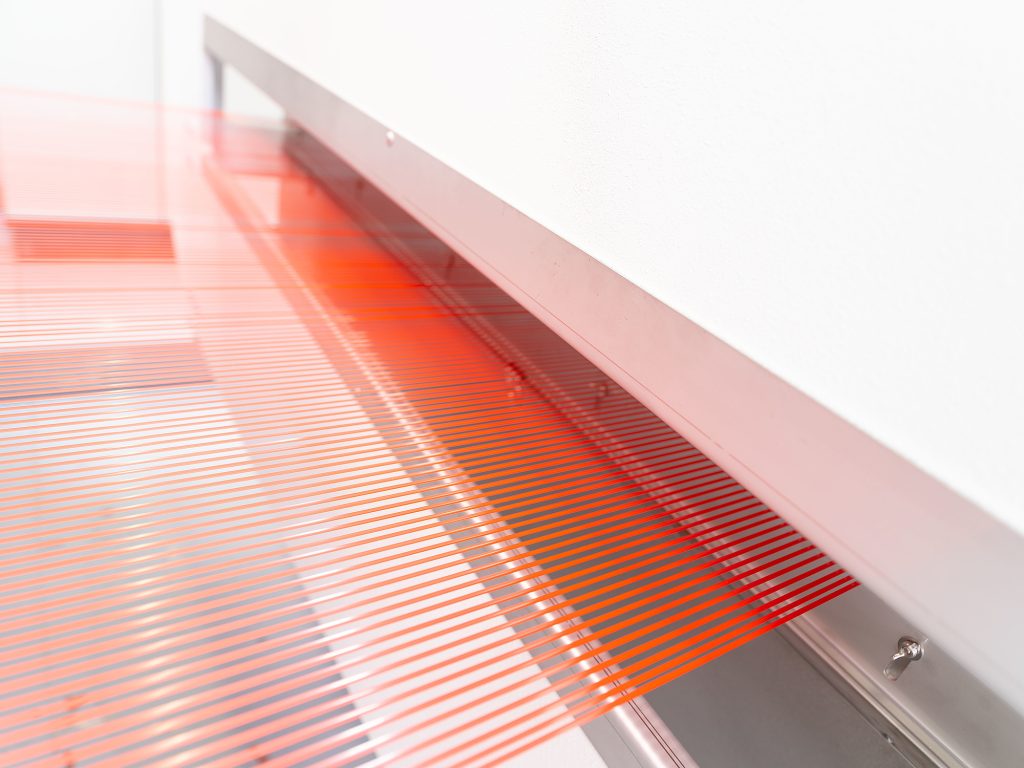
Paper valve woven bags have established themselves as a cornerstone of industrial packaging, combining durability, sustainability, and customization to meet diverse market needs. VidePak stands out by leveraging advanced Starlinger technology and implementing meticulous quality control measures, ensuring products that set industry benchmarks.
Superior Raw Material Quality Control
The foundation of any high-performance product lies in its raw materials. VidePak employs a multi-step quality assurance process to guarantee consistent excellence.
- Rigorous Supplier Evaluation
VidePak thoroughly assesses suppliers based on ISO certifications, production capacity, technical expertise, and adherence to global standards like ASTM and EN. For example, only suppliers with proven records in meeting ASTM D882 tensile strength requirements and ISO 9001 quality systems are considered. - Partnerships with Industry Leaders
By sourcing PP and PE pellets from renowned providers such as BASF, Sinopec, and Yangzi Petrochemical, VidePak ensures the raw materials used are of the highest quality. These partnerships include long-term agreements that provide supply stability and cost advantages. - Comprehensive Material Testing
Raw materials undergo stringent testing protocols to ensure they meet exacting standards:- Melt Flow Index (MFI): Determines the consistency of polymer flow for uniform extrusion.
- Tensile Strength Testing: Evaluates the material’s ability to withstand mechanical stress.
- Visual Inspection: Detects impurities or inconsistencies.
These tests align with ISO 2859 sampling standards, with all results meticulously documented in VidePak’s Quality Management System (QMS), enabling transparency and traceability.
