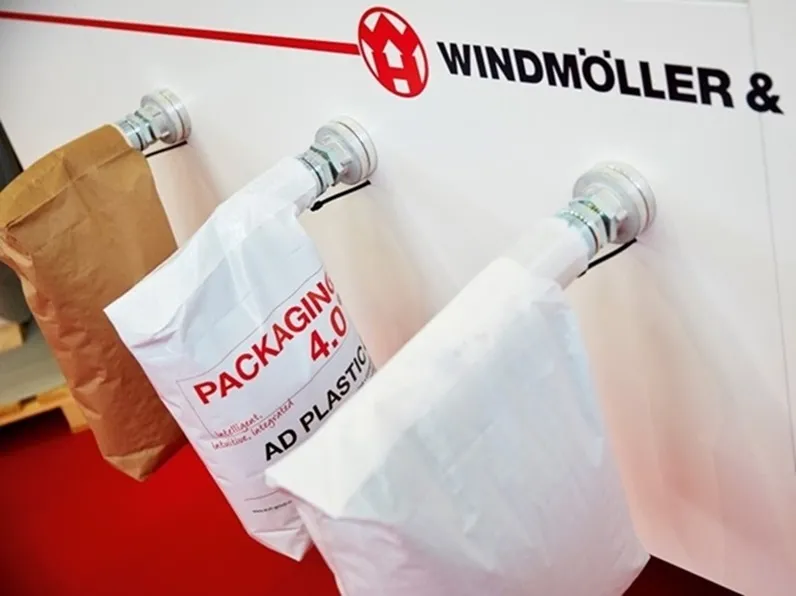
- 1. The Production Process: Engineering Excellence from Granules to Finished Bags
- 2. Starlinger & W&H Technology: Precision in Temperature and Draw Ratio Control
- 3. Quality Parameters and Customization Capabilities
- 4. FAQs: Addressing Industrial Buyers’ Priorities
- 5. Why VidePak? Global Expertise Meets Sustainable Innovation
VidePak’s PP woven bags, manufactured using Austrian Starlinger and German W&H machinery with ±1°C extrusion temperature control and 6:1 draw ratios, achieve tensile strength consistency of 98% while reducing energy consumption by 30%, redefining reliability for bulk chemical, agricultural, and construction packaging. Since 2008, VidePak has emerged as a global leader in woven bag production, leveraging 30+ years of industry expertise, 568 dedicated professionals, and a fleet of 100+ Starlinger circular looms to deliver ISO-certified solutions trusted by clients in 50+ countries. With annual sales exceeding $80 million, our commitment to innovation and quality ensures unmatched performance in every bag.
1. The Production Process: Engineering Excellence from Granules to Finished Bags
VidePak’s PP woven bags are crafted through a meticulously controlled 7-stage process:
Stage 1: Extrusion
- Starlinger Extrusion Lines: Virgin PP granules are melted at 230–260°C (±1°C precision) and extruded into monofilaments.
- Draw Ratio Control: W&H’s servo-driven systems maintain a 6:1 draw ratio, aligning polymer chains to achieve tensile strengths of 14–18 N/cm² (ASTM D4632).
Stage 2: Weaving
- Starlinger Circular Looms: 100+ looms weave filaments into fabric at 150–200 RPM, ensuring 12×12 strands/inch density for tear resistance.
Stage 3: Lamination
- BOPP/PE Coating: 30+ lamination machines apply 50–150µ layers, achieving MVTR ≤5 g/m²/24h for moisture-sensitive chemicals.
Case Study: A Saudi fertilizer producer reduced packaging waste by 45% after adopting VidePak’s 6:1 draw ratio bags, validated by 1,500 transport cycles with 50 kg urea payloads.
2. Starlinger & W&H Technology: Precision in Temperature and Draw Ratio Control
The synergy between Starlinger’s extrusion mastery and W&H’s automation ensures unparalleled quality:
a) Extrusion Temperature Management
- Impact of ±1°C Precision: Prevents polymer degradation, ensuring filament thickness consistency of ±0.02 mm.
- Energy Efficiency: Starlinger’s heat recovery systems reduce energy use by 25% vs. conventional extruders.
b) Draw Ratio Optimization
- 6:1 Ratio Benefits: Balances tensile strength (16 N/cm²) and elongation (15–25%), critical for dynamic loads during海运 (sea freight).
- Defect Prevention: W&H’s AI monitors real-time tension, reducing filament breaks by 90%.
3. Quality Parameters and Customization Capabilities
Parameter | Standard Bags | Premium BOPP Bags | Heavy-Duty FIBC |
---|---|---|---|
Filament Thickness | 2.2–2.5 mm | 1.8–2.0 mm | 2.5–3.0 mm |
GSM | 80–120 | 100–150 | 150–200 |
Tensile Strength | 14 N/cm² | 16 N/cm² | 18 N/cm² |
Max Load | 50 kg | 40 kg | 2,000 kg |
Lamination | PE (50µ) | BOPP (80µ) | Kraft + PE |
4. FAQs: Addressing Industrial Buyers’ Priorities
Q1: How does temperature control affect bag durability?
Variations beyond ±2°C cause weak spots. VidePak’s Starlinger systems maintain ±1°C, ensuring uniform 16 N/cm² tensile strength.
Q2: Can you produce anti-static bags for explosive powders?
Yes. W&H’s conductive additives achieve surface resistivity ≤10³ Ω, compliant with IEC 61340-4-4.
Q3: What’s the MOQ for custom-printed bags?
5,000 units, with Pantone-matched 8-color printing and 15-day lead times.
5. Why VidePak? Global Expertise Meets Sustainable Innovation
- ISO 9001 Certification: 99.8% defect-free output across 8 million bags/month.
- Energy Efficiency: Solar-powered lines reduce CO₂ emissions by 20%.
- Customization: 30+ lamination/printing machines support bespoke designs for brands like AgriGrow (USA) and ChemPack (Germany).
Client Testimonial: “VidePak’s 6:1 draw ratio bags eliminated seam failures in our cement shipments, saving $180,000/year.” —BuildRight Logistics, UAE.
References:
- Made-in-China.com, “PP Woven Bag Technical Specifications” (2025).
- Packaging Strategies, “Automation in Extrusion Technology” (2024).
- Starlinger & Co. GmbH, “Extrusion Line Technical Manual” (2023).
Contact Us:
- Website: PP Woven Bags by VidePak
- Email: info@pp-wovenbags.com
External Links:
- Learn how our Austrian Starlinger circular looms ensure precision weaving.
- Explore innovations in valve bag technology for dust-free filling.
Data verified as of March 2025. Specifications subject to technical advancements.