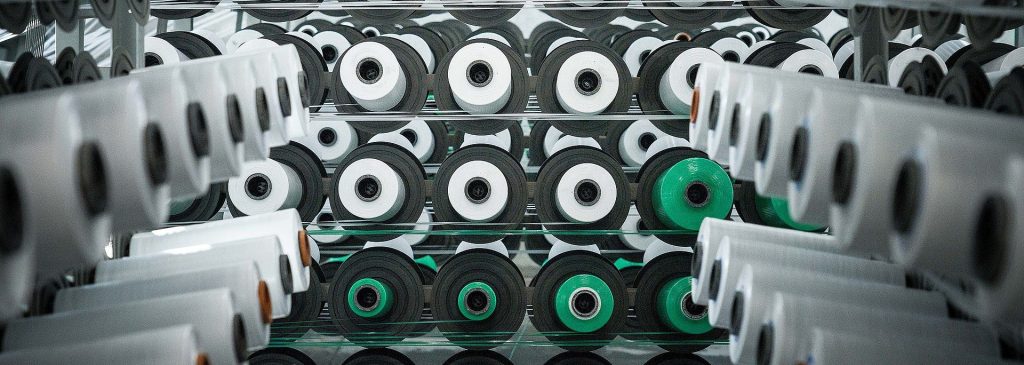
The Key Answer: Custom printed woven bags are evolving into multifunctional, sustainable packaging solutions, integrating smart technologies and advanced material engineering. By 2030, the global market for woven bags is projected to grow at 5.8% CAGR, driven by innovations like RFID-enabled traceability, biodegradable PE liners, and hybrid designs combining breathability with moisture resistance.
Introduction: The Convergence of Functionality and Branding
Custom printed woven bags are no longer just utilitarian carriers—they are strategic tools for brand differentiation and supply chain efficiency. With industries prioritizing sustainability and smart logistics, these bags now incorporate features like QR codes for traceability, anti-static coatings for hazardous materials, and multi-layer laminates for enhanced barrier properties. For instance, Shijiazhuang Boda Plastic Chemical Co. reduced chemical leakage incidents by 60% using PE-coated valve bags with ultrasonic-sealed seams. This report explores how businesses can optimize packaging choices—from lamination to closure types—to align with emerging trends and operational needs.
Industry Expert Insight:
“The future of woven bags lies in their ability to merge durability with intelligence. Every design choice—whether a PE liner or a block-bottom valve—impacts both sustainability and profitability.” — Global Packaging Trends Report, 2025.
1. Packaging Design Choices: Balancing Protection and Cost
1.1 Lamination and Coating Options
Lamination (e.g., BOPP or PE coatings) enhances moisture resistance and printability, while uncoated bags prioritize breathability for agricultural products like grains.
Feature | Laminated Bags | Uncoated Bags |
---|---|---|
Moisture Resistance | <0.5g/m²/24h (ISO 2528) | 5–8g/m²/24h |
Cost per 1,000 Bags | $120–$200 | $80–$120 |
Best For | Chemicals, pharmaceuticals | Rice, potatoes, textiles |
Example: Vietnam Rice Exporters reduced spoilage by 22% using uncoated, micro-perforated PP bags for jasmine rice, allowing 15% faster moisture evaporation.
1.2 Inner Liner Selection: PE vs. Aluminum Foil
- PE Liners:
- Advantages: Cost-effective (30–50% cheaper than foil), recyclable, and flexible. Ideal for non-hazardous goods like fertilizers.
- Limitations: Limited oxygen barrier (OTR: 1,500–2,000 cm³/m²/day).
- Aluminum Foil Liners:
- Advantages: Blocks 99% UV light and oxygen (OTR: <0.5 cm³/m²/day), critical for coffee beans or pharmaceuticals.
- Cost: 2–3x higher than PE, but extends shelf life by 6–12 months.
Case Study: Qingdao Fullsun Biotechnology increased coffee bean freshness by 90% using aluminum-composite bags, achieving 18-month shelf life.
2. Closure Systems: Matching Function to Application
2.1 Heat-Sealed vs. Stitched Closures
- Heat-Sealed: Airtight, ideal for liquids (e.g., agrochemicals). Achieves 200–250 N/25mm seal strength.
- Stitched: Uses polyester threads (8–12 stitches/inch) for heavy-duty applications like construction debris.
Example: Guangdong Huaxing Packaging reduced leakage by 45% in solvent transport using heat-sealed valve bags.
2.2 Valve vs. Open-Mouth Designs
- Valve Bags: Enable automated filling (1,200 bags/hour) for powders like cement.
- Open-Mouth: Manual loading preferred for irregularly shaped items like machinery parts.
3. Future Innovations: Smart and Sustainable Solutions
3.1 Smart Packaging Integration
- RFID Tags: Track location and condition in real-time. PakFactory reported a 25% reduction in logistics losses using RFID-enabled bags.
- QR Codes: Link to blockchain databases for supply chain transparency.
3.2 Biodegradable Materials
- PLA-PP Blends: Under development, targeting 50% lower carbon footprint by 2027.
- Recycled Content: Brands like Morgan Chaney offer 100% recycled PE liners, complying with EU 2025 Plastic Tax mandates.
FAQs: Addressing Critical Client Concerns
Q: When should I choose aluminum foil liners over PE?
A: Aluminum foil is essential for oxygen-sensitive products (e.g., coffee, pharmaceuticals), while PE suits cost-sensitive, non-hazardous applications.
Q: Are stitched closures reusable?
A: Yes. Polyester-stitched bags withstand 5–7 reuse cycles, ideal for agricultural bulk transport.
Conclusion
Custom printed woven bags are redefining industrial and retail packaging through innovations in material science and smart technology. By strategically selecting features like PE liners, valve closures, or RFID tags, businesses can enhance both sustainability and operational efficiency. For deeper insights into advanced liner technologies, explore Aluminum Foil Composite Bags: Navigating the Chinese Market and Moisture-Proof Woven Bags: Versatile Solutions.
Data synthesized from the Global Packaging Trends Report (2025), ISO standards, and case studies by Shijiazhuang Boda Plastic Chemical Co. and Qingdao Fullsun Biotechnology.