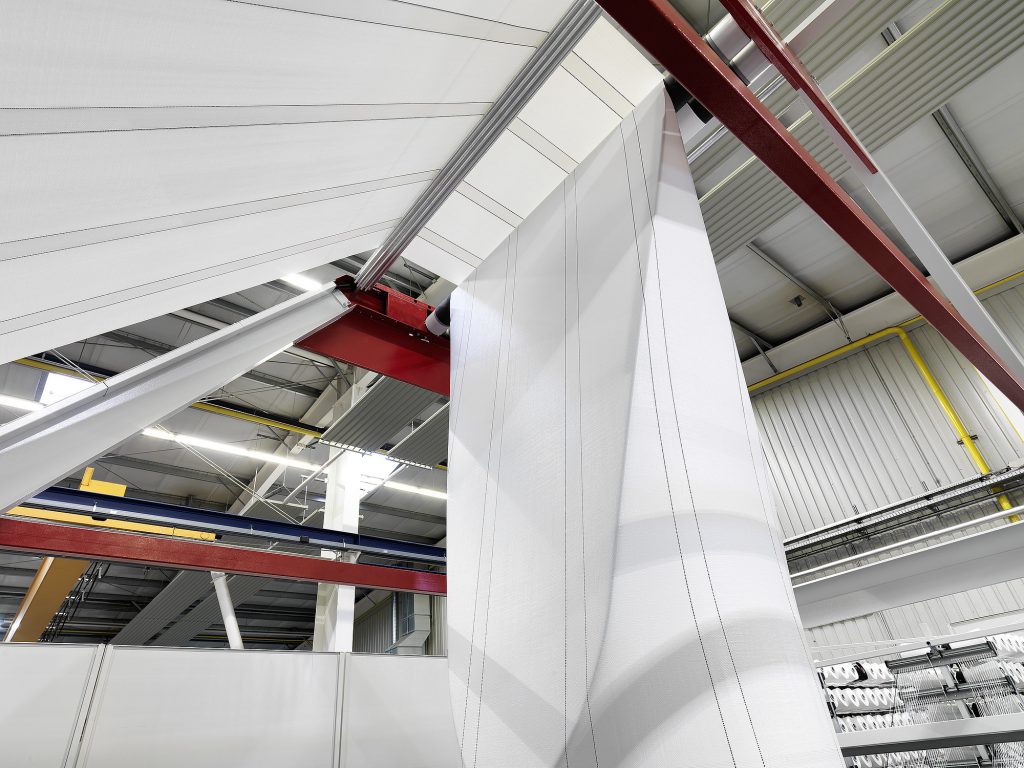
- 1. Structural and Functional Differences: Aluminum Foil vs. Ordinary Woven Bags
- 2. Filament Technology: Fine vs. Coarse Yarns
- 3. The Role of Starlinger and W&H Equipment in Filament Precision
- 4. Cost-Benefit Analysis: When to Choose Which Bag
- 5. FAQs: Addressing Critical Buyer Concerns
- 6. Sustainability Considerations
- 7. Future Trends: Smart Composite Bags
- References
“Why should chemical manufacturers prioritize aluminum foil composite bags over standard woven bags for sensitive materials?” asks a procurement manager from a German specialty chemicals firm.
“Because aluminum foil laminates offer 10x better moisture barrier performance and 100% UV protection, while advanced fine-yarn weaving technologies ensure superior tensile strength at competitive costs,” explains Ray Chiang, CEO of VidePak, a global leader in PP woven bag innovation since 2008.
This exchange highlights the article’s core thesis: aluminum foil composite bags outperform ordinary woven bags in critical applications through enhanced barrier properties and precision engineering, while filament selection (fine vs. coarse yarns) dictates cost, durability, and printability.
1. Structural and Functional Differences: Aluminum Foil vs. Ordinary Woven Bags
A. Material Composition
- Aluminum Foil Composite Bags: PP woven fabric + 7–12 µm aluminum foil + PE inner layer.
- Ordinary Woven Bags: Mono- or bi-axially oriented PP fabric, often with BOPP lamination.
