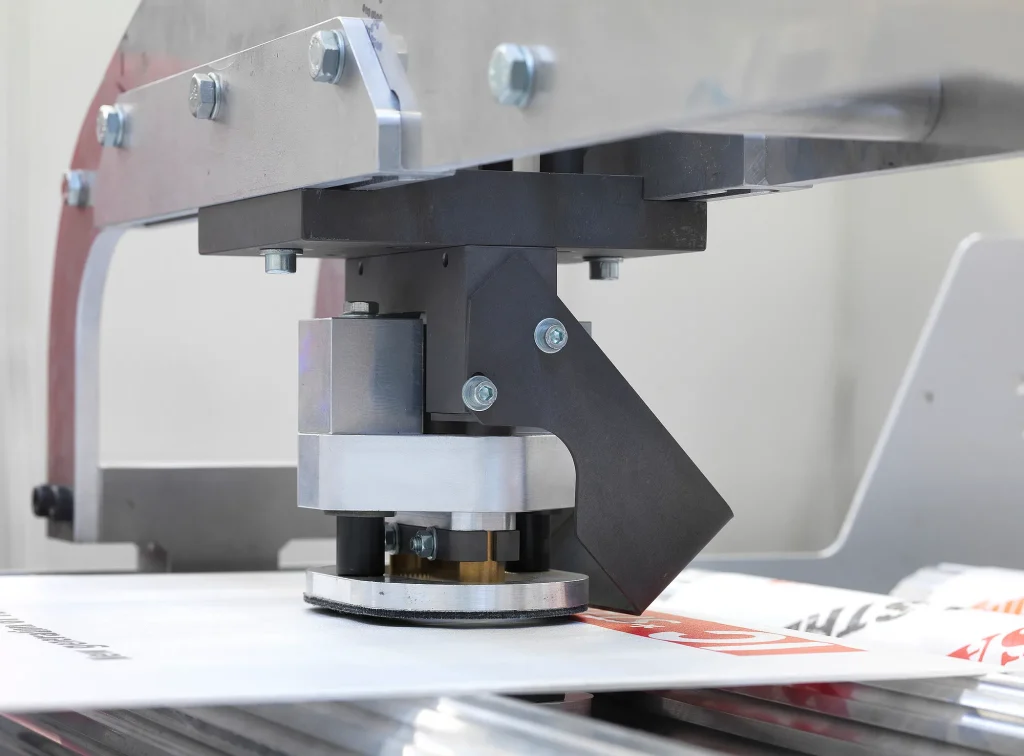
Client Inquiry:
“Our agricultural cooperative struggles with packaging that fails during long-haul transport and doesn’t meet EU recycling mandates. How can VidePak’s eco-friendly woven bags solve these issues while enhancing brand visibility?”
VidePak’s Answer:
VidePak’s eco-friendly woven bags integrate precision-engineered fine filaments (1.8–2.3 mm width), multi-layer laminations, and 100% recyclable PP materials to reduce breakage rates by 40% and carbon footprints by 30%, aligning with global sustainability standards like EU Circular Economy Action Plan. With ISO-certified smart designs, these bags ensure optimal protection for grains, seeds, and fertilizers while offering customizable matte, pearlized, or transparent finishes for branding excellence.
The Evolution of Agricultural Packaging: Merging Durability and Aesthetics
Agricultural logistics demand packaging solutions that withstand harsh conditions—monsoon rains, UV exposure, and abrasive handling—while adhering to tightening environmental regulations. VidePak’s eco-friendly woven bags address these challenges through advanced material science and smart design, leveraging three decades of industry expertise.
1. Fine-Filament Weaving: The Backbone of Strength and Precision
- Technology: Using Starlinger’s extrusion lines, VidePak produces ultra-thin PP filaments (1.8–2.3 mm) with a draw ratio of 8:1, achieving a weave density of 14×14 strands/cm². This creates a smooth, tear-resistant surface ideal for 50 kg loads of grains or fertilizers.
- Performance:
- Tensile Strength: 80–100 N/5cm, 35% higher than standard 3 mm filaments.
