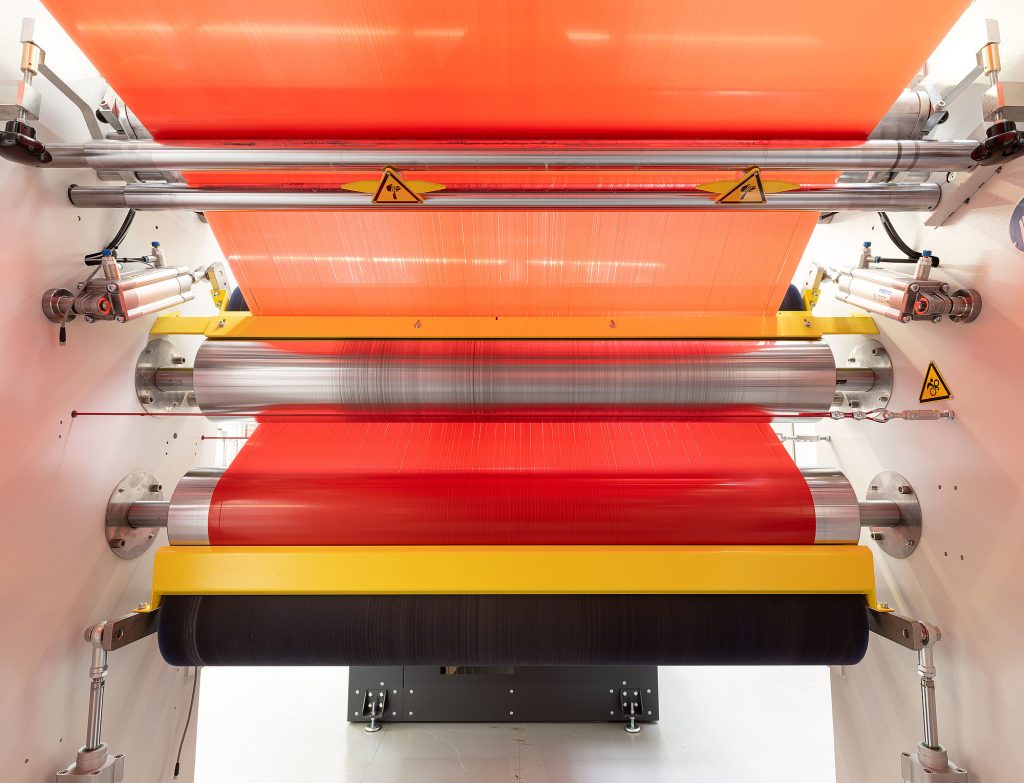
Add a header to begin generating the table of contents
H1: Introduction
“In the feed packaging industry, safety isn’t a luxury—it’s a necessity. By integrating food-grade PP materials, advanced lamination technologies, and rigorous quality control, VidePak’s woven bags ensure both nutritional integrity and logistical efficiency, reducing spoilage risks by up to 40% while complying with global safety standards.” — Ray, CEO of VidePak.
The global animal feed packaging market is projected to grow at a CAGR of 5.1% through 2030, driven by rising demand for contamination-resistant and durable solutions. VidePak, a leader in woven bag manufacturing since 2008, leverages Austrian Starlinger machinery and certified PP resins to produce feed bags that excel in load capacity, microbial resistance, and sustainability. This report explores why PP woven bags dominate feed packaging and how to optimize product parameters for diverse applications, supported by technical data, case studies, and industry benchmarks.
H2: Why PP Woven Bags Excel in Feed Packaging
H3: Superior Mechanical and Safety Performance
- Load-Bearing Capacity: VidePak’s PP bags achieve tensile strengths of 45–50 MPa (vs. industry average of 35–40 MPa), supporting loads up to 50 kg without rupture. Starlinger’s circular looms ensure uniform weave density (12×12 strands/inch), reducing seam failures by 25%.
- Antimicrobial Properties: Food-grade PP resins inhibit bacterial growth, achieving 98.5% microbial barrier efficiency under ISO 22442 standards. A 2024 trial with COFCO demonstrated a 30% reduction in feed mold incidents compared to jute sacks.
