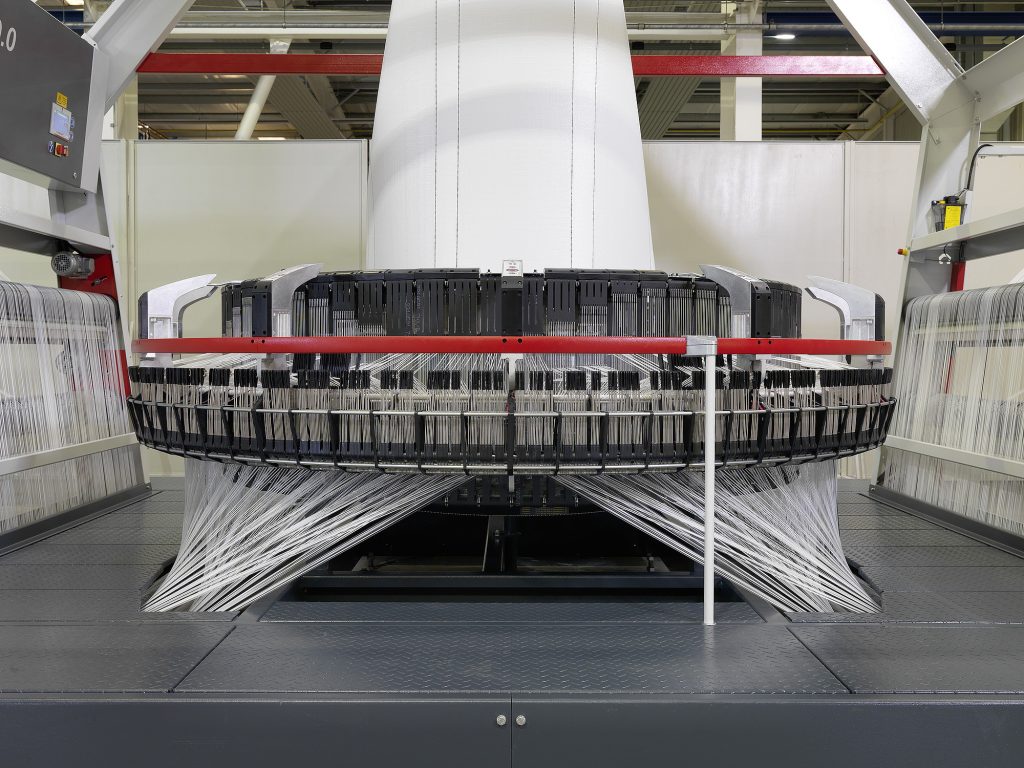
- Market Demand and the Role of PP Bags
- Customization: Meeting Diverse Market Needs
- Technological Edge: Starlinger Machinery and Production Capacity
- Case Study: PP Bags in Action
- Sustainability and Circular Economy
- Product Specifications at a Glance
- FAQs: Addressing Client Concerns
- Future Trends and Strategic Partnerships
By leveraging 30+ years of industry expertise and cutting-edge technology, VidePak has positioned itself as a global leader in manufacturing customizable, durable, and eco-friendly PP woven bags tailored for waste management and recycling. This report explores how the company’s innovative solutions address diverse market demands while aligning with sustainability goals.
Market Demand and the Role of PP Bags
The global waste management sector is projected to reach $530 billion by 2025, driven by urbanization and regulatory pressures to reduce landfill dependence. Polypropylene (PP) woven bags, known for their strength, reusability, and recyclability, have emerged as critical tools for efficient waste segregation, transportation, and recycling. For instance, VidePak’s PP bags are engineered to withstand heavy loads (up to 50 kg) and harsh environments, making them ideal for construction debris, industrial waste, and municipal recycling programs.
Key Insight from Industry Experts
Ray, CEO of VidePak, emphasizes:
“Our clients don’t just need bags—they need tailored solutions. Whether it’s a valve design for powder waste or UV-resistant coatings for outdoor storage, customization is non-negotiable in today’s competitive landscape.”
