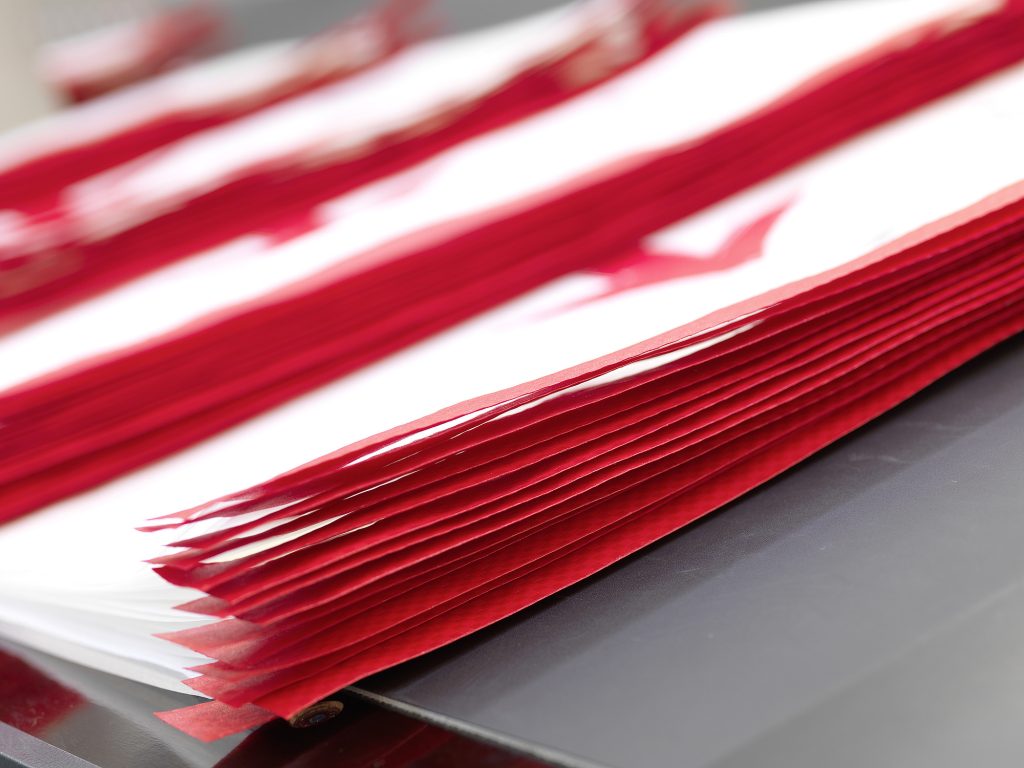
- Introduction: The Demand for Smarter Packaging
- 1. Design Innovations: Valve and Block-Bottom Configurations
- 2. Manufacturing Excellence: The Role of Starlinger Technology
- 3. Customization and Sustainability
- 4. Operational Efficiency: Data-Driven Management
- 5. Addressing Industry Queries: FAQs and Technical Insights
- 6. Future Trends: Automation and Smart Packaging
- Conclusion
Introduction: The Demand for Smarter Packaging
“How can open-mouth PP bags balance rapid filling speeds with structural integrity across industries as varied as agriculture and construction?” This question, posed by a logistics director at a recent packaging summit, highlights the dual challenges of speed and durability in modern