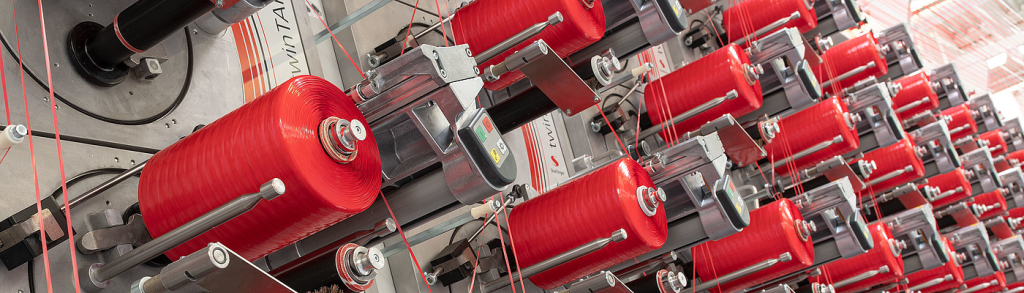
Polypropylene (PP) bags are versatile, durable, and customizable solutions widely used across industries, from agriculture to construction. As businesses look for efficient packaging solutions, polypropylene bags—whether woven or laminated—offer a comprehensive range of choices, each with unique benefits and applications. This article explores the diversity of materials used in PP bags and the production techniques behind them, providing an in-depth overview of the various types of PP bags available today.
Material Diversity in PP Bags
Polypropylene bags are primarily made from high-quality PP resin, which can be processed in various ways to create bags that meet specific requirements. The material used influences the bag’s strength, flexibility, resistance to moisture, and suitability for different environments. Below is a breakdown of common materials used in PP bag production:
Type of Material | Key Properties | Applications |
---|---|---|
BOPP (Biaxially Oriented Polypropylene) | High strength, transparency, excellent printability | Food packaging, retail packaging, agricultural products |
Kraft Paper Laminated with PP | Robust, eco-friendly, resistant to wear | Construction, fertilizers, chemicals, and bulk products |
Polypropylene Woven Fabric | Strong, breathable, and flexible | Bulk goods, construction, and agriculture |
FFS (Form-Fill-Seal) Tubular PP | High-speed production, customizable shapes | Industrial applications, food packaging |
Jumbo Woven Bags | Large capacity, durable, moisture-resistant | Bulk material transport, agriculture, and industrial products |
Valve Bags | Tight seal, easy filling | Agricultural feed, chemicals, and construction |
Each type of PP bag material is chosen based on the packaging requirements, including strength, barrier properties, moisture resistance, and the ability to handle specific loads. For instance, BOPP bags are perfect for retail packaging due to their visual appeal and printability, while Kraft Paper Laminated PP bags provide added durability and eco-friendliness for industrial use.
Production Techniques: The Art of Creating Strong, Durable, and Customizable PP Bags
The manufacturing process of PP bags involves several stages, each of which impacts the final product’s performance, durability, and cost. Let’s dive into the common production techniques:
1. Woven Fabric PP Bags
Woven PP bags are produced by weaving polypropylene fibers into a sturdy fabric that offers high tensile strength and flexibility. These bags are used in a range of applications, from carrying agricultural products to storing chemicals.
The key production stages include:
- Extrusion: Polypropylene pellets are melted and extruded into thin fibers.
- Weaving: The fibers are woven together using specialized looms to form a fabric.
- Lamination (optional): In some cases, woven fabric is laminated with other materials such as BOPP film for added durability and barrier properties.
2. BOPP Laminated PP Bags
The production of BOPP laminated PP bags involves several advanced processes:
- Extrusion of PP Film: First, the polypropylene resin is extruded to create a flat film.
- Biaxial Orientation: The film is stretched in both directions (horizontal and vertical) to improve strength and transparency.
- Lamination: The BOPP film is then laminated to woven PP fabric to improve the bag’s surface, making it printable for branding and design purposes.
