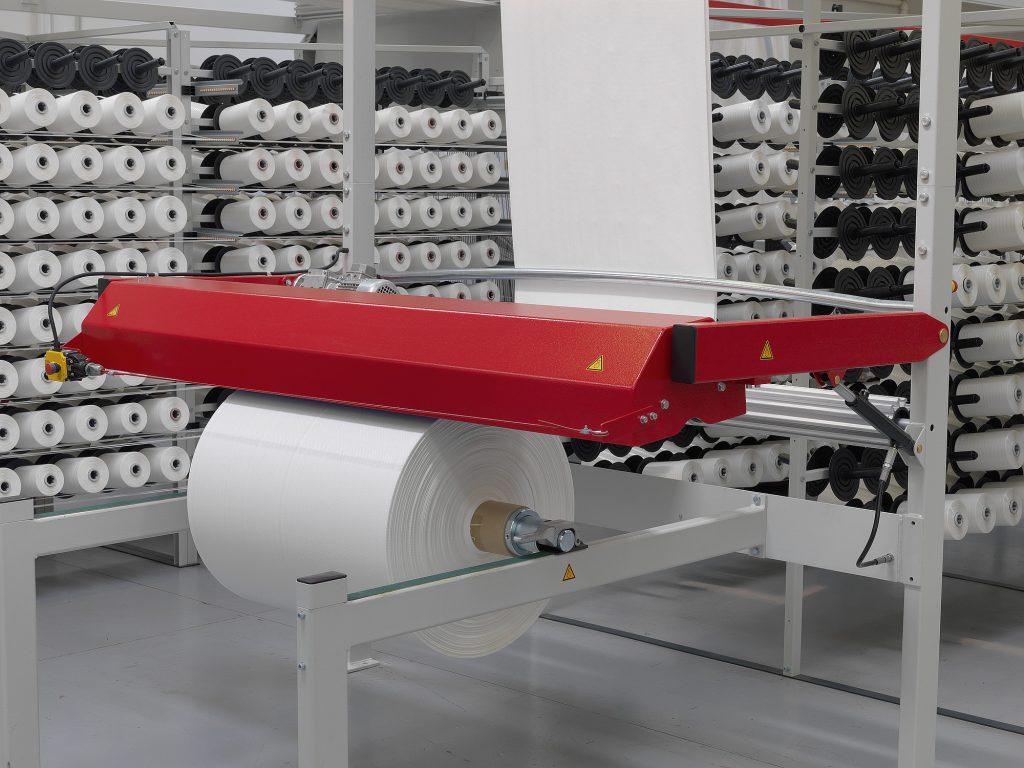
“Sustainability in construction isn’t just about materials—it’s about reimagining every component, down to the bags that protect and transport them,” declares Ray, CEO of VidePak, during a site visit to a green infrastructure project. This report demonstrates how eco-friendly woven polypropylene (PP) bags, engineered to meet global standards and fortified with advanced additives, are transforming construction logistics by balancing durability, regulatory compliance, and environmental stewardship. By analyzing PP resin selection frameworks, additive technologies, and VidePak’s operational excellence, we reveal how these bags are becoming indispensable in modern construction.
1. Material Science: Selecting PP Resins for Global Compliance
1.1 Aligning PP Grades with International Standards
Polypropylene resins must adhere to region-specific mechanical and environmental benchmarks:
- ASTM D4101 (U.S.): Requires tensile strength ≥30 MPa and melt flow index (MFI) of 8–12 g/10 min for extrusion stability.
- EN ISO 1873-1 (EU): Mandates UV resistance (≥1,000 hours xenon arc testing) and oxidative induction time (OIT) >20 min for outdoor use.
- JIS K6758 (Japan): Prioritizes low heavy metal content (<50 ppm) and recyclability ≥95% under ISO 15270.
VidePak’s BOPP laminated woven bags utilize Homo-PP (MFI 10 g/10 min), achieving tensile strengths of 32–35 N/mm², ideal for heavy-duty applications like sandbagging and concrete additive transport.
