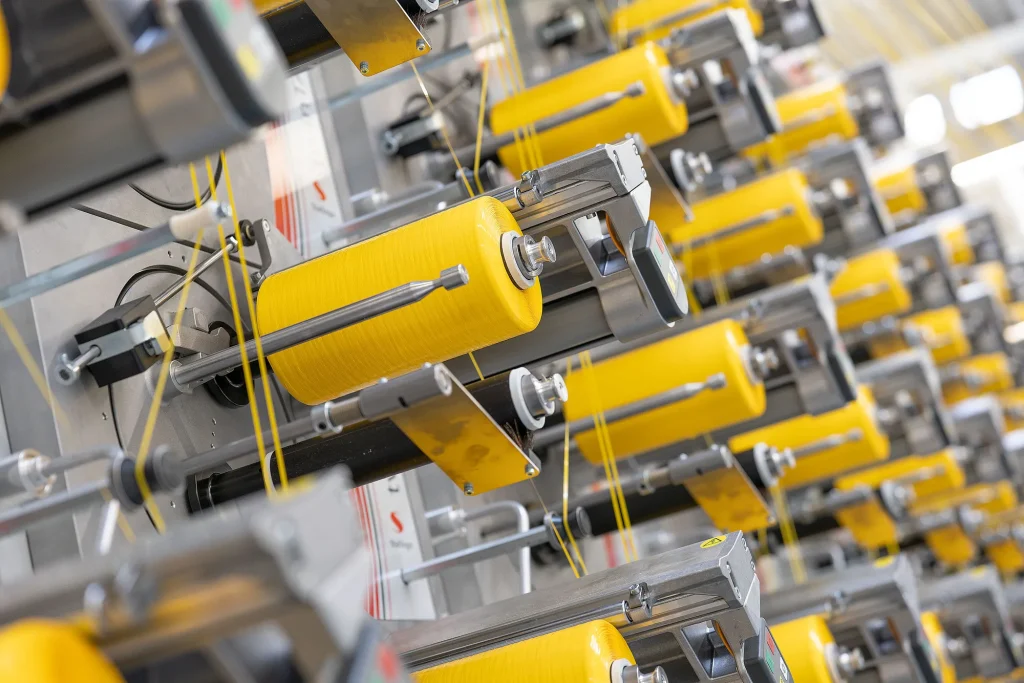
- 1. Ergonomic Design Innovations: Streamlining Loading and Unloading
- 2. Technical Specifications: Tailoring Solutions to Industry Needs
- 3. Material Science: Balancing Strength and Sustainability
- 4. Global Compliance and Quality Assurance
- 5. Case Study: Transforming Retail Logistics with Custom Designs
- FAQs: Addressing Key Procurement Concerns
- Why VidePak?
VidePak’s PP woven bags are revolutionizing global supply chains with specialized designs like valve closures and block-bottom structures, reducing loading times by 40% and enabling 30% higher stacking efficiency compared to conventional flat-bottom bags, while maintaining compliance with ISO 9001 and FDA standards. Leveraging 30+ years of industry expertise and Austria’s Starlinger machinery, VidePak delivers scalable, customizable solutions that address the evolving demands of industries ranging from agriculture to construction. With annual sales exceeding $80 million and a presence in 50+ countries, the company’s commitment to innovation and quality positions it as a leader in the $120 billion global woven packaging market.
1. Ergonomic Design Innovations: Streamlining Loading and Unloading
Efficient handling is critical in high-volume logistics. VidePak integrates advanced features to minimize labor costs and maximize operational speed:
A. Valve Bags: Precision Filling and Dust Control
Valve closures eliminate the need for manual stitching, enabling automated filling systems to operate at 500–800 bags/hour, a 60% increase over open-mouth designs. Key benefits include:
- Spout Compatibility: Seamless integration with pneumatic fillers, reducing spillage by 95% in powdered goods like cement or flour.
