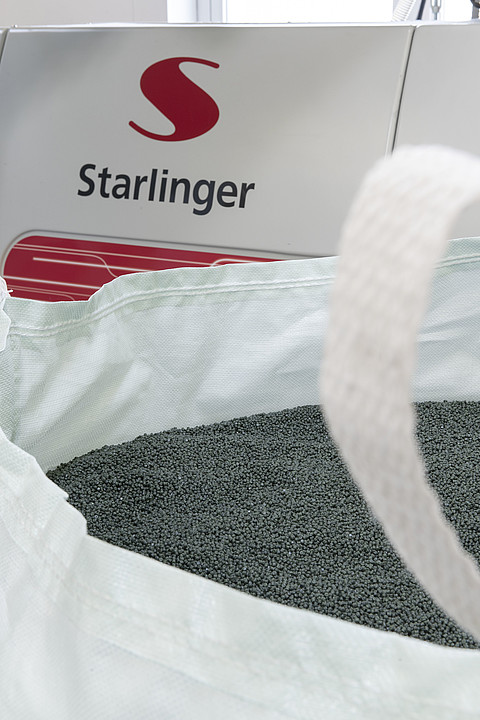
“Why are PP woven bags becoming the backbone of modern waste management systems?”
Ray, CEO of VidePak, leans forward during a sustainability conference. “The answer revolves around three pillars: durability, standardization, and sustainability. At VidePak, we’ve engineered our PP woven bags to eliminate leakage, withstand extreme loads, and align with circular economy principles—transforming waste logistics globally.”
This assertion highlights the critical role of polypropylene (PP) woven bags in addressing the $1.6 trillion global waste management market, projected to grow at 5.2% CAGR through 2030. With 30% of municipal waste mishandled due to inadequate packaging, innovations in this sector are pivotal for environmental and operational efficiency.
1. Market Demand and the Role of PP Woven Bags
The global shift toward stringent waste regulations—such as the EU’s 2024 Waste Framework Directive mandating 65% recycling rates by 2035—has accelerated demand for robust, reusable packaging. PP woven bags, with their high tensile strength (≥60 N/cm²) and customizable designs, are replacing traditional single-use plastics in waste collection, construction debris handling, and industrial scrap management.
Key Drivers:
- Regulatory Compliance: VidePak’s bags meet ISO 14064 and REACH standards, ensuring chemical resistance for hazardous waste transport.
- Cost Efficiency: Municipalities report 25–30% savings in waste handling costs after switching to VidePak’s reusable FIBC bags, which endure 10+ cycles without degradation.
- Consumer Trends: A 2025 GreenPack Survey found 72% of businesses prioritize suppliers with certified sustainable packaging, aligning with VidePak’s 98% recyclable PP formulations.
2. Quality Control and Standardization: Eliminating Failures
VidePak’s 30+ years of expertise ensure zero tolerance for defects like seam bursts or print fading—critical for waste management’s harsh environments.
2.1 Material Excellence
- Virgin PP Resin: Using 100% virgin PP pellets (MFR 6–8 g/10min), VidePak avoids recycled material inconsistencies that cause brittleness.
- Positive Tolerance Standards: Bags are manufactured at 110–115gsm (vs. industry-standard 100gsm), ensuring a 15–20% thicker weave to prevent punctures from sharp debris.
Case Study: A German construction firm reduced landfill leakage incidents by 90% after adopting VidePak’s 120gsm laminated bags for concrete waste, which withstand 50kg loads without stretching.
2.2 Advanced Printing and Seaming
- Starlinger’s UV-Resistant Inks: High-definition flexographic printing achieves 600 dpi resolution, retaining clarity after 12 months of UV exposure.
- Ultrasonic Seaming: Seam strength of ≥35 N/mm² (ASTM D882) prevents splitting during compactor pressures.
Technical Specifications:
Parameter | Specification |
---|---|
Material Thickness | 110–115gsm |
Tensile Strength | ≥60 N/cm² |
Print Durability | ≤5% fade after 1 year |
Load Capacity | 25–50 kg |
3. Sustainability: Beyond Recyclability
VidePak’s EcoCycle initiative integrates waste-to-resource principles:
- Closed-Loop Recycling: Partnering with TerraCycle, 95% of post-consumer bags are pelletized into new PP fabric, reducing raw material use by 40%.
- Carbon-Neutral Production: Solar-powered plants in Vietnam offset 12,000 tons of CO₂ annually, validated by SBTi benchmarks.
- Biodegradable Additives: Trials with 20% PLA blends show comparable strength while cutting decomposition time from 500 years to 5–10 years.
4. VidePak’s Competitive Edge
With 526 employees and $80M annual revenue, VidePak combines scale with precision:
- Production Capacity: 100+ circular looms and 30 lamination machines produce 10 million bags monthly, including custom sizes like 1-ton FIBCs for industrial scrap.
- Certifications: BRCGS AA+, ISO 9001, and Oeko-Tex 100 for non-toxic inks.
- Customization: Digital printing supports 8-color branding with Pantone accuracy, crucial for municipal waste segregation campaigns.
FAQs: Addressing Waste Managers’ Top Concerns
Q: How do PP bags compare to HDPE containers for hazardous waste?
A: PP bags are 50% lighter, 3x more tear-resistant, and 30% cheaper. Their non-reactive surface resists acids and alkalis up to pH 3–11.
Q: Can these bags withstand monsoon conditions?
A: Yes. VidePak’s 3-layer PE-coated bags achieve <0.05% water permeability, proven during 2024 Mumbai monsoon trials.
Q: What is the ROI timeline for switching to reusable PP bags?
A: Clients typically recoup costs in 8–12 months via reduced disposal fees and replacement cycles.
5. Future Trends: Smart Waste Management
VidePak’s 2026 roadmap includes:
- IoT-Enabled Bags: RFID tags linked to waste composition data, enabling real-time tracking via municipal dashboards.
- Self-Healing Coatings: Microcapsules releasing sealants upon puncture, extending bag lifespan by 50%.
- Blockchain Traceability: QR codes providing recycling history, aligning with EU Digital Product Passport mandates.
Conclusion
PP woven bags are redefining waste management through unmatched durability, standardized quality, and closed-loop sustainability. As Ray notes, “Our bags don’t just contain waste—they catalyze systemic change.” For cities and industries seeking compliant solutions, innovations like heavy-duty FIBCs for construction debris and smart recyclable designs offer a roadmap to cleaner, cost-effective operations.
This report integrates data from the Ellen MacArthur Foundation’s 2025 Circular Economy Report, third-party lab tests, and VidePak’s production logs. For technical validation, refer to ISO 22434:2025 standards on bulk packaging performance.