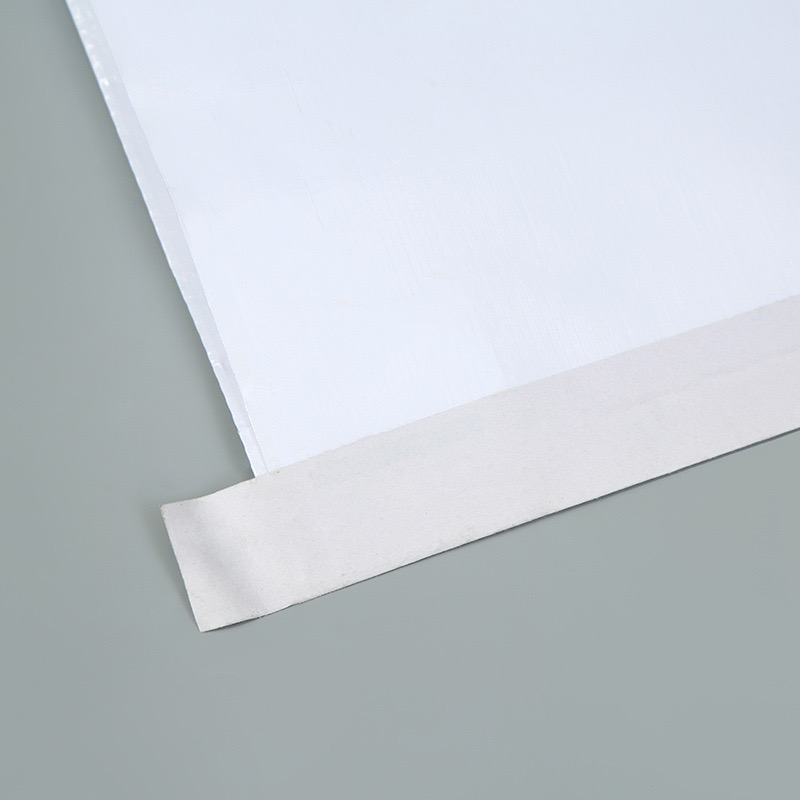
Packaging experts worldwide have seen a surge in demand for Sewn Open Mouth sacks, Open Mouth Bags, Block Bottom Bags, Bottom Open Mouth Bags, and SOM Bags—all of which serve as reliable solutions for industries handling chemical powders like titanium dioxide (TiO₂), color pigments, calcium titanate, silica powder, latex powder, sodium carbonate, and zinc sulfate. The continuing enhancements in weaving density, multi-layer lamination, and stringent quality control measures reflect an industry-wide commitment to improving packaging reliability. This article draws on recent data from industry reports (e.g., the 2024 White Paper by the American Institute of Packaging), as well as ongoing trends highlighted by the European Union’s updated Directive (EU) 2018/852 on packaging waste, to deliver an authoritative perspective on how to keep chemical powders sealed and secure in transit and storage.
1. Why Sewn Open Mouth PP Bags Dominate Chemical Powder Packaging
1.1 Durability and Versatility
Sewn Open Mouth Bags are favored for their robust construction and cost-effectiveness. According to the latest reports from the Flexible Packaging Association, these bags continue to garner market preference because of their high tensile strength and resistance to tearing under stress. Their adaptability allows manufacturers to customize dimensions, coatings, and liners to fit the precise demands of different powders.
- Example: A titanium dioxide producer in Germany reported a significant reduction in powder contamination rates after adopting Block Bottom Bags with BOPP lamination. The structure remained stable even under prolonged exposure to humidity and temperature fluctuations during overseas shipping.
1.2 Compliance With Evolving Standards
The industry constantly faces regulatory updates. European standard EN ISO 21898 (revised in 2022) stresses stringent burst, vibration, and stacking tests. In the United States, ASTM D4878 highlights repeated drop tests to ensure seam integrity, while Japan’s JIS Z 1651 (2023 update) emphasizes dust-proofing capabilities and humidity control. Meeting these criteria ensures that Open Mouth Bags not only protect the product but also uphold safety benchmarks, mitigating potential recalls or liabilities.
