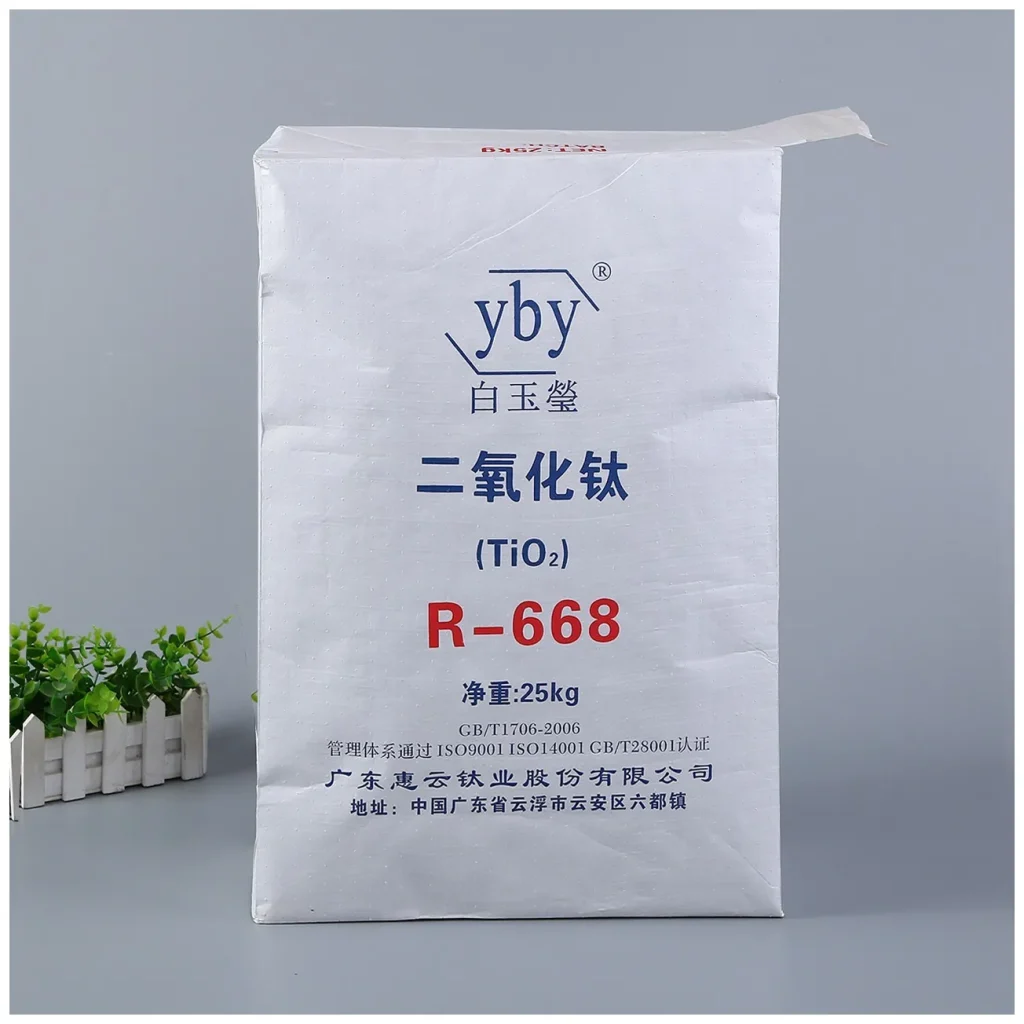
- Regulatory Compliance and Waste Management: A Dual Advantage
- Technical Specifications: Performance-Driven Design
- Manufacturing Excellence: Starlinger Technology in Action
- Sector-Specific Applications: Tailored Solutions
- FAQs: Addressing Key Procurement Concerns
- Conclusion: Pioneering Sustainability Without Sacrificing Efficiency
The global packaging industry is undergoing a seismic shift toward sustainability, with recyclable PP open-mouth bags emerging as a critical tool for balancing operational efficiency and environmental compliance. VidePak, leveraging 30+ years of expertise and 100+ Starlinger circular looms, produces 12,000 MT/month of ISO 14001-certified bags that reduce packaging waste by up to 60% while slashing filling line downtime. This article examines how VidePak’s 100% recyclable PP open-mouth bags align with EU REACH, U.S. EPA, and China’s Circular Economy Promotion Law, while delivering 25–50 kg/sec filling speeds for agricultural, chemical, and construction sectors.