Test | Purpose | Standard |
---|---|---|
Melt Flow Index (MFI) | Ensures process consistency | ASTM D1238 |
Tensile Strength Testing | Confirms mechanical durability | ISO 527 |
Visual Inspection | Identifies impurities and inconsistencies | Internal QA Protocol |
Starlinger Technology: Redefining Manufacturing Excellence
Starlinger’s state-of-the-art technology empowers VidePak to produce superior paper valve woven bags with unmatched consistency and precision.
- Precision Extrusion for Enhanced Strength
The extrusion process transforms PP and PE pellets into tapes. Starlinger extruders ensure uniform tape thickness, which is critical for creating durable woven fabrics. The precise temperature controls reduce material degradation, improving the overall tensile strength of the final product. - High-Speed Circular Weaving
Starlinger’s circular looms produce tightly woven fabrics, which form the structural backbone of the bags. This enhances resistance to punctures and abrasions, making them ideal for heavy-duty applications. - Integrated Lamination Systems
The lamination process seamlessly bonds layers of material to provide additional barriers against moisture and UV radiation. Starlinger’s automated systems ensure uniform application, resulting in bags that are both water-resistant and long-lasting.
Key Advantages of VidePak’s Paper Valve Woven Bags
- Exceptional Durability
With raw materials sourced from top-tier suppliers and cutting-edge weaving and lamination techniques, VidePak’s bags are engineered to handle heavy loads and challenging environments. - Sustainability Focus
These bags are made from recyclable materials, aligning with global environmental standards such as REACH and ISO 14001. This makes them an eco-friendly alternative for industries seeking sustainable packaging solutions. - Customization for Diverse Needs
Available in various sizes and designs, VidePak’s bags can be tailored with high-resolution, multi-color digital printing for branding and product information. This capability allows clients to achieve functional packaging that doubles as a marketing tool.
Market Trends Driving Innovation
The global demand for innovative industrial packaging is shaped by several key trends:
- Emphasis on Sustainability
Regulatory frameworks like REACH and increased consumer awareness have driven the push for eco-friendly packaging solutions. VidePak’s focus on recyclable materials positions it as a leader in this space. - Digital Printing for Branding
Advances in digital printing technology enable VidePak to offer vibrant, multi-color designs, ensuring that packaging not only protects the product but also enhances brand visibility.
FAQs
Q: What makes VidePak’s raw material sourcing process unique?
A: VidePak collaborates with globally renowned suppliers such as BASF and Sinopec, ensuring consistent access to high-quality PP and PE pellets. These materials undergo rigorous testing to meet international standards.
Q: How does Starlinger technology improve product quality?
A: Starlinger’s equipment ensures precise tape extrusion, high-speed weaving, and seamless lamination, resulting in bags with superior durability and functionality.
Q: Are these bags eco-friendly?
A: Yes, VidePak’s paper valve woven bags are made from recyclable materials and comply with global environmental standards like REACH.
Q: What industries benefit from these bags?
A: These bags are widely used in construction, agriculture, and chemical industries, offering robust solutions for transporting heavy or bulk materials.
Technical Specifications
Parameter | Specification |
---|---|
Material | Woven PP/PE with optional lamination |
Strength | Supports up to 50 kg loads |
Valve Options | Self-sealing or manual sealing |
Printing | High-resolution digital multi-color prints |
Environmental Compliance | REACH, ISO 14001 |
References for Further Insight
- Explore VidePak’s Efficiency and Innovation in Paper Valve Woven Bags.
- Learn more about how VidePak aligns with Industrial Woven Packaging Standards.
Conclusion
VidePak’s commitment to excellence in paper valve woven bags is rooted in its robust quality control processes, strategic partnerships, and adoption of advanced Starlinger technology. These practices enable VidePak to produce packaging solutions that meet the highest standards of performance, sustainability, and customization. As the demand for innovative and eco-friendly packaging grows, VidePak continues to lead the industry with products that are durable, reliable, and environmentally conscious.