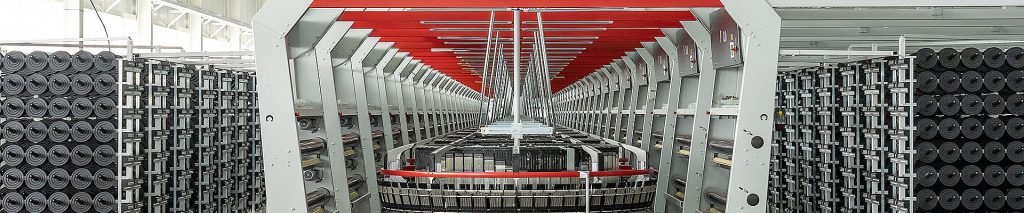
Answer in Brief: By integrating Printed Woven Bags with robust testing protocols—covering tensile and tear strength, heat sealing, anti-aging, and UV durability—VidePak ensures Printed Woven sacks, Multiple color bags, and Printed PP Woven Bags excel in both performance and branding.
As global markets continue to demand stronger, more visually striking packaging, recent studies (2024 Global Packaging Innovations Report) underscore the importance of combining high-quality materials with stringent quality evaluations. For enterprises handling bulk commodities—ranging from fertilizers to grains—Printed Woven Bags deliver brand visibility and mechanical resilience. In this article, we investigate how VidePak leverages comprehensive testing methods to guarantee consistent quality, from verifying yarn integrity to analyzing UV exposure effects.
1. Why Printed Woven Bags Still Matter
1.1 Enhancing Brand Impact
- Full-scale Custom Prints
- Example: A luxury pet food supplier upgraded to Printed PP Woven Bags featuring eight-color rotogravure designs, boosting shelf appeal and driving a 20% increase in brand recognition.
- Multi-hued imagery helps end users quickly identify products in busy retail or storage environments.
- Versatile Color Technology
- Multiple color bags are possible using advanced printing presses, preserving clarity and vibrancy across supply chains.
- Example: A multinational grain distributor adopted full-bleed printing, enabling bold, photo-realistic visuals to highlight premium product quality.
- Customization for Various Industries
- While single-color sacks may suffice for basic transport, specialized markets benefit from distinctive logos, text, or illustrations.
- Example: A fertilizer brand incorporated farmland scenes onto Printed Woven sacks, reinforcing authenticity and building consumer trust.
2. VidePak’s Comprehensive Quality Testing
VidePak adheres to internationally recognized standards—drawing on methods akin to ISO 13934-1 (tensile testing), ASTM D5034 (fabric strength), and QUV protocols (UV stability). This approach ensures that Custom Woven Bags consistently meet or exceed client demands for reliability.
2.1 Tensile Strength & Elongation
- Core Material Durability
- Tensile strength measures the force required to break the woven fabric. For heavy goods (e.g., construction materials), robust tensile ratings avert punctures and spills.
- Example: VidePak’s labs subject raw PP yarns to controlled stretching, confirming they handle forklift shocks during shipping.
- Elongation Control
- By tracking elongation at break, VidePak verifies that the bags absorb load shifts without sudden tearing.
- Example: A chemical producer shipping 25 kg loads relies on sacks with moderate elongation, preventing tears under dynamic warehouse conditions.
2.2 Tear Resistance Evaluations
- Preventing Small Nicks from Spreading
- While tensile tests confirm overall strength, tear evaluations gauge how well Printed Woven Bags handle localized damage.
- Example: A coffee exporter discovered that upgrading to higher tear-resistance fabric cut corner rips by 30%, improving product safety in transit.
- Elmendorf and Trapezoid Testing
- VidePak typically employs standardized tear methods—e.g., Elmendorf—to measure the force needed to propagate an existing slit in warp vs. weft directions.
2.3 Heat Sealing Integrity
- Seam Bond and Leak Prevention
- For laminated surfaces or specialized liners, heat-sealed seams must hold under load.
- Example: A pet food supplier implementing BOPP lamination needed precise sealing temperatures to retain barrier properties and eliminate product leaks.
- Peel Strength
- Peel tests quantify adhesive force between lamination layers, predicting potential delamination.
- Example: Bags failing peel standards can result in brand graphics flaking off, compromising marketing efforts.
2.4 Anti-aging and UV Resistance
- Outdoor Exposure
- If sacks spend weeks under sunlight—typical for fertilizers or feed—UV protection and anti-aging additives become critical.
- Example: A tropical poultry feed distributor requested 300-hour UV testing to ensure minimal color fade or polymer degradation.