3. FFS (Form-Fill-Seal) Tubular PP Bags
FFS bags are manufactured through a continuous process that allows for high-speed production. The steps include:
- Film Extrusion: PP resin is melted and formed into a tubular film.
- Forming: The film is shaped into a tubular form that will become the bag.
- Filling and Sealing: The bags are filled with the product and sealed automatically.
These bags are ideal for mass production and are commonly used in food packaging due to their speed and flexibility.
4. Jumbo Woven PP Bags
Jumbo bags are large capacity bags typically used for bulk material handling. Their production process includes:
- Weaving of Strong Polypropylene Fabric: Similar to woven PP bags but with thicker and stronger fibers to handle large volumes.
- Seam Welding or Sewing: The edges of the fabric are welded or sewn to create a sturdy, load-bearing bag.
Key Advantages of PP Bags
PP bags offer numerous benefits, making them an ideal choice for packaging in many industries:
- Durability: PP bags are known for their robustness and ability to withstand rough handling.
- Customization: Whether it’s size, color, or printing, PP bags can be tailored to meet specific requirements.
- Cost-Effective: They provide a low-cost, efficient solution for bulk packaging.
- Eco-Friendly Options: With increasing consumer demand for sustainable practices, Kraft Paper Laminated PP Bags are gaining popularity as an eco-friendly solution for industries seeking environmentally responsible alternatives.
FAQs About PP Bags
1. What are the differences between BOPP and Kraft Paper Laminated PP Bags?
BOPP bags are highly transparent and offer excellent printability, making them suitable for retail packaging. Kraft paper laminated PP bags are stronger, more durable, and provide additional protection against moisture and wear, making them ideal for industrial and bulk packaging.
2. How can PP bags be customized?
PP bags can be customized in a variety of ways:
- Size: Bags can be made to fit specific quantities or dimensions.
- Printing: Full-color printing allows for branding and design.
- Additives: For specific needs, such as UV resistance, anti-static properties, or moisture resistance, additives can be incorporated into the production process.
3. Are PP bags recyclable?
Yes, polypropylene bags are recyclable. However, their recycling process can vary depending on the bag type and location. Some PP bags, especially woven ones, can be recycled back into usable plastic materials.
4. Can PP bags be used for food packaging?
Yes, many types of PP bags, such as FFS Tubular Bags, are safe for food packaging. However, it is essential to ensure that the bags meet food safety standards, such as being free from harmful chemicals.
5. What industries use PP bags the most?
PP bags are used across various industries, including:
- Agriculture: For storing and transporting grains, seeds, fertilizers, and feed.
- Chemicals: For packaging powders, granules, and other chemicals.
- Retail: For consumer goods like pet food, groceries, and other packaged items.
- Construction: For transporting bulk materials such as sand, cement, and gravel.
Latest Trends in PP Bag Production
As the demand for sustainable packaging grows, the eco-friendly options within the PP bag industry are on the rise. One significant trend is the shift toward using recycled PP materials, which not only reduces waste but also cuts down on the energy required to produce new PP resins. Another exciting development is the use of multilayer films that provide greater strength and improved moisture barriers.
In addition, custom printing technologies have evolved, offering more advanced options such as flexographic printing for high-resolution designs. As businesses look for ways to differentiate their products, the ability to print high-quality, vibrant designs on PP bags is becoming increasingly important.
Conclusion
Polypropylene bags offer a comprehensive, one-stop solution for a variety of industries, thanks to their material diversity and advanced production techniques. From the high transparency of BOPP bags to the industrial strength of Kraft Paper Laminated PP bags, businesses can choose the ideal product for their needs. With customizations available in size, strength, and design, these bags offer cost-effective, durable, and sustainable packaging solutions.
For more insights into the versatility and applications of PP bags, you can read about the role of Kraft Paper Laminated PP bags in packaging or explore the advantages of industrial woven bags in flood protection.