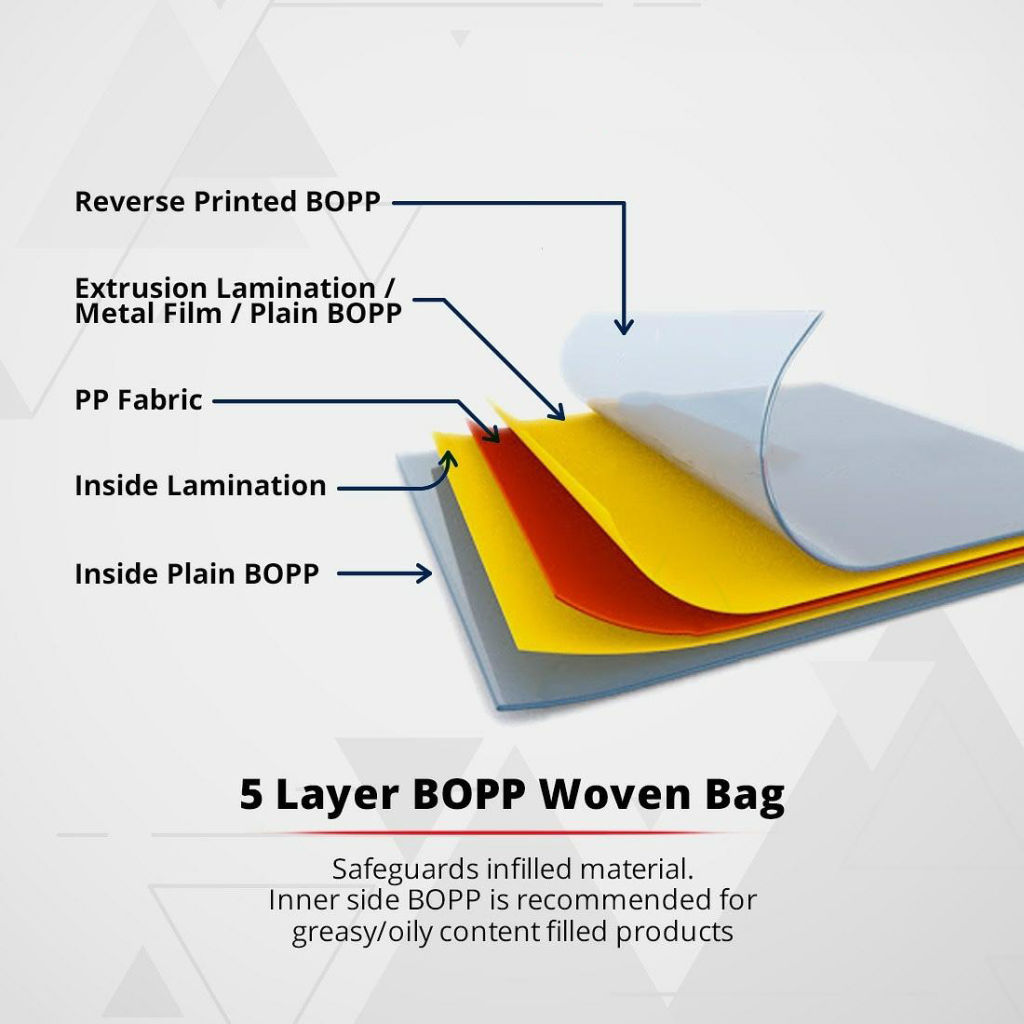
When it comes to packaging materials, Composite Woven Bags and Aluminum Foil Woven Bags are two popular options, each offering unique benefits depending on the application. Understanding the differences, the materials used, and the specific advantages of each can help businesses and consumers make informed decisions about which packaging solution is best suited to their needs.
This blog will explore the key differences between Aluminum Foil Composite Bags and traditional woven sacks, such as Multi-wall woven bags, and discuss important considerations in material selection—particularly the use of polypropylene (PP) and polyethylene (PE)—as well as the role of additives such as UV inhibitors and antioxidants in enhancing product performance.
1. Aluminum Foil Composite Bags vs. Traditional Woven Sacks
In the world of industrial packaging, Composite Woven Bags and Aluminum Foil Woven Bags each serve distinct purposes, with specific advantages depending on the type of goods being packaged and transported. Below is a breakdown of the main characteristics and advantages of these two packaging solutions:
Feature | Aluminum Foil Composite Bags | Traditional Woven Bags (e.g., PP, PE) |
---|---|---|
Material Composition | Aluminum foil laminated to a woven fabric (often PP or PET) | Woven polypropylene or polyethylene fabric |
Protection Level | Superior moisture, oxygen, and light barrier properties | Basic protection; some variants offer water resistance |
Strength and Durability | High tensile strength due to aluminum layer | Highly durable, but more prone to puncturing than foil |
Weight | Heavier than woven bags due to aluminum layer | Generally lighter, depending on the material and thickness |
Cost | More expensive due to multilayer construction | Cost-effective, especially in bulk quantities |
Environmental Impact | Limited recyclability due to the aluminum layer | Generally recyclable, particularly when made from PP |
Primary Uses | Packaging sensitive goods such as chemicals, food, and pharmaceuticals | Used for bulk materials like grains, construction materials, and animal feed |
Customizability | High degree of customization in size and design | Customization available through printing, size options |
Key Advantages of Aluminum Foil Composite Bags:
- Moisture and Oxygen Protection: The aluminum foil layer acts as a barrier to moisture, oxygen, and light, making these bags ideal for packaging products that are sensitive to environmental conditions, such as food, pharmaceuticals, and chemicals. This is particularly important for long-term storage and transport.
