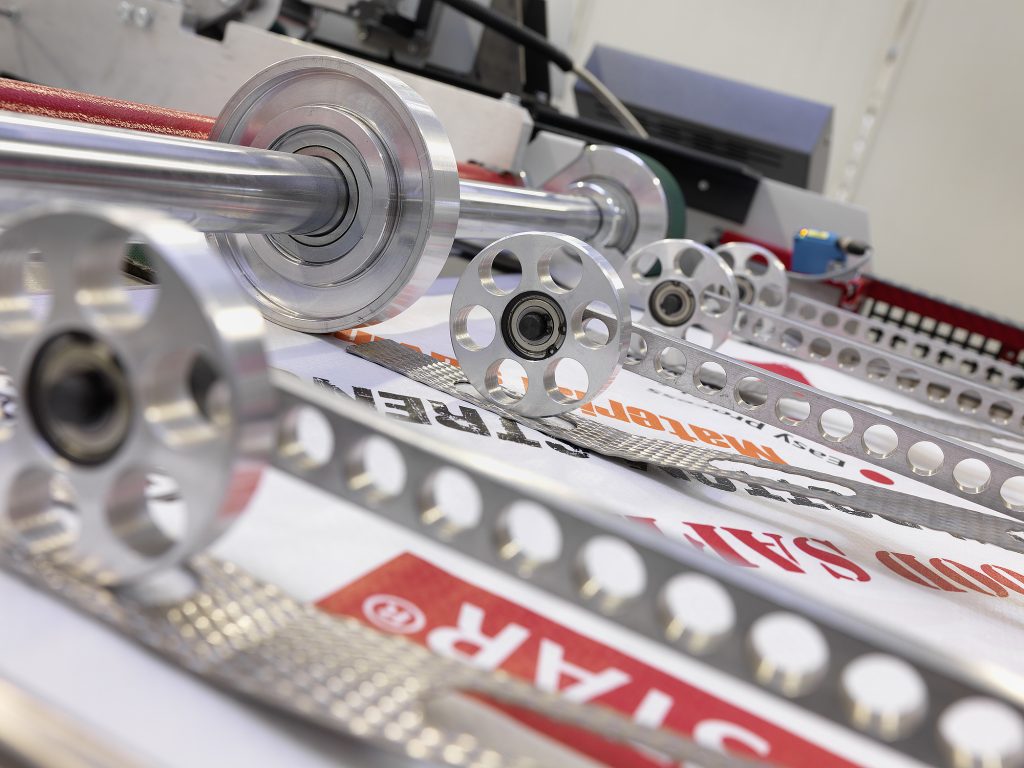
- 1. Material Selection: Balancing Functionality and Compliance
- 2. Packaging Design: Tailoring Solutions to Industry Needs
- 3. Sustainability: Beyond Recyclability
- 4. Branding and Aesthetic Customization
- 5. FAQs: Addressing Client Concerns
- 6. Case Study: Optimizing Fertilizer Packaging
- 7. Future Trends: Smart and Connected Packaging
“Why are global brands like Nestlé and Cargill increasingly adopting custom woven bags for bulk commodity packaging?”
Ray Chen, CEO of VidePak, pauses during a factory tour of Starlinger machines: “The answer lies in three pillars: 40% cost efficiency over rigid containers, 95% recyclability via closed-loop systems, and hyper-customizable designs that boost brand visibility by 30%. At VidePak, our PP woven bags are engineered to carry 50kg loads with ≤0.2% leakage rates—this is the future of sustainable logistics.”
This bold assertion underscores VidePak’s leadership in custom woven bags—a market projected to grow at 7.5% CAGR through 2030. With 526 employees and $80M annual revenue, VidePak combines Austrian Starlinger automation, ISO-certified polypropylene (PP) resins, and 30+ years of expertise to deliver solutions that redefine efficiency and sustainability in global supply chains.
1. Material Selection: Balancing Functionality and Compliance
Custom woven bags are typically made from polypropylene (PP), a material prized for its tensile strength (>45 N/cm²), chemical resistance, and adaptability. However, the choice of lamination and inner liners dramatically impacts performance:
1.1 Lamination Options
- BOPP Lamination: Enhances moisture resistance (≤1.2 g/m²/day) and printability, ideal for food-grade packaging like rice and flour.