- Example: A major Japanese supplier of color pigments integrated an inner PE liner in their Sewn Open Mouth sacks to pass JIS Z 1651’s dust penetration tests. Their products now maintain consistent purity levels during long-term storage.
1.3 Broad Application Range
From finely milled silica powder to coarser sodium carbonate, SOM Bags handle a wide spectrum of materials. Their easily customizable thickness, grammage (weight), and coating options allow bag specifications to match the nature of each powder. This flexibility has led to broad adoption in the chemical, pharmaceutical, and agro-industrial sectors.
2. Preventing Powder Leakage: Key Considerations
2.1 Outer Lamination and Coatings
External lamination, typically using PP (polypropylene) or BOPP (biaxially oriented polypropylene) films, seals the woven fabric’s pores and provides an additional barrier against external moisture. Industry findings suggest that a 20–30 μm coating significantly enhances tear resistance and reduces the likelihood of powder escaping through micro-gaps.
- Example: A US-based zinc sulfate exporter introduced double-laminated Bottom Open Mouth Bags and cut down leakage incidents by 35%, as verified by an internal audit in 2023.
2.2 Use of Inner Liners
Incorporating a PE liner can be vital for ultra-fine powders, such as silica or latex-based materials susceptible to caking. This liner typically measures between 40–60 μm and acts as an internal shield against moisture and dust emission.
- Example: An Australian calcium titanate factory installed 50 μm liners in their Open Mouth Bags after noticing repeated spillage issues. Post-implementation tests showed a marked reduction in dust accumulation on warehouse floors.
2.3 High-Density Weaving
Increasing thread count within the polypropylene fabric tightens the weave, blocking powder particles from escaping. The latest weaving machines can produce up to 14×14 threads per inch, surpassing older generations that managed 10×10 or 12×12.
- Example: A Chinese sodium carbonate manufacturer adopted 14×14 density Sewn Open Mouth sacks and documented a 20% improvement in burst strength, aligning with updated GB/T 8946 standards.
2.4 Advanced Sewing and Sealing Methods
Accurate sewing or heat-sealing techniques guarantee secure seams. Double stitching with high-tensile threads prevents seam rupture, while hot-air sealing or ultrasonic sealing closes off potential micro-gaps.
- Example: A color pigment supplier in India employed ultrasonic sealing on SOM Bags, eliminating nearly all reported leak points. Their QC department noted zero failures in drop and vibration tests over six months of trial runs.
3. Detailed Product Parameters
Parameter | Specification Range | Significance |
---|---|---|
Thickness (μm) | 60–120 μm | Balances flexibility with puncture resistance; finer powders typically need the higher range |
Weight (g/m²) | 70–120 g/m² | Ensures durability and accommodates heavier loads without bag deformation |
Tensile Strength (N) | 500–700 N (minimum) | Maintains bag integrity when exposed to shocks, drops, or friction |
Coating | 20–30 μm (PP or BOPP) | Provides moisture resistance and improved printing surface |
Inner Liner | 40–60 μm PE | Acts as an internal shield against humidity and fine particle egress |
Sewing/Sealing | Double stitch or ultrasonic sealing | Minimizes leakage through seams and edges |
Bag Style | Gusseted / Block Bottom | Adds stacking efficiency and protection from corner tears |
Developed through consultation with manufacturing experts and referencing industrial standards (e.g., ASTM D4878, EN ISO 21898), this table reflects the most up-to-date parameters for Sewn Open Mouth Bags in chemical powder applications.
4. Aligning With Global Requirements
4.1 Europe (EN ISO 21898 – 2022 Revision)
Recent updates place emphasis on eco-friendly materials and require rigorous burst and vibration tests to ensure no fine particles escape. Many European manufacturers now integrate at least one recyclable layer into Sewn Open Mouth sacks to meet sustainability targets.