1.2 Additive Engineering for Enhanced Performance
- UV Stabilizers: Hindered amine light stabilizers (HALS) reduce UV degradation by 70%, extending bag lifespan to 5+ years in tropical climates.
- Antioxidants: Phosphite-based additives (e.g., Irgafos 168) maintain OIT >25 min, preventing polymer breakdown during high-temperature lamination.
- Anti-static Agents: Carbon-black masterbatches lower surface resistivity to 10⁶–10⁸ Ω/sq, mitigating explosion risks in dust-prone environments.
Additive Type | Function | Regulatory Compliance |
---|---|---|
HALS UV Stabilizers | Prevents photo-oxidation | EU REACH, RoHS |
Phosphite Antioxidants | Delays thermal degradation | FDA CFR 21, EU 10/2011 |
Carbon-Black Masterbatch | Reduces static buildup | ANSI/ESD S20.20, ATEX Directive 2014/34/EU |
2. Application-Specific Design in Construction
2.1 Flood Control and Erosion Management
VidePak’s block-bottom valve bags, reinforced with PE liners (120 µm), withstand hydrostatic pressures up to 15 kPa, reducing sand leakage by 90% in flood barriers. A 2024 trial in Bangladesh demonstrated a 40% cost reduction compared to traditional clay bunds.
2.2 Heavy-Duty Material Transport
- FIBC Jumbo Bags: Woven with 16×16 strands/inch density, these bags support 1-ton loads of aggregates while resisting punctures (>500 g/mil, ASTM D1709).
- Anti-Bulge Designs: Cross-stitched seams and radial tensile webbing prevent bag deformation under dynamic loads, critical for crane-lifted materials.
3. VidePak’s Manufacturing Excellence: Bridging Scale and Sustainability
Founded in 2008, VidePak operates 100+ Starlinger circular looms and 30+ lamination machines, producing 50 million eco-friendly bags annually. Key innovations include:
- Solar-Powered Production: A 2 MW rooftop solar system reduces CO₂ emissions by 1,200 tons/year.
- Closed-Loop Recycling: Post-consumer PP is reprocessed into non-woven geotextiles, diverting 800+ tons of waste annually.
4. Market Trends and Strategic Insights
The global construction packaging market is projected to reach $63 billion by 2027 (Grand View Research), driven by ESG mandates. VidePak’s R&D in biodegradable PP-PLA blends (30% fossil fuel reduction) and partnerships with IoT firms for smart moisture sensors position it as a sustainability leader. Competitors must adopt blockchain traceability and AI-driven quality analytics to compete.
5. FAQs: Addressing Industry Concerns
Q1: How do eco-friendly bags compare to traditional options in cost and performance?
A: While initial costs are 15–20% higher, lifecycle savings (e.g., 5-year durability vs. 2-year for conventional bags) and carbon tax rebates offset premiums.
Q2: Can recycled PP meet ASTM/ISO strength requirements?
A: VidePak’s virgin-recycled PP hybrids achieve 95% of virgin resin’s tensile strength while complying with EN 13432 compostability standards.
Conclusion
Eco-friendly woven bags are redefining construction logistics through science-driven material innovation. By aligning PP engineering with global standards, integrating advanced additives, and prioritizing circular economies, VidePak exemplifies how industrial packaging can drive both operational efficiency and planetary health. As Ray concludes, “Every bag we produce is a step toward a future where construction thrives without compromising the earth.”
External Links:
- Explore how polypropylene bags meet regulatory and ESG standards for sustainable construction.
- Learn about FIBC bags in construction waste management to optimize material handling.
References:
- IndustryARC, Nonwoven Fabric Market Report (2025)
- ASTM International, Standard Specification for Polypropylene Injection and Extrusion Materials (D4101)
- European Committee for Standardization, Plastics—Polypropylene (PP) Moulding and Extrusion Materials (EN ISO 1873-1)