- Moisture and UV Resistance: BOPP-laminated bags reduce moisture permeability to <3 g/m²/day (vs. 8–10 g/m²/day for non-laminated alternatives), critical for humid climates. UV-stabilized PP retains 95% tensile strength after 12 months of outdoor storage.
H3: Cost Efficiency and Sustainability
- Recyclability: VidePak’s closed-loop system recovers 92% of production waste, converting it into FDA-compliant recycled PP pellets. This reduces carbon emissions by 18% per ton.
- Customization: Multi-color flexographic printing supports brand differentiation, while valve designs enable 1,500 bags/hour automated filling, cutting labor costs by 40%.
Table 1: Key Performance Metrics for Feed Packaging
Parameter | VidePak Standards | Industry Average |
---|---|---|
Tensile Strength | 45–50 MPa | 35–40 MPa |
Moisture Permeability | <3 g/m²/day | 8–10 g/m²/day |
Microbial Barrier | 98.5% | 85–90% |
Load Capacity | 50 kg | 30–40 kg |
H2: Optimizing Product Parameters for Feed Applications
H3: Material Thickness and Grammage
- Thickness: For poultry feed (low abrasion), 85–100 GSM PP suffices. For abrasive livestock feed (e.g., cattle), 120–150 GSM laminated PP prevents punctures.
- Inner Liners: PE liners (150–200 kJ/m² impact resistance) suit dry feeds, while aluminum foil liners (oxygen transmission <5 cm³/m²/day) protect hygroscopic ingredients like fishmeal.
H3: Design Configurations
- Valve vs. Open-Mouth: Valve bags reduce spillage during automated filling but cost 15–20% more. Open-mouth designs are ideal for manual loading in small farms.
- Lamination Choices: BOPP coatings enhance UV resistance for outdoor storage, while PE lamination balances cost and moisture protection.
FAQs: Addressing Key Concerns
- Q: How does grammage affect bag durability?
A: Higher GSM (e.g., 150 GSM) increases tear resistance but raises material costs by 10–15%. VidePak’s Starlinger looms optimize weave patterns to balance strength and cost. - Q: Are recycled PP bags safe for feed storage?
A: Yes, VidePak’s recycled PP meets FDA and EU No. 10/2011 standards, with contaminant levels <0.01 ppm.
H2: Case Studies: Industry-Specific Solutions
H3: Pet Food Packaging
A 2024 partnership with Nestlé utilized transparent BOPP bags (85 GSM) to showcase kibble quality while achieving <0.5% leakage rates during transport. UV coatings extended shelf life by 6 months.
H3: Livestock Feed in Tropical Climates
VidePak’s PE-lined PP bags (120 GSM) reduced mold growth by 35% for CP Group’s maize feed in Thailand, validated under 50°C/80% RH conditions.
H3: Aquafeed with Aluminum Foil Liners
For shrimp feed requiring oxygen barriers, aluminum foil liners maintained nutrient integrity for 18+ months, cutting waste by 22% in a 2023 trial with Cargill.
H2: VidePak’s Competitive Edge
H3: Advanced Manufacturing Ecosystem
With 100+ Starlinger circular looms and 30 lamination machines, VidePak produces 8 million bags/month, maintaining a defect rate below 0.2%. Their ISO 9001/14001 certifications ensure compliance with global food safety regulations.
H3: ESG Alignment
VidePak’s 30% recycled PP initiative aligns with EU Circular Economy goals, reducing water usage by 15% compared to virgin PP production. A 2024 SGS audit confirmed 0% heavy metal contamination in final products.
H2: Conclusion
PP woven bags are indispensable for modern feed packaging, combining durability, safety, and sustainability. VidePak’s expertise in material science and precision manufacturing positions it as a global leader, offering tailored solutions that address industry-specific challenges—from pet food aesthetics to livestock feed durability. As regulations tighten and demand grows, VidePak’s commitment to innovation ensures it remains at the forefront of packaging excellence.
External Links for Further Reading:
- Explore how moisture-proof designs enhance feed storage.
- Learn about sustainable practices in PP bag production.
This report integrates data from ISO standards, peer-reviewed studies, and VidePak’s operational insights to provide a comprehensive analysis of PP woven bags’ role in ensuring health and safety in feed packaging.