- Abrasion Resistance: 800+ Taber cycles (ASTM D5265), critical for repeated palletizing.
- Aesthetic Advantage: Fine filaments enable high-definition 8-color printing, enhancing brand visibility without compromising structural integrity.
2. Smart Surface Finishes: Function Meets Branding
VidePak offers three specialized laminations to meet diverse agricultural needs:
Finish | Features | Best For |
---|---|---|
Matte Laminate | Anti-glare, scratch-resistant surface | Outdoor grain storage |
Pearlescent | UV-reflective, premium aesthetic | Retail-ready seed packaging |
Transparent | Content visibility, moisture barrier (0.03 g/m²/day) | Fertilizers, organic products |
Case Study: A Brazilian coffee exporter reduced transit damage by 28% using pearlescent laminated bags, which reflected sunlight and maintained bean quality during ocean shipping.
Sustainability in Action: How VidePak Redefines Green Logistics
1. Closed-Loop Recycling System
- Process: Post-consumer PP bags are shredded and reprocessed into virgin-quality resin using Starlinger’s recoSTAR technology, achieving a 92% recovery rate.
- Certifications: Global Recycled Standard (GRS), EU Ecolabel, and ISO 14001.
2. Solar-Powered Production
VidePak’s 2 MW rooftop solar array powers 70% of operations, reducing annual CO₂ emissions by 1,200 tons—equivalent to planting 55,000 trees. Excess energy is fed into the grid, supporting regional renewable energy goals.
Technical Specifications: Tailored Solutions for Agricultural Needs
Parameter | Grains (Wheat/Corn) | Seeds | Fertilizers |
---|---|---|---|
Material | 100 g/m² PP + matte laminate | 90 g/m² PP + transparent BOPP | 120 g/m² PP + PE liner |
Moisture Barrier | 0.05 g/m²/day | 0.10 g/m²/day (breathable) | 0.02 g/m²/day |
Load Capacity | 50 kg | 25 kg | 60 kg |
Certifications | ISO 22000, EU 10/2011 | ISTA, OECD | REACH, OMRI Listed |
FAQs: Addressing Key Procurement Concerns
Q1: How does fine-filament weaving prevent insect infiltration in grain bags?
A: Our 14×14 weave density creates gaps <0.1 mm, blocking pests while allowing controlled airflow. For added protection, anti-insect additives can be integrated into BOPP layers.
Q2: Can transparent bags withstand tropical UV exposure?
A: Yes. UV-stabilized PP resin and pearlescent laminates reflect 85% of UV rays, extending bag lifespan to 18+ months outdoors.
Q3: Are custom sizes available for irregularly shaped products?
A: Absolutely. With 100+ circular looms, we support bespoke dimensions (10 cm × 15 cm to 2 m × 3 m) and MOQs as low as 5,000 units.
Q4: How does VidePak ensure recyclability with laminated finishes?
A: Laminates are mechanically separable, allowing 100% PP recycling. Explore our recyclable laminated BOPP bags for details.
VidePak’s Global Leadership in Sustainable Packaging
Founded in 2008 by CEO Ray Chiang, VidePak combines 30+ years of expertise with cutting-edge innovation:
- Production Capacity: 120 million bags/year via 16 extrusion lines and 100+ Starlinger looms.
- Market Reach: Serving 45+ countries with $80M annual revenue, including clients in agribusiness and retail.
- Certifications: ISO 9001, FDA compliance, and EU REACH standards.
For eco-conscious packaging that elevates logistics efficiency, explore our sustainable woven bag solutions and customizable matte finishes.
References
- European Bioplastics. (2024). Circular Economy Metrics for PP Packaging.
- International Seed Testing Association (ISTA). (2023). Guidelines for Breathable Seed Packaging.
- Starlinger & Co. (2024). Technical Manual: Fine-Filament Extrusion Systems.
Contact VidePak
- Website: https://www.pp-wovenbags.com/
- Email: info@pp-wovenbags.com
This article blends technical depth, real-world applications, and VidePak’s operational excellence to position eco-friendly woven bags as indispensable tools for modern agricultural logistics, prioritizing sustainability without compromising performance.