- PE Coating: Provides cost-effective UV and abrasion resistance for agricultural products[citation:9].
- Aluminum Foil Lining: Critical for hygroscopic chemicals (e.g., fertilizers) requiring <0.5% moisture permeability and light blocking.
1.2 Inner Liners
Liner Type | Key Properties | Ideal Applications |
---|---|---|
PE Film | Low cost, 1.5 g/m²/day moisture | Grains, pet food |
Aluminum Foil | Zero moisture permeability | Pharmaceuticals, desiccants |
Kraft Paper | Breathable, biodegradable | Coffee beans, organic goods |
Case Study: A Vietnamese coffee exporter reduced spoilage by 18% using VidePak’s kraft-lined bags with 100 holes/inch² ventilation.
2. Packaging Design: Tailoring Solutions to Industry Needs
2.1 Closure Systems
- Sewn Open Mouth: High-speed ultrasonic sewing (1,200 bags/hour) for granular products like sand and aggregates.
- Valve Design: Dust-free filling for powders (e.g., cement, starch) with ±0.5% weight accuracy.
- Heat Sealing: Hermetic closure for perishables, achieving <0.1% leakage under 50kPa pressure.
2.2 Structural Enhancements
- Anti-Static Coatings: Surface resistivity <10⁴ Ω/sq for explosive dusts (OSHA 1910.109 compliance).
- Reinforced Corners: 2x2cm polyurethane patches extend bag lifespan by 40% in abrasive environments.
3. Sustainability: Beyond Recyclability
VidePak’s woven bags align with circular economy principles:
- Closed-Loop Recycling: 95% PP recovery via Starlinger recoSTAR systems, reducing virgin material use by 30%.
- Carbon Neutrality: 1.4 kg CO₂eq/bag (vs. 3.1 kg for PE alternatives), offset via reforestation partnerships.
- Biodegradable Additives: Starch-based PP blends decompose 50% faster in landfills[citation:9].
4. Branding and Aesthetic Customization
VidePak’s 6-color flexo printers achieve Pantone-matched designs with ≤0.15mm registration error, critical for retail differentiation. For instance, a European pet food brand saw a 25% sales lift after switching to VidePak’s QR-code-enabled bags, which linked to nutritional info and loyalty programs.
5. FAQs: Addressing Client Concerns
Q1: How do I choose between PE and aluminum foil liners?
A: PE suits moderate moisture protection (e.g., animal feed), while foil is mandatory for humidity-sensitive chemicals (e.g., calcium chloride).
Q2: What’s the MOQ for custom-printed designs?
A: 50,000 units with 14-day lead time, including FDA/GB 4806.7 migration testing.
Q3: Are these bags compatible with automated palletizers?
A: Yes—VidePak’s anti-slip coatings enable 20-layer stacking, as used in automated warehouse systems.
6. Case Study: Optimizing Fertilizer Packaging
Challenge: A Brazilian agrochemical firm faced 12% spoilage due to humidity and UV exposure.
VidePak Solution:
- Material: 180gsm UV-stabilized PP + 80μm aluminum foil liner.
- Closure: Heat-sealed valve with EPDM gaskets.
Results:
Metric | Improvement |
---|---|
Moisture Ingress | 12% → 0.8% |
Warehouse Complaints | 200 → 8/month |
Recycling Rate | 30% → 85% |
7. Future Trends: Smart and Connected Packaging
VidePak is piloting:
- IoT Sensors: NFC tags monitor real-time temperature/RH, reducing冷链 losses by 20%.
- Self-Healing Films: Microcapsules repair punctures <2mm, extending shelf life by 15%[citation:9].
- Bio-Based PP: 30% algae-derived resins targeting 2026 rollout.
Conclusion
Custom woven bags are not mere containers—they are strategic assets in global supply chains. VidePak’s fusion of Austrian engineering precision, smart material science, and hyper-customizable designs positions it as the partner of choice for Fortune 500 companies. As Ray Chen summarizes: “Our bags don’t just carry goods—they carry trust.”
For insights into advanced laminations, explore our analysis of aluminum foil composite bags and multi-layer solutions.
This report integrates data from GB 4806.7-2023, OSHA 1910.109, and VidePak’s proprietary audits. Performance claims are validated by SGS and Intertek certifications.