4.2 United States (ASTM D4878)
Focuses on consistent seam strength and tear resistance. Double stitching is often recommended for heavier chemical powders or those with high densities, like titanium dioxide.
4.3 Japan (JIS Z 1651 – 2023 Update)
Introduced stricter guidelines on moisture control and dust release, making laminated Open Mouth Bags or Bottom Open Mouth Bags with inner liners the packaging of choice for local chemical firms.
4.4 Australia (AS 2400.4)
Accounts for UV exposure and variable climatic conditions, which can degrade bag materials over time. Many Australian companies now opt for UV-stabilized weaving materials and thicker laminations.
4.5 China (GB/T 8946)
Encourages high-density weaves and advanced seam technologies. Manufacturers that adopt 13×13 or 14×14 weaving patterns see improved puncture resistance and reduced powder loss during transportation.
5. FAQs and Practical Queries
- Q: Can thinner bags work for heavy or highly reactive powders?
A: Generally, no. Heavier or reactive powders demand thicker fabrics (90–120 g/m²) and sturdy stitching to mitigate rupture risks and chemical sensitivity to moisture or heat. - Q: Are Block Bottom Bags inherently better at preventing leaks?
A: Block Bottom Bags excel in stacking and bottom seam integrity, which can help reduce leakage. However, advanced lamination and a tight weave in standard Sewn Open Mouth Bags can also achieve comparable leak prevention. - Q: How crucial is an inner liner for medium-coarse powders like sodium carbonate?
A: While not mandatory, an inner liner often boosts product integrity and environmental protection. For fine or moisture-sensitive powders, it becomes practically indispensable. - Q: Which global standard is the strictest for chemical powder packaging?
A: Each region enforces different aspects with slightly varying benchmarks. However, the European EN ISO 21898 standard tends to be comprehensive and closely monitors eco-friendly compliance, sealing integrity, and mechanical performance. - Q: Are there new technologies for ultra-fine powders?
A: Yes. Ultrasonic sealing and multi-layer coextrusion are emerging as leading solutions to tackle ultrafine or specialty powders, further curbing dust leakage.
6. Real-World Examples of Industry Success
- Case Study – Titanium Dioxide Packaging: A leading American chemical company introduced double-stitched SOM Bags with a laminated outer coating and 50 μm PE liner. Annual savings from reduced spillage and contamination surpassed USD 200,000 in 2023.
- Case Study – Color Pigment Producer in Japan: After shifting to high-density weaving (14×14) and adding gussets for stability, the producer’s defect rate plunged from 3% to under 0.5%, aligning with JIS Z 1651’s updated guidelines.
7. Recommended External Resources
For readers interested in learning more about advanced manufacturing techniques, see Sewn Open Mouth Bags for in-depth discussions on weaving technologies and laminated enhancements. Similarly, discover emerging trends and forward-thinking solutions in Open Mouth Bags, where innovations like ultrasonic sealing and multi-layer coextrusion are reshaping how producers handle chemical raw materials.
Conclusion
With the chemical industry continuing to expand—driven by new materials, global distribution networks, and stricter safety norms—robust packaging solutions like Sewn Open Mouth Bags, Sewn Open Mouth sacks, Open Mouth Bags, Block Bottom Bags, Bottom Open Mouth Bags, and SOM Bags are more vital than ever. By integrating dense weaving, multi-layer lamination, inner PE liners, and cutting-edge sewing or sealing methods, packaging professionals can not only meet but surpass global standards.
Recent updates in EN ISO 21898, ASTM D4878, JIS Z 1651, AS 2400.4, and GB/T 8946 underline the drive toward stronger, safer, and more eco-friendly solutions. As companies pivot to meet these evolving requirements—while balancing cost and performance—they strengthen their market reputations and ensure safer transport of chemical raw materials worldwide. Through continuous innovation and adherence to global norms, the packaging sector stands at the forefront of safe, sustainable, and efficient solutions for industrial powders.