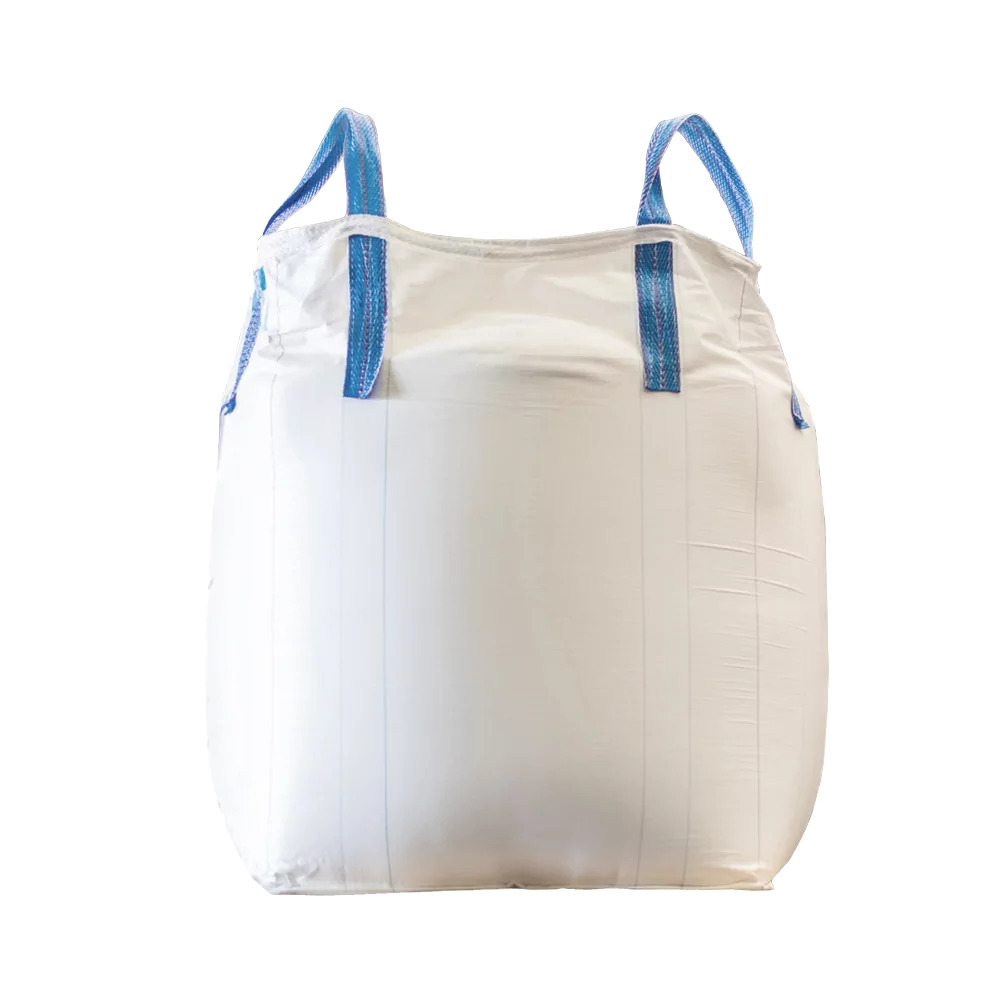
Flexible Intermediate Bulk Containers (FIBC Bags), commonly known as bulk bags, have become indispensable in industries requiring safe and efficient storage or transportation of bulk materials. Among these, woven bulk bags with antistatic properties play a critical role in ensuring safety during the handling of flammable or sensitive materials. At VidePak, our production processes leverage cutting-edge technologies from Austrian manufacturer Starlinger and German supplier W&H. This integration of advanced machinery not only boosts efficiency but also enhances product quality, particularly in terms of durability and flexibility.
Explore the versatility and benefits of FIBC Bags in bulk packaging applications. These bags, produced using automation-rich setups with line speeds exceeding 200 units per minute, showcase unparalleled efficiency and performance. Additionally, our focus on fine drawing techniques significantly influences the mechanical properties of these containers, making them a trusted choice across various industries.
