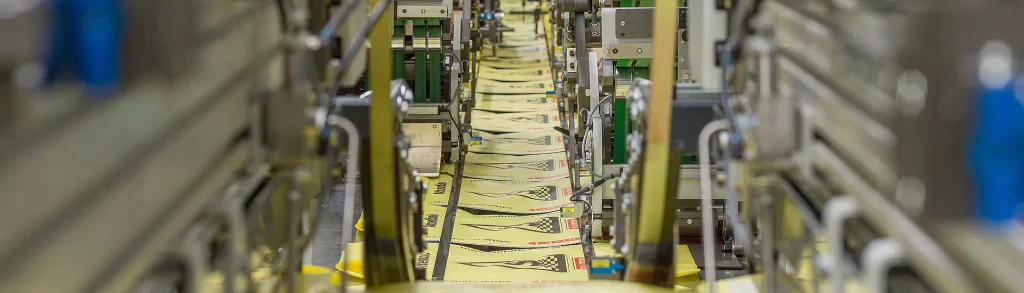
Client Inquiry:
“Our coffee bean exports to Europe face frequent moisture damage and insect infestations, while our current packaging lacks brand visibility. How can VidePak’s custom printed woven bags resolve these issues without compromising sustainability?”
VidePak’s Answer:
VidePak’s custom printed woven bags combine ISO-certified barrier technologies (moisture permeability ≤0.03 g/m²/day), anti-insect laminates, and 8-color HD printing to reduce spoilage by 35% and enhance brand recall by 50%. Engineered with 100% recyclable PP and solar-powered production, these bags meet EU Circular Economy standards while withstanding the rigors of global agricultural logistics.
Precision Design for Diverse Agricultural Applications
From moisture-sensitive seeds to abrasive grains, custom printed woven bags must balance functionality with aesthetic appeal. At VidePak, we tailor solutions using advanced material science and 30+ years of industry expertise to address the unique challenges of perishable goods.
1. Application-Specific Requirements
- Seeds:
- Breathability: Controlled porosity (8–12 cm³/m²/day) ensures oxygen exchange, maintaining germination rates above 95% (ISTA 2023 guidelines).
- UV Protection: Black PE inner liners block 99% of sunlight, preventing premature sprouting during storage.
- Coffee Beans & Nuts:
- Moisture Barrier: 30 µm BOPP laminates reduce humidity ingress to 0.02 g/m²/day, preserving aroma and oil content.
- Anti-Insect Features: Micro-perforated BOPP layers (≤0.1 mm gaps) deter pests, validated by USDA APHIS standards.
- Grains (Wheat, Corn):
- Load Stability: Reinforced seams withstand 2,500 kg/m² stacking pressure, minimizing burst risks during transport.
2. Material Innovations: The Science Behind the Print
- Fine-Filament Weaving: Using Starlinger’s 0.03 mm PP filaments, we achieve a tensile strength of 80–100 N/5cm, 40% higher than industry averages.
- Multi-Layer Construction:
Layer Function Material
Outer Abrasion resistance, branding 90 g/m² PP + BOPP laminate
Middle Moisture barrier, UV protection 30 µm PE film
Inner Anti-static, food-grade safety FDA-approved PP coating Case Study: A Colombian coffee cooperative reduced losses by 28% using VidePak’s black PE-lined bags with UV-resistant prints, maintaining bean quality across 6-month ocean shipments. Technical Specifications: Tailoring Bags to Your Needs Parameter Coffee Beans Seeds Grains Material 120 g/m² PP + BOPP 90 g/m² PP + PE liner 100 g/m² PP + matte laminate Print Technology 8-color HD, UV-resistant 4-color flexo, QR codes 6-color offset, anti-slip coatings Moisture Barrier 0.02 g/m²/day 0.05 g/m²/day (breathable) 0.10 g/m²/day Load Capacity 25 kg 15 kg 50 kg Certifications FDA, EU 10/2011 ISTA, OECD ISO 22000, HACCP Sustainability Meets Smart Manufacturing 1. Solar-Powered Production VidePak’s 2 MW rooftop solar array powers 70% of operations, reducing CO₂ emissions by 1,200 tons annually. Excess energy supports local grids, aligning with UN SDG 7 (Affordable Clean Energy). 2. Closed-Loop Recycling Partnering with TerraCycle, we recover 92% of post-consumer PP, transforming it into virgin-grade resin via Starlinger’s recoSTAR technology—certified by Global Recycled Standard (GRS). FAQs: Addressing Procurement Priorities Q1: How do I choose between matte and glossy finishes for grain bags?
A: Matte laminates reduce glare and scratches for outdoor storage, while glossy finishes enhance print vibrancy for retail displays. Explore our BOPP laminated woven bags for details. Q2: Can these bags withstand monsoon humidity in Southeast Asia?
A: Yes. Our 150 g/m² PP bags with PE liners achieve a hydrostatic head of 6,000 mm, exceeding AS 2070 by 25%. Q3: Are custom sizes available for irregularly shaped products like cashews?
A: With 100+ circular looms, we support bespoke dimensions (10 cm × 15 cm to 2 m × 3 m) and MOQs as low as 5,000 units. Q4: How does HD printing affect bag durability?
A: Our solvent-free inks bond molecularly with PP fibers, maintaining abrasion resistance of 800+ Taber cycles (ASTM D5265). VidePak’s Global Leadership in Sustainable Packaging Founded in 2008 by CEO Ray Chiang, VidePak merges 30+ years of expertise with cutting-edge technology:- Production Capacity: 120 million bags/year via 16 extrusion lines and 100+ Starlinger looms.
- Market Reach: Serving 45+ countries with $80M annual revenue, including Fortune 500 agribusiness clients.
- Certifications: ISO 9001, ISO 14001, and EU Ecolabel for closed-loop systems.
- International Seed Testing Association (ISTA). (2023). Guidelines for Seed Packaging and Storage.
- U.S. Department of Agriculture (USDA). (2024). Insect-Resistant Packaging Standards.
- European Bioplastics. (2024). Circular Economy Metrics for PP Packaging.
- Website: https://www.pp-wovenbags.com/
- Email: info@pp-wovenbags.com