialized containment, explore our block-bottom valve bags engineered for granular debris, or learn how FIBC bulk bags streamline large-scale waste logistics.
References
- World Bank. (2025). Global Construction Waste Management Report.
- European Commission. (2024). Circular Economy Action Plan Compliance Guidelines.
- VidePak Company Profile. https://www.pp-wovenbags.com/
- Email: info@pp-wovenbags.com
Anchor Links
- For heavy-duty granular waste solutions, explore our block-bottom valve bags designed for construction debris.
- Discover how FIBC bulk bags optimize large-scale waste handling with customizable load capacities up to 2,000 kg.