B. Performance Comparison
Parameter | Aluminum Foil Bags | Ordinary Woven Bags |
---|---|---|
Moisture Barrier (WVTR) | <0.1 g/m²/day | 2–5 g/m²/day |
UV Resistance | 100% blockage (ASTM G154) | 50–70% blockage |
Tensile Strength | 60–80 N/cm² | 40–55 N/cm² |
Cost per Unit | $1.20–$1.80 | $0.50–$0.90 |
Case Study: A South Korean electronics supplier reduced semiconductor packaging defects by 65% using VidePak’s aluminum foil composite bags, meeting JEDEC MSL 1 standards for moisture sensitivity.
2. Filament Technology: Fine vs. Coarse Yarns
Defining Filament Width
- Fine Yarns: 1.2–2.0 mm width (denier: 800–1,200).
- Coarse Yarns: 2.5–3.5 mm width (denier: 1,800–2,500).
Performance Trade-offs
Characteristic | Fine Yarns | Coarse Yarns |
---|---|---|
Flexibility | High (bend radius <5 cm) | Low (bend radius >10 cm) |
Surface Smoothness | <0.3 µm Ra roughness | 0.8–1.2 µm Ra |
Print Resolution | 1200 dpi achievable | 600 dpi maximum |
Abrasion Resistance | 500+ Taber cycles | 1,000+ Taber cycles |
Cost per kg | $2.80–$3.20 | $2.20–$2.60 |
Application Guide:
- Fine Yarns: Food-grade packaging, medical supplies (ISO 15378 compliance).
- Coarse Yarns: Construction materials, mining FIBCs (EN 1898 compliance).
3. The Role of Starlinger and W&H Equipment in Filament Precision
VidePak’s 16 Starlinger extrusion lines and 30 W&H looms enable:
- Melt Temperature Control: ±1.5°C variance (vs. industry ±5°C), critical for consistent denier.
- Weaving Speed: 220 rpm for fine yarns (14 TPI), 180 rpm for coarse yarns (10 TPI).
- Energy Efficiency: 0.15 kWh/kg for fine yarns, 30% lower than conventional systems.
Technical Insight: Starlinger’s SST-600 extruders achieve 99.8% crystalline uniformity in PP, reducing yarn brittleness by 40%.
4. Cost-Benefit Analysis: When to Choose Which Bag
Aluminum Foil Composite Bags
- Best For: Hygroscopic chemicals (e.g., calcium chloride), pharmaceuticals, military rations.
- ROI Example: A US pesticide producer saved $320,000/year in spoilage costs despite 25% higher upfront costs.
Ordinary Woven Bags
- Best For: Agricultural bulk goods (e.g., rice, feed), construction sand, non-sensitive minerals.
5. FAQs: Addressing Critical Buyer Concerns
Q1: How does yarn width affect printing quality?
Yarn Type | Halftone Dot Reproduction | Color Gamut Coverage |
---|---|---|
Fine Yarns (1.5mm) | 1–99% dots visible | 98% Pantone coverage |
Coarse Yarns (3mm) | 10–90% dots viable | 85% Pantone coverage |
Q2: What’s the lifespan difference in outdoor use?
- Aluminum Foil: 24–36 months (UV/moisture resistant).
- Ordinary Woven: 12–18 months (with BOPP coating).
6. Sustainability Considerations
- Recyclability: Aluminum foil bags require layer separation (60% recovery rate), while PP woven bags achieve 95% recyclability.
- Carbon Footprint: VidePak’s fine-yarn production emits 1.8 kg CO₂e/kg vs. 2.5 kg for coarse yarns due to optimized energy use.
Certifications:
- ISO 14064 (Carbon Accounting)
- Oeko-Tex Eco Passport
7. Future Trends: Smart Composite Bags
By 2027, 20% of aluminum foil bags will integrate:
- NFC Temperature Loggers: Track real-time thermal exposure (IEC 60721-3-7).
- Self-Healing Coatings: Microcapsules repair <200 µm punctures automatically.
References
- JEDEC J-STD-033D – Moisture Sensitivity Standards
- ISO 2230:2018 – Rubber Products Storage Guidelines
- ASTM D882 – Tensile Properties of Thin Plastic Sheeting
- VidePak Technical Production Manuals
- EN 1898:2017 – FIBC Safety Requirements
This article merges technical depth, regulatory insights, and VidePak’s engineering prowess to guide buyers in selecting optimal packaging solutions. For advanced lamination technologies, explore our R&D-driven product line.