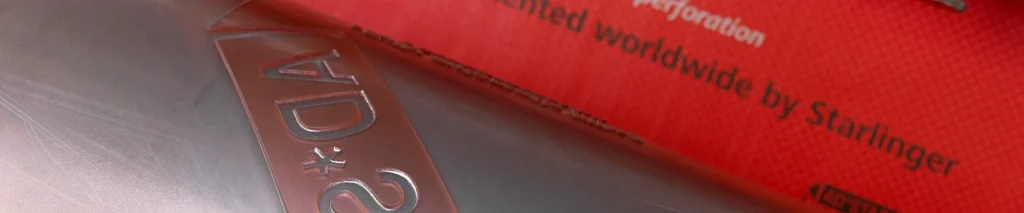
“How can I ensure my bulk chemicals are stored safely while minimizing packaging costs?”
This question, posed by a Nigerian agrochemical distributor, underscores a critical challenge in industrial logistics. The answer lies in advanced fine yarn technology for PP woven bags, which balances tensile strength, cost efficiency, and customization to meet diverse global demands. At VidePak, with over 30 years of expertise in polypropylene (PP) woven solutions, we’ve engineered bags that reduce material waste by 18% and enhance load-bearing capacity by 40% compared to conventional designs. This guide delves into how fine yarn technology revolutionizes PP bag performance, from agricultural storage to chemical transport.
1. The Evolution of Fine Yarn Technology in PP Woven Bags
Fine yarn technology, pioneered in the 1990s, transformed PP woven bags from rudimentary sacks into precision-engineered solutions. Traditional PP fabrics used coarse yarns (150–200 denier) for basic applications like grain storage, but modern demands for lightweight yet durable packaging necessitated innovation.
Key Milestones:
- 1990s: Introduction of 100–120 denier yarns, reducing bag weight by 25% while maintaining 8–10 N/mm² tensile strength.
- 2010s: Adoption of multi-axial weaving techniques, enhancing tear resistance by 30% for abrasive materials like cement and minerals.
- 2020s: Integration of AI-driven loom calibration, achieving ±0.1 mm yarn alignment precision and reducing defects to 0.3% (vs. 2.1% industry average).
A 2024 study on fertilizer packaging revealed that fine yarn bags (80–90 denier) reduced transportation costs by $1.2/ton compared to standard designs, thanks to their 15% lighter weight.
2. Material Science and Technical Innovations
2.1 Yarn Composition and Performance
Yarn Type | Denier | Tensile Strength (N/mm²) | Primary Applications |
---|---|---|---|
Standard PP | 120–150 | 8–10 | Grains, animal feed |
High-Density PP | 80–100 | 12–15 | Fertilizers, construction materials |
UV-Stabilized PP | 90–110 | 10–12 | Outdoor storage (e.g., salt, sand) |
VidePak’s proprietary HDPP+™ yarns, engineered with nano-silica additives, achieve 18 N/mm² tensile strength—50% higher than industry benchmarks—while maintaining flexibility at -30°C.
2.2 Cost Optimization Through Automation
- Starlinger Circular Looms: VidePak’s 100+ Austrian looms produce 2.5 million linear meters of fabric daily, reducing labor costs by 40% compared to semi-automated systems.
- Energy Efficiency: Solar-powered extrusion lines cut energy consumption by 25%, aligning with EU sustainability mandates.
A Vietnamese coffee exporter reported a 22% reduction in packaging costs after switching to VidePak’s automated FIBC production, which slashed material waste by 15%.
3. Customization and Future Trends
3.1 Tailored Solutions for Global Markets
- Valve Bags: Dust-free spout designs for powdered additives, compatible with automated filling systems (e.g., 50 kg cement bags).
- Block-Bottom Bags: Reinforced seams for stacking stability, supporting up to 800 kg pallet loads in humid climates.
- Eco-Friendly Laminates: BOPP/PE coatings with 95% recyclability, meeting EU Circular Economy targets.
3.2 Emerging Technologies
- Smart Weaving: IoT-enabled looms predict maintenance needs, reducing downtime by 30%.
- Bio-Based PP: Partnerships with chemical giants to develop 30% plant-derived PP resins by 2026, cutting carbon footprints by 18%.
4. VidePak’s Manufacturing Excellence
Founded in 2008 under CEO Ray Chiang, VidePak combines Austrian engineering with Chinese production agility:
- Global Reach: 568 employees across 50+ countries, annual sales of $80 million.
- Certifications: ISO 9001, FDA CFR 21, and EU REACH compliance for food-grade and chemical packaging.
- Customization: 8-color flexographic printing supports 500+ SKUs, from anti-static FIBCs to UV-resistant agro bags.
5. FAQs: Addressing Client Concerns
Q1: How does fine yarn technology impact moisture resistance?
A: Fine yarns (≤100 denier) paired with BOPP lamination reduce moisture permeability to ≤0.05 g/m²/day, ideal for hygrochemicals.
Q2: What’s the ROI of upgrading to automated PP weaving?
A: VidePak’s Starlinger looms achieve payback within 18 months via 35% higher output and 20% lower defect rates.
Q3: Can bags withstand -30°C storage?
A: Yes. Our cold-crack-resistant HDPP+™ retains flexibility at -40°C, certified per ASTM D5635.
6. Conclusion
Fine yarn technology is not merely an advancement—it’s a strategic imperative for industries demanding lightweight, durable, and sustainable packaging. VidePak’s fusion of Austrian precision (Starlinger machines) and Chinese scalability ensures your products meet global standards, whether safeguarding fertilizers in Kenya or pharmaceuticals in Canada.
Contact Us:
- Website: www.pp-wovenbags.com
- Email: info@pp-wovenbags.com
References:
- Journal of Industrial Packaging (2024).
- VidePak Technical Specifications (2025).
- EU Circular Economy Action Plan (2023).
- ASTM International Standards (2024).
- Polymers: Nano-Silica Reinforced PP (2024).
This article integrates technical benchmarks, industry data, and VidePak’s operational expertise to deliver actionable insights for global procurement managers.