The Role of Antistatic Properties in FIBC Bags
Antistatic FIBC bags are critical for environments where static electricity poses a risk. These bags, made with specially treated woven polypropylene, ensure safe handling in applications such as chemical, pharmaceutical, and food industries. The antistatic feature minimizes the chances of sparks, safeguarding materials and personnel. Our antistatic bulk bags conform to Type C or Type D safety classifications, ensuring compliance with stringent industrial safety standards.
Below is an overview of VidePak’s antistatic FIBC bag specifications:
Parameter | Details |
---|---|
Material | Woven polypropylene with antistatic coating |
Safety Factor | 5:1 or 6:1 |
Capacity | 500kg to 2000kg |
Dimensions | Customizable based on client requirements |
UV Protection | Optional, up to 1500 hours |
Applications | Chemicals, food grains, pharmaceutical powders |
The Influence of Drawing Techniques on Bag Durability
One of the most critical aspects of producing woven bulk bags is the drawing process, which involves stretching molten polypropylene into fine tapes. This process determines the tapes’ tensile strength and elasticity—two factors that directly impact the bag’s durability and flexibility. At VidePak, our state-of-the-art drawing machines from Starlinger operate with precise tension control, ensuring consistent tape quality.
Advantages of Advanced Drawing Techniques:
- Enhanced Tensile Strength: Our finely drawn tapes exhibit higher breaking strength, allowing the bags to handle heavier loads without tearing.
- Improved Flexibility: Uniform drawing reduces brittleness, making the bags more pliable and resistant to stress.
- Dimensional Stability: Advanced tension controls ensure that tapes maintain uniform thickness and width, providing stability during bag fabrication.
- Abrasion Resistance: High-quality tapes resist wear and tear, even under rough handling conditions.
Automation-Driven Efficiency in Production
VidePak’s reliance on high-speed machinery ensures that our woven bulk bags are produced with exceptional consistency and minimal wastage. Each step, from extrusion to lamination and printing, benefits from automation, allowing us to maintain quality while meeting high-volume demands.
Key Features of Our Production Line:
- Extrusion Lines: 16 units capable of producing superior PP tapes with uniform density.
- Circular Looms: 150 machines weaving seamless tubular fabrics with precision.
- Lamination Units: 32 machines applying protective layers to enhance bag longevity.
- Printing Systems: 16 advanced units enabling high-definition, multi-color designs.
Learn more about how woven bulk bags meet industry-specific requirements.
Customized Solutions for Diverse Applications
VidePak provides a variety of customization options to cater to diverse client needs. Whether it’s antistatic coatings, UV protection, or unique dimensions, our production capabilities ensure the delivery of tailored solutions. Below is a comparison of standard and customized FIBC bag features:
Feature | Standard Bags | Customized Solutions |
---|---|---|
Material | Virgin polypropylene | Blends with additional additives |
Coating | Single-layer lamination | Multi-layer, with antistatic or UV layers |
Load Capacity | Up to 1000kg | Up to 2000kg |
Printing Options | Single-color logos | Multi-color, high-definition branding |
Closure Types | Open top, plain bottom | Spout top, discharge bottom |
Industry-Leading Equipment and Its Advantages
Starlinger and W&H are synonymous with quality and innovation in the packaging industry. By integrating their equipment, VidePak achieves a perfect balance between productivity and product excellence. Some notable features of our equipment include:
- High-Speed Production: Line speeds exceeding 200 bags per minute ensure large-scale production without compromising on quality.
- Multi-Machine Integration: Synchronization between extrusion, weaving, and lamination machines minimizes downtime.
- Automated Quality Checks: Inline inspection systems detect defects early, ensuring only flawless products leave the factory.
Meeting Global Standards with Rigorous Testing
To guarantee the reliability of our FIBC bags, VidePak adheres to global testing standards, including ISO 21898 for bulk bags. Tests conducted include:
- Drop Tests: To evaluate resistance to impact.
- Stack Tests: To verify load-bearing capacity under vertical pressure.
- UV Aging Tests: To ensure durability under prolonged sunlight exposure.
- Tensile Tests: To measure tape strength and elongation.
Conclusion
The combination of innovative drawing techniques and state-of-the-art machinery positions VidePak as a leader in the production of antistatic FIBC bags and woven bulk bags. Our commitment to quality and efficiency ensures that we consistently deliver products that exceed client expectations while adhering to the highest safety and durability standards. With a focus on customization, automation, and advanced manufacturing, VidePak continues to redefine excellence in bulk packaging solutions.