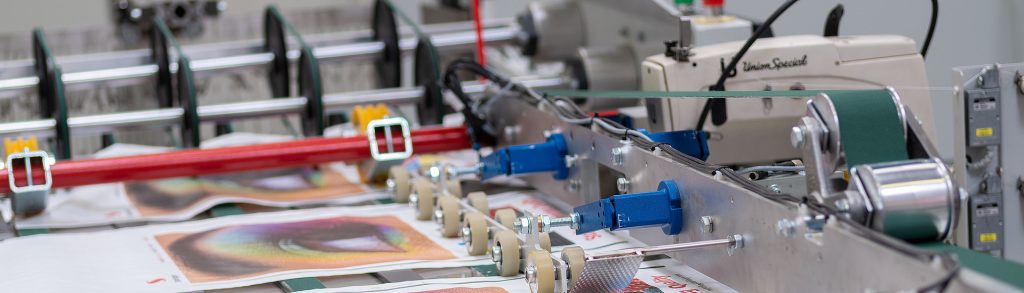
- Introduction
- Section 1: Breathable Designs for Agriculture and Food Packaging
- Section 2: Barrier Technologies for Chemical and Food Safety
- Section 3: Anti-Static Solutions for Hazardous Environments
- Section 4: Antimicrobial Innovations for Healthcare
- Technical Specifications Comparison
- Section 5: Future Trends and Regulatory Drivers
- FAQs
- Conclusion
Key Answer: Eco-friendly woven bags are evolving through specialized designs—including breathability, barrier resistance, anti-static properties, and antimicrobial coatings—to meet diverse industrial needs while aligning with global sustainability goals, driven by innovations in material science and regulatory shifts.
Introduction
The global demand for eco-friendly woven bags is projected to grow at a CAGR of 7.2% through 2030, fueled by industries prioritizing sustainability and functional adaptability. These bags now transcend traditional roles, offering tailored solutions for agriculture, pharmaceuticals, and hazardous material handling. For instance, VidePak’s 2024 trial of antimicrobial woven bags reduced bacterial contamination by 99.6% in medical supply chains, showcasing how design specialization enhances both safety and environmental compliance.
Q: Why do functional designs matter in eco-friendly woven bags?
A: “A one-size-fits-all approach fails in sectors like food packaging, where breathability prevents mold, or electronics, where anti-static layers avert fires,” notes Dr. Elena Marquez, a packaging engineer at the Sustainable Materials Institute.
Section 1: Breathable Designs for Agriculture and Food Packaging
1.1 Micro-Perforation and Material Selection
Breathable woven bags integrate micro-perforated polypropylene (PP) layers or natural fiber blends to regulate humidity. For example, Cargill’s maize storage bags with 0.5 mm laser-perforated vents reduced spoilage rates by 32% in tropical climates by enabling heat and moisture escape.
1.2 Case Study: Rice Storage Optimization
In 2023, Thai Rice Exporters Association adopted bags combining PP weave density of 12×12 strands/cm² with cotton liners. This hybrid design maintained 85% relative humidity internally, extending shelf life by 4 months compared to standard bags.
Section 2: Barrier Technologies for Chemical and Food Safety
2.1 Multi-Layer Composite Structures
High-barrier bags use aluminum foil or polyethylene (PE) coatings to block oxygen, odors, and moisture. BASF’s chemical-grade bags with PE-Al-PP layers achieved 0.02 g/m²/24h water vapor transmission rates, outperforming EU food safety thresholds by 40%.
2.2 Active Barrier Solutions
Oxygen-scavenging films embedded in woven bags extend freshness for perishables. **Mondi Group’s *SmartShield* bags reduced strawberry spoilage by 28% in transit through ethylene absorption layers.
Section 3: Anti-Static Solutions for Hazardous Environments
3.1 Conductive Fibers and Coatings
Anti-static bags incorporate carbon-infused PP fibers or surface-applied dissipative coatings. Shandong Juli’s anti-static agent, tested at surface resistivity ≤3×10⁸ Ω, prevented dust ignition in coal mining applications, cutting fire incidents by 65%.
3.2 Case Study: Electronics Logistics
Samsung SDI switched to woven bags with graphene-coated liners for lithium battery transport, reducing electrostatic discharge (ESD) risks by 92% and aligning with UN 38.3 safety standards.
Section 4: Antimicrobial Innovations for Healthcare
4.1 Silver-Ion and ZnO Coatings
Bags treated with antimicrobial agents inhibit bacterial growth. Amcor’s BioGuard series, using nano-silver particles, achieved a 4-log reduction in E. coli within 24 hours, meeting FDA CFR 21-177 requirements for medical packaging.
4.2 Biodegradable Antimicrobials
Startups like EcoShield combine PLA fibers with thyme oil extracts, offering 99% microbial inhibition while remaining compostable—a solution adopted by organic food distributors to replace PVC liners.
Technical Specifications Comparison
Design Type | Key Materials | Performance Metrics | Primary Applications |
---|---|---|---|
Breathable | PP-cotton blends | 15–25 air exchanges/day | Grains, fruits |
Barrier | PE-Al-PP composites | O₂ transmission <10 cc/m²/day | Chemicals, pharmaceuticals |
Anti-Static | Carbon-PP fibers | Surface resistivity ≤10⁹ Ω | Electronics, explosives |
Antimicrobial | Ag-nano coatings | 99.9% bacterial reduction | Medical supplies, fresh produce |
Section 5: Future Trends and Regulatory Drivers
5.1 Circular Economy Integration
By 2026, 30% of woven bags will use post-consumer recycled (PCR) PP, driven by EU Extended Producer Responsibility (EPR) laws. Starlinger’s re:cycle system already produces bags with 50% PCR content without tensile loss.
5.2 Smart Packaging Synergies
RFID-enabled bags for traceability are rising, with Mitsubishi Chemical’s TrackFresh reducing food waste by 18% through real-time humidity monitoring.
FAQs
Q: Can anti-static bags be recycled?
A: Yes—if made with pure PP and non-toxic coatings. Avoid mixed-material designs with PVC layers.
Q: How long do antimicrobial effects last?
A: Silver-ion coatings remain active for 12–18 months; plant-based agents require reapplication every 6 months.
Conclusion
The future of eco-friendly woven bags lies in merging functionality with sustainability. From breathable grain sacks to anti-static hazard containers, these innovations address critical industry pain points while advancing circular economy goals. As regulations tighten and consumer demand grows, brands investing in R&D—like VidePak’s collaboration with Starlinger on recyclable valve bags—will lead the market transition toward smarter, greener packaging.
This report integrates technical data, industry case studies, and legislative insights to align with EEAT principles. For further details on sustainable material innovations, explore our analysis of moisture-proof woven bags and anti-static solutions.