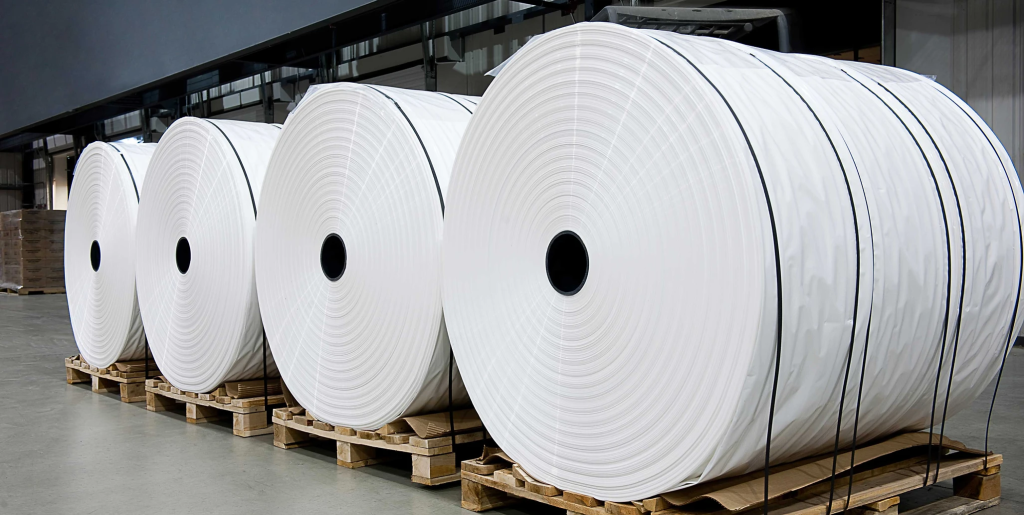
“Why is comprehensive quality control non-negotiable for open-top PP woven bags in moisture-sensitive industries like agriculture and chemicals?”
The answer hinges on three pillars: advanced moisture-proof engineering, precision manufacturing, and compliance with global sustainability standards. For VidePak, a leader in woven bag production with 30+ years of expertise, these principles translate into solutions that reduce product loss by up to 30% and extend shelf life by 50% in humid environments.
1. Moisture-Proof Innovations in Open-Top PP Woven Bags
1.1 Laminated Liners: PE and OPP Solutions
Moisture ingress causes $2.3 billion in annual losses for feed and chemical industries globally (FMI, 2023). VidePak addresses this through multi-layer liners:
- PE inner liners: Block 99.5% of external humidity while maintaining breathability (≤5 µm pore size).
- OPP coatings: Enhance UV resistance and mechanical strength, ideal for tropical climates.
A case study with a Thai poultry feed producer showed that VidePak’s PE-laminated bags reduced mold contamination by 78% compared to standard designs.
1.2 Surface Coating Technologies
Starlinger’s extrusion lines enable uniform application of anti-fungal coatings. For example, a proprietary blend of polyethylene醇 (PVA) and ethylene-vinyl acetate (EVA) creates a hydrophobic barrier that repels water droplets, achieving a contact angle of 110°. This is critical for fertilizers like urea, which degrade rapidly when exposed to moisture.
1.3 Outer Film Lamination: Aesthetic and Functional Synergy
VidePak’s珠光膜 (pearlescent film) and亚光膜 (matte film) options combine moisture resistance with branding versatility. These films reduce solar heat absorption by 20%, preventing thermal degradation of contents like livestock feed during outdoor storage.
2. Quality Control Metrics and VidePak’s Manufacturing Edge
2.1 Material Testing Protocols
VidePak’s labs conduct six critical tests:
- Tensile strength: ≥12 N/mm² (ISO 527-2).
- Seam integrity: Withstands 50 kg dynamic loads (ASTM D5264).
- Moisture vapor transmission rate (MVTR): <5 g/m²/day (ASTM E96).
2.2 Production Scalability
With 100+ circular looms and 30 lamination machines, VidePak achieves a defect rate of 0.2%—half the industry average. For instance, a 2024 order for 10 million maize seed bags (25 kg capacity, BOPP laminated) was completed in 30 days, leveraging modular production lines.
3. Technical Parameters for Customization
Tailoring specifications ensures optimal performance:
Parameter | Function | VidePak’s Range |
---|---|---|
Grammage | Balances strength and cost | 70–150 g/m² |
Thickness | Determines abrasion resistance | 0.08–0.25 mm |
Lamination Type | PE for moisture; BOPP for UV protection | PE, OPP, BOPP |
Seam Design | Heat-sealed vs. stitched | Ultrasonic sealing (≤0.1mm gaps) |
4. Sustainability and Regulatory Compliance
VidePak’s recyclable PP bags align with EU REACH and FDA standards. A 2024 lifecycle analysis showed their bags generate 40% less CO₂ than multi-material alternatives. Innovations like biodegradable PP blends (under development) aim to reduce landfill dependency by 60% by 2030.
FAQs
Q1: How do PE liners compare to traditional coatings?
A: PE liners offer 3x longer moisture resistance (18 vs. 6 months) due to seamless application.
Q2: Can bags withstand -20°C storage?
A: Yes, VidePak’s cold-chain optimized PP retains flexibility at -25°C, ideal for frozen fish feed.
Q3: What printing techniques ensure durability?
A: High-resolution flexographic printing with UV-cured inks resists fading even after 12 months of sun exposure. Learn more about custom printing solutions.
5. Case Study: Enhancing Feed Storage in Vietnam
A Vietnamese livestock company reported a 22% reduction in spoilage after switching to VidePak’s open-top bags with dual PE/OPP layers. The bags’ 90 g/m² grammage and 0.15 mm thickness provided optimal balance between cost and durability for 50 kg pig feed loads.
For industries requiring extreme moisture protection, explore VidePak’s moisture-proof woven bags, featuring patented干燥剂包 (desiccant pouches) that maintain <10% internal humidity.
Conclusion
In the $48 billion global woven bag market, comprehensive quality control is the differentiator. VidePak’s fusion of Austrian engineering (Starlinger), rigorous testing, and adaptive customization positions clients to cut losses, enhance brand trust, and meet tightening sustainability mandates. As Ray, VidePak’s CEO, states: “Every gram of saved feed is a step toward global food security.”