Customization: Meeting Diverse Market Needs
VidePak’s strength lies in its ability to deliver bespoke PP bag solutions across industries. Below are critical customization options and their applications:
1. Structural Customization
- Valve Design: Ideal for fine-grained materials like cement or chemical powders. VidePak’s pasted valve bags ensure dust-free filling, reducing workplace contamination.
- Reinforced Handles and Gussets: For heavy-duty waste, such as construction rubble, bags with double-stitched handles and side gussets improve load stability.
- Perforations and Ventilation: Custom airflow openings prevent moisture buildup in organic waste collection, addressing odor issues.
2. Material and Durability Enhancements
- Thickness (80–200 GSM): Thicker bags (150+ GSM) are used for sharp industrial waste, while lighter variants suit household recycling.
- Laminated Layers: BOPP or PE coatings add waterproofing, crucial for coastal municipalities managing monsoon-season waste.
3. Branding and Compliance
- Multi-Color Printing: High-definition branding supports municipal campaigns (e.g., “Recycle Right” initiatives).
- Regulatory Labels: Pre-printed hazard symbols or recycling instructions ensure compliance with EU/EPA standards.
Technological Edge: Starlinger Machinery and Production Capacity
VidePak’s 100+ circular looms and 30+ lamination machines (Austrian Starlinger systems) enable rapid scalability. For example:
- Speed: Producing 2,000 bags/hour per loom, the company meets bulk orders (e.g., 500,000 bags for a European waste conglomerate) within 72 hours.
- Precision: Advanced extrusion lines ensure uniform thread density (10×10 strands/cm²), enhancing tensile strength by 40% compared to industry averages.
Case Study: PP Bags in Action
Client: A U.S.-based recycling firm managing e-waste.
Challenge: Sharp components (e.g., circuit boards) punctured standard bags during transit.
Solution: VidePak engineered anti-puncture PP bags with:
- 180 GSM thickness + PE inner lining.
- Double-layered bottom stitching.
- Custom printing for OSHA compliance.
Outcome: Reduced bag failure rate by 92%, saving $220,000 annually in replacement costs.
Sustainability and Circular Economy
PP bags are inherently recyclable, but VidePak goes further:
- Post-Consumer Recycled (PCR) Content: 30% PCR-PP bags reduce virgin plastic use, aligning with ESG commitments.
- Closed-Loop Programs: Partnering with waste processors, VidePak reclaims used bags for pelletizing, cutting carbon footprints by 25%.
Product Specifications at a Glance
Parameter | Range/Options | Application Example |
---|---|---|
Capacity | 5–50 kg | Construction debris (25–50 kg) |
Thickness | 80–200 GSM | Food waste (100 GSM) |
Printing | Up to 8 colors, HD resolution | Municipal branding |
Valve Types | Pasted, sewn, or heat-sealed | Chemical powders |
Coating | BOPP, PE, UV-resistant | Outdoor storage |
FAQs: Addressing Client Concerns
Q1: How do PP bags compare to traditional plastic sacks?
A: PP bags offer 3x greater tensile strength and reusability, reducing long-term costs by 60%.
Q2: Can VidePak handle small-batch custom orders?
A: Yes! Minimum order quantities start at 5,000 units, with prototyping in 7 days.
Q3: Are PP bags suitable for food-grade waste?
A: Absolutely. FDA-approved liners and anti-microbial coatings ensure safety.
Future Trends and Strategic Partnerships
With the rise of smart waste management systems, VidePak is integrating QR codes and RFID tags into bags for real-time tracking. Collaborations with firms like Splunk (data analytics) further optimize waste logistics.
External Resources
- Learn how recyclable PP bags drive circular economies.
- Explore custom printing technologies for brand-centric solutions.
Conclusion
VidePak’s fusion of customization, scalability, and sustainability positions PP woven bags as indispensable tools in modern waste management. By continuously innovating—whether through material science or IoT integration—the company remains at the forefront of a $800 million global market, proving that “one-size-fits-all” is obsolete in the age of precision waste solutions.