- Accelerated Weathering Chambers
- Xenon arc or QUV apparatus replicate sunlight, heat, and humidity cycles.
- Example: VidePak sets thresholds (e.g., 500 hours) for color retention, verifying long-term storage viability in open yards.
2.5 Thickness, Edge, and Color Checks
- Thickness Tolerance
- Ensuring consistent thickness across Multiple color bags supports uniform printing and load distribution.
- Example: A 100 g/m² specification might allow a tight ±5 g/m² window, measured via micrometers.
- Cut-edge Uniformity
- Misaligned edges create “hairy” fringes, which reduce packaging aesthetics and can snag during filling.
- Example: VidePak’s cut-edge checklist ensures neatly trimmed Printed Woven sacks for premium display.
- Color Variance (ΔE) and Grammage
- Using spectrophotometers, VidePak measures color deviations against set Pantone or CMYK standards.
- Example: A big-box retailer might insist on ΔE ≤ 3 for brand-critical hues, guaranteeing consistent brand identity across batches.
3. Technical Table: Printed Woven Bags Specifications
Test Parameter | Typical Range | Significance |
---|---|---|
Tensile Strength (N) | 500–1000+ N | Resists breakage under heavy loads or impacts |
Tear Resistance (N) | 30–70 N (Elmendorf) | Mitigates minor cuts from expanding into major tears |
Heat Seal Temperature | 130–180°C (material-based) | Ensures reliable seam closure without laminate damage |
UV Stability Hours | 200–500 hours QUV/Xenon | Prevents color fade, polymer weakening in sunlit environments |
Thickness Tolerance | ±5–10% around nominal spec | Maintains uniform print results and mechanical consistency |
Color Variation (ΔE) | ≤2–3 | Upholds brand-accurate hues across multiple runs |
Grammage (g/m²) | 70–120 typical | Balances cost, weight, and structural resilience |
Example: A construction aggregate supplier might specify 90 g/m², 700 N tensile strength, 50 N tear resistance, and 300-hour UV stability—ensuring reliability for extended outdoor storage.
4. Conversation Snippets
Topic: “How do you ensure Printed Woven sacks maintain color fidelity batch after batch?”
Answer: We employ spectrophotometric ΔE checks on every print run. If any sample deviates from brand-approved Pantone or CMYK standards, we recalibrate inks and retest to guarantee uniformity.
Topic: “Are heat-sealed seams prone to failure in Multiple color bags?”
Answer: Properly controlled sealing temperatures prevent bag distortion or leaks. We also conduct peel tests to confirm that lamination layers stay fully bonded, regardless of the number of print colors used.
5. FAQs
- Q: Does printing multiple colors reduce bag strength?
A: Not inherently. The printing process doesn’t compromise fabric integrity as long as the lamination and weaving processes remain standardized. We still test tensile and tear strength to confirm overall durability. - Q: How often should I run UV stability tests for Printed Woven Bags stored outdoors?
A: If your products face extended sunlight, consider quarterly or biannual revalidations—especially for new ink colors or bag designs. - Q: Are Printed Woven sacks with BOPP lamination more difficult to recycle?
A: BOPP-laminated PP can still be recycled in many facilities; however, local regulations and recycling infrastructure may differ. We also explore eco-friendly solutions upon request. - Q: Do heat-sealed edges eliminate the need for stitching?
A: Some designs rely solely on heat sealing, while others combine stitching for added reinforcement. The optimal approach depends on your load, product type, and handling requirements. - Q: How do I confirm if a bag meets regulatory compliance in my region?
A: Provide relevant national or international standards (e.g., ISO, ASTM). We cross-reference these with test results to confirm compliance.
Conclusion
Through advanced printing techniques and a rigorous testing regime—spanning tensile strength, tear resistance, heat sealing, color accuracy, and UV protection—VidePak’s Printed Woven Bags, Printed Woven sacks, Multiple color bags, Printed PP Woven Bags, and Custom Woven Bags excel in both reliability and brand appeal. The comprehensive evaluations ensure consistent thickness, clean edges, and fade-resistant graphics, even under challenging environmental conditions.
By focusing on each detail—from yarn integrity to final lamination—VidePak empowers clients across agriculture, construction, and consumer markets to differentiate themselves, reduce losses, and drive loyalty through premium packaging solutions. In a world where packaging can set products apart, blending mechanical fortitude with eye-catching designs remains a winning formula—one that VidePak continues to refine with every test, every batch, and every innovation.