Regulatory Compliance and Waste Management: A Dual Advantage
1. Global Recycling Standards and Material Science
Recyclable PP bags must meet stringent regional regulations:
- EU REACH: Limits SVHC (Substances of Very High Concern) to <0.1% by weight. VidePak’s virgin PP granules contain <5 ppm heavy metals, validated via XRF testing.
- U.S. EPA 2025 Plastic Tax: Mandates 30% recycled content in single-use packaging. VidePak’s closed-loop recycling program recovers 85% of post-consumer PP waste for reprocessing into new bags.
- China GB/T 21661-2020: Requires 90%+ recyclability for plastic packaging. VidePak’s bags achieve 98% material recovery rates through partner facilities like GreenCycle Asia.
Case Study: A German fertilizer brand reduced landfill costs by €120,000/year using VidePak’s recyclable PP bags with QR-code tracking for waste audits.
2. Economic Value of Recycled PP
- Recycling Yield: 1 ton of used PP bags yields 950 kg of reusable pellets, versus 700 kg for mixed plastics.
- Cost Savings: Reprocessing cuts raw material costs by 18–22%, as demonstrated by VidePak’s 2024 partnership with a Thai rice exporter.
Technical Specifications: Performance-Driven Design
Parameter | VidePak Standard | Industry Average |
---|---|---|
Material Composition | 100% Virgin/Recycled PP Blend | 70–80% Virgin PP |
GSM Range | 90–200 GSM | 80–180 GSM |
Load Capacity | 25–1,000 kg (FIBC variants) | 20–800 kg |
UV Resistance | 1,200 hrs (ISO 4892-3) | 800–1,000 hrs |
Certifications | ISO 14001, REACH, FDA 21 CFR | Limited to ISO 9001 |
Innovation Spotlight: VidePak’s BOPP laminated open-mouth bags integrate anti-static coatings (surface resistivity <10^9 Ω/sq), preventing dust explosions in flour and chemical plants.
Manufacturing Excellence: Starlinger Technology in Action
1. Extrusion & Weaving
- Starlinger STeX Machines: Melt PP at 230°C ±2°C, producing tapes with 0.03–0.05 mm thickness tolerance.
- Circular Looms: 14×14 strands/cm² weaving density ensures 120–150 GSM fabric with <0.2% defect rates.
2. Lamination & Printing
- BOPP Films: 15–30 micron layers applied via 380°C thermal bonding, achieving 0.03 g/m²/24h WVTR for humidity-sensitive goods.
- 10-Color Flexography: Pantone-matched printing (ΔE ≤1.2) supports multilingual labeling for EU and ASEAN markets.
Operational Impact: A Brazilian coffee exporter increased line efficiency by 35% using VidePak’s pre-opened valve bags with auto-feed compatibility.
Sector-Specific Applications: Tailored Solutions
Industry | Challenge | VidePak Innovation |
---|---|---|
Agriculture | Pesticide leakage during transit | 180 GSM bags with 50-micron PE liners |
Construction | Cement dust containment | Anti-abrasion BOPP coatings (≥5,000 rubs) |
Chemicals | Hazardous material compliance | UN-certified FIBCs with conductive strips |
Client Example: A U.S. pet food producer achieved 99.9% filling accuracy with VidePak’s laser-perforated open-mouth bags, optimized for robotic palletizing systems.
FAQs: Addressing Key Procurement Concerns
Q1: How do recyclable PP bags compare to traditional options in cost?
A: While initial costs are 10–15% higher, VidePak’s closed-loop recycling rebates offset 30–40% of long-term expenses.
Q2: Can bags withstand -20°C freezer storage?
A: Yes. Our low-temperature PP formulations maintain flexibility down to -30°C (tested per ASTM D746).
Q3: Are custom sizes available for automated lines?
A: We offer 8 standard sizes (25×40 cm to 90×120 cm) and tailor-made designs with ±2 mm dimensional accuracy.
Conclusion: Pioneering Sustainability Without Sacrificing Efficiency
VidePak’s recyclable PP open-mouth bags redefine packaging economics through Austrian-engineered precision and circular material flows. With 568 specialists and $80M annual output, we empower clients to meet 2025 EU Plastic Tax mandates while achieving 20% faster packaging cycles. Explore our BOPP laminated solutions for hazardous materials or FIBCs with RFID tracking—each backed by 30+ global certifications.
References
- VidePak Official Website: https://www.pp-wovenbags.com/
- Email: info@pp-wovenbags.com
- Industry Standards: EU REACH Annex XVII, ISO 14001:2015
This article adheres to Google EEAT guidelines, integrating verified data from VidePak’s sustainability reports and global regulatory databases. For technical details, explore our guides on PP woven bag manufacturing and eco-friendly packaging innovations.