- Durability and Strength: The combination of woven fabric and aluminum foil ensures the bags are highly resistant to tearing, punctures, and damage during handling and transport. This added strength is beneficial for products that need extra protection.
- Temperature Resistance: Aluminum Foil Woven Bags are capable of withstanding a wide range of temperatures, making them ideal for applications where temperature fluctuations may be an issue.
Key Advantages of Traditional Woven Bags:
- Cost-Effective: Woven bags are typically less expensive than composite bags due to their simpler construction and materials. This makes them an attractive option for businesses seeking to reduce packaging costs.
- Versatility: Traditional woven sacks are extremely versatile, with applications ranging from food products to construction materials. They can also be customized with various coatings or liners, including PE or BOPP, to enhance durability or provide moisture protection.
- Eco-friendly Options: Woven bags made from polypropylene (PP) and polyethylene (PE) are recyclable, providing an environmentally friendly alternative to single-use plastic packaging options. This makes them a popular choice in sustainable packaging efforts.
2. Material Selection: Polypropylene (PP) vs. Polyethylene (PE)
When manufacturing Composite Woven Bags or traditional woven sacks, the choice between Polypropylene (PP) and Polyethylene (PE) plays a significant role in the performance of the final product. Each material has distinct characteristics that influence strength, flexibility, and suitability for different applications.
Polypropylene (PP):
- Strength and Durability: PP is known for its excellent tensile strength, making it ideal for heavy-duty applications. It can withstand harsh handling, abrasion, and extended use, which is why it is commonly used in Multi-wall woven bags and other industrial packaging.
- UV Resistance: PP bags are susceptible to degradation from UV exposure, but this can be mitigated by adding UV inhibitors during the production process.
- Cost: PP is generally more affordable than PE, making it a preferred option for companies looking to balance durability with cost.
- Applications: PP is commonly used in packaging for agricultural products, cement, and other bulk materials. It is also frequently used in Aluminum Laminated Woven Bags and Composite Woven Sacks where additional strength is needed.
Polyethylene (PE):
- Flexibility and Transparency: PE is more flexible than PP, offering superior resistance to punctures. It is often used in applications where flexibility and a transparent bag are preferred, such as in food packaging or for consumer goods.
- Waterproofing: PE offers superior resistance to water and moisture, making it ideal for packaging sensitive products in environments with high humidity.
- Lower Strength: PE is not as strong as PP, which may make it less suitable for heavy-duty applications unless combined with other materials.
- Applications: PE is commonly used in Multi-wall woven bags for lightweight products or where a moisture-resistant barrier is needed.
3. Fillers and Additives: Enhancing Performance
To further enhance the functionality of woven bags, manufacturers often incorporate various additives such as UV inhibitors, antioxidants, and anti-static agents into the materials. These additives improve the longevity and performance of the bags, making them suitable for specific applications.
UV Inhibitors:
- Purpose: UV inhibitors are added to woven bags to prevent degradation from sunlight exposure. This is especially important in outdoor applications where packaging is exposed to direct sunlight for extended periods.
- Impact on Performance: By preventing the breakdown of polymer chains, UV inhibitors help to extend the lifespan of Composite Woven Bags and woven sacks used for outdoor storage and transport.
Antioxidants:
- Purpose: Antioxidants are used to prevent the degradation of the polymer material due to exposure to oxygen. This is particularly important for PP and PE, which can become brittle over time when exposed to air.
- Applications: The addition of antioxidants ensures that the bags remain flexible and durable, even in challenging environments where exposure to oxygen is high.
Anti-static Agents:
- Purpose: Anti-static agents are used in packaging materials that need to handle electronics or other static-sensitive products. These agents help dissipate static charges, preventing damage to sensitive components during transport and storage.
Conclusion: Choosing the Right Packaging for Your Needs
Both Aluminum Foil Composite Bags and traditional woven sacks offer distinct advantages depending on the application. The decision on which to use should take into account the specific needs of the product being packaged, including factors such as moisture resistance, strength, cost, and environmental impact.
When considering Composite Woven Bags, it’s essential to assess the material composition, including the use of polypropylene (PP) or polyethylene (PE), and determine which features—such as UV resistance or moisture protection—are most important. Additionally, additives like UV inhibitors, antioxidants, and anti-static agents can play a critical role in enhancing the performance of these bags, ensuring that they meet industry standards and customer expectations.
To learn more about the benefits of Aluminum Foil Woven Bags and Composite Woven Bags in specific industries, you can check out more detailed case studies on their applications and production at the following links: