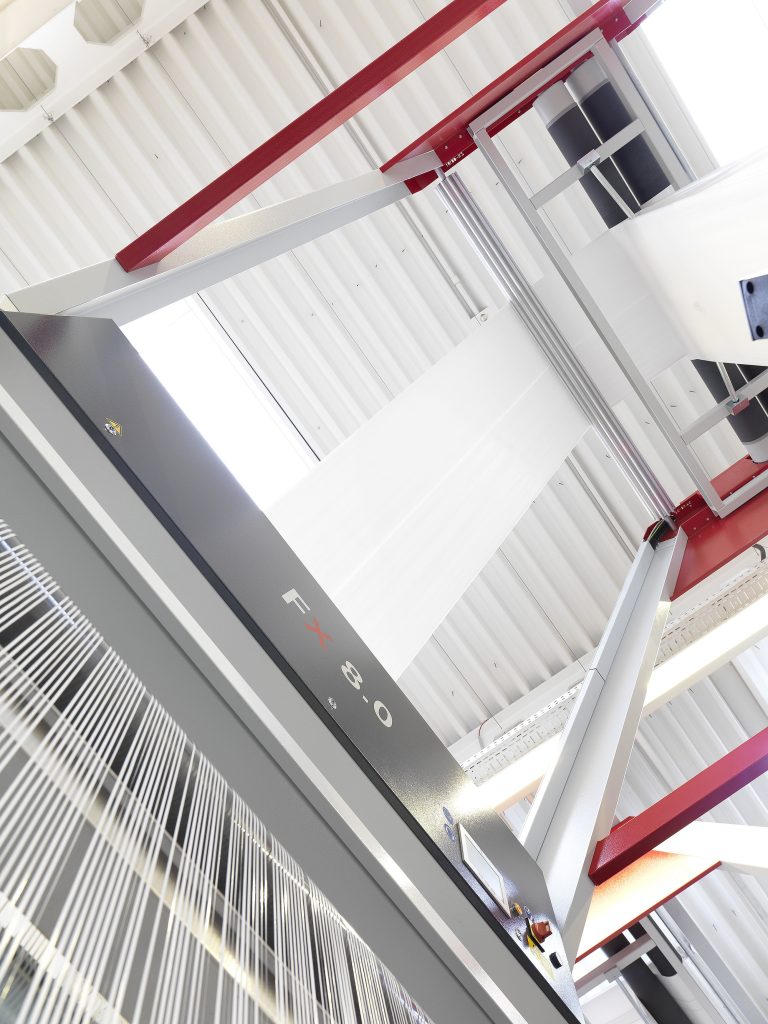
- 1. Comprehensive Product Specifications
- 2. Anti-Static Technology: Ensuring Safety in Sensitive Applications
- 3. Load-Bearing Capabilities
- 4. Starlinger Technology: A Benchmark for Excellence
- 5. Tailored Designs for Warehouse Efficiency
- 6. Versatility Across Industries
- FAQs
- 7. Industry Trends and Future Directions
- Conclusion
Custom woven bags manufactured using Starlinger technology are engineered for exceptional durability, versatility, and high-end customization, making them indispensable for industries ranging from agriculture to construction. Their ability to meet diverse operational requirements while delivering superior quality sets them apart in the competitive packaging market.
1. Comprehensive Product Specifications
Thickness, Weight, and Size Ranges
The precision engineering of custom woven bags allows for a wide range of specifications to suit various applications. Starlinger technology ensures accuracy in these parameters:
Parameter | Range | Application Highlights |
---|---|---|
Thickness | 60–200 microns | Thin bags for light-duty goods, thick bags for heavy-duty materials. |
Weight | 50–200 GSM | Lightweight options for cost-efficiency; heavy-duty for robust packaging. |
Sizes | 20 cm × 30 cm to 100 cm × 200 cm | Small bags for retail, large bags for industrial needs. |
With precise control over these specifications, woven bags are adaptable to both niche and large-scale requirements.
2. Anti-Static Technology: Ensuring Safety in Sensitive Applications
Anti-static woven bags are essential for handling volatile or flammable materials. Here’s how they work:
- Electrostatic Discharge (ESD) Prevention
Conductive threads woven into the fabric dissipate static electricity, mitigating risks of sparks or explosions. - Advanced Coatings
Anti-static coatings applied to the surface enhance safety by reducing resistivity, especially during transportation or storage. - Compliance with Safety Standards
Many anti-static woven bags meet international standards such as ISO 61340-4-4, ensuring reliability in hazardous environments.