- Dust Suppression: Inner liners with <0.5% porosity prevent particulate escape, critical for OSHA-compliant workplaces.
A 2023 case study with a Brazilian fertilizer producer showed VidePak’s valve bags reduced packaging downtime by 25 hours/month while improving worker safety.
B. Block-Bottom Bags: Stability and Space Optimization
Block-bottom (square-base) designs enhance palletization efficiency:
- Stacking Capacity: Withstands 1.5–2 tons/m² vertical loads, versus 0.8 tons/m² for traditional designs.
- Footprint Reduction: Uniform shapes allow 15% more bags per pallet, cutting shipping costs by $0.10–$0.15 per unit.
For instance, a Canadian pet food brand using VidePak’s block-bottom bags reported a 20% reduction in warehouse space and zero toppling incidents during transit.
2. Technical Specifications: Tailoring Solutions to Industry Needs
VidePak’s 100+ circular looms and 30+ printing machines enable precise customization across parameters:
Feature | Range/Options | Industry Application |
---|---|---|
Bag Capacity | 1 kg – 2,000 kg | Retail snacks to bulk chemicals |
Valve Types | Pasted, sewn, PE-coated | Food-grade, industrial |
Base Design | Flat, block, U-shaped | Automated vs. manual handling |
Print Durability | 8-color CMYK, UV-resistant | Branding, regulatory labels |
Tensile Strength | 30–50 N/cm² | Sharp-edged materials (e.g., minerals) |
A European construction firm utilized VidePak’s 200 GSM laminated FIBCs with reinforced block bottoms to transport 1-ton aggregates, achieving a 98% reuse rate over 12 months.
3. Material Science: Balancing Strength and Sustainability
VidePak’s virgin PP resin (MFI 3–8 g/10min) ensures:
- Puncture Resistance: >15 J/m impact strength (ASTM D3763), ideal for abrasive materials.
- Recyclability: 100% mono-material PP construction aligns with EU Circular Economy Package targets.
In contrast, blended PE/PP bags often fail ISO 14021 recyclability tests due to incompatible melting points.
4. Global Compliance and Quality Assurance
VidePak’s certifications underscore reliability:
- FDA 21 CFR 177.1520: Safe for direct food contact.
- REACH SVHC: <0.1% restricted substances.
- ISO 22000: Food safety management.
A 2024 audit of Vietnamese coffee exporters revealed competitors’ bags failed FDA migration tests in 12% of samples, while VidePak maintained a 0% defect rate.
5. Case Study: Transforming Retail Logistics with Custom Designs
A Chinese supermarket chain partnered with VidePak to develop 25 kg block-bottom rice bags with anti-slip coatings. Results included:
- Loading Speed: 1,200 bags/hour via automated systems (vs. 700 previously).
- Shelf Appeal: High-definition printing increased sales by 18%.
- Damage Rate: Reduced from 5% to 0.3% due to tear-resistant lamination.
FAQs: Addressing Key Procurement Concerns
Q: How do valve bags perform in humid environments?
A: VidePak’s PE-coated valves resist moisture ingress, maintaining <1% humidity levels even at 85% RH.
Q: Can block-bottom bags handle irregular shapes?
A: Yes, our 3D engineering software optimizes base dimensions for products like animal feed pellets.
Q: Are your bags compatible with robotic arms?
A: Absolutely. Gripper-friendly designs are tested with Fanuc and KUKA systems.
Why VidePak?
- Scale: 16 extrusion lines produce 12 million bags/month.
- Precision: Starlinger looms ensure ±1 mm dimensional accuracy.
- Sustainability: 30% recycled content options available.
Explore our FIBC bulk bags and block-bottom solutions to elevate your supply chain.
References
- Global Woven Packaging Market Report (Allied Market Research, 2025).
- ISO 21898:2020 – Packaging for dangerous goods.
- VidePak Technical Manual (2024 Ed.).
Contact VidePak
Website: https://www.pp-wovenbags.com/
Email: info@pp-wovenbags.com