Example:
In the chemical industry, anti-static woven bags are used to safely transport powders and granules, preventing accidents caused by static build-up.
3. Load-Bearing Capabilities
Woven bags produced with Starlinger technology are designed to handle a broad spectrum of weights, ensuring structural integrity across various applications:
Load Range | Recommended Use Cases |
---|---|
5–25 kg | Packaging of rice, flour, and animal feed. |
25–50 kg | Transportation of fertilizers, grains, and industrial powders. |
50–1000 kg (FIBC) | Bulk materials like construction aggregates and chemicals. |
Rigorous quality testing, including drop tests and tensile strength evaluations, guarantees the bags perform reliably under maximum load conditions.
4. Starlinger Technology: A Benchmark for Excellence
Starlinger machinery sets the gold standard for woven bag manufacturing by incorporating advanced automation and precision. Key features include:
High-Speed Weaving
- Produces consistent fabric with exceptional tensile strength.
- Reduces manufacturing errors, ensuring uniformity.
Efficient Coating and Lamination
- Multi-layer laminations enhance durability and waterproofing.
- Supports branding with high-definition printing capabilities.
Customizable Features
- Enables integration of labels, handles, and liners for added functionality.
- Produces eco-friendly options with recyclable materials.
Statistical Insight:
Manufacturing with Starlinger technology can improve production efficiency by up to 40%, translating to lower costs and faster turnaround times.
5. Tailored Designs for Warehouse Efficiency
Color Coding and Labeling
- Customizable labels and color strips (blue, green, red) simplify inventory management by categorizing contents at a glance.
- Example: Blue-striped bags for grains, red-striped bags for chemicals.
Storage-Optimized Designs
- Stackable bags with anti-slip finishes improve space utilization in warehouses.
- Ventilated options maintain product freshness, especially for agricultural goods.
Convenience Features
- Handles and resealable tops enhance user experience during handling and transport.
- Inner liners ensure moisture protection for delicate products.
6. Versatility Across Industries
Agriculture
Custom woven bags are widely used for packaging grains, seeds, and fertilizers:
- Moisture-Resistant Liners prevent spoilage during long-term storage.
- High-Load Capacity accommodates bulk handling needs.
Construction
- Anti-static and reinforced woven bags handle heavy-duty applications like cement and sand.
- Waterproof laminations keep materials dry, even in outdoor conditions.
Retail
High-resolution printing on woven bags elevates brand visibility for retail packaging:
- Eye-Catching Designs attract consumers on store shelves.
- Eco-Friendly Materials cater to the growing demand for sustainable packaging.
FAQs
Q: What weight ranges can custom woven bags support?
A: Standard woven bags can handle up to 50 kg, while bulk FIBC bags can support up to 1000 kg.
Q: How do anti-static woven bags enhance safety?
A: They dissipate static electricity through conductive threads and coatings, ensuring safety in environments prone to static build-up.
Q: Can woven bags be customized for branding?
A: Yes, they support high-resolution printing and labeling, offering significant branding opportunities.
Q: What makes Starlinger technology stand out?
A: Its precision, automation, and ability to produce eco-friendly and high-performance bags make it a market leader.
7. Industry Trends and Future Directions
Sustainability
The industry is shifting toward sustainable practices, with recyclable materials and biodegradable options becoming standard. Starlinger machinery is designed to process eco-friendly polymers, aligning with global green initiatives.
Smart Packaging
- RFID-enabled woven bags improve inventory tracking.
- QR codes printed on bags allow consumers to access product information and recycling guidelines.
Enhanced Safety Standards
- Integration of advanced anti-static and flame-retardant materials ensures compliance with evolving safety regulations.
Conclusion
Custom woven bags crafted with Starlinger technology combine precision, durability, and versatility, making them indispensable for modern packaging needs. Whether it’s the ability to handle heavy loads, integrate anti-static features, or showcase vibrant branding, these bags set a high standard in the industry. Businesses looking for cutting-edge solutions can explore options like anti-static woven bags and leverage Starlinger’s advanced machinery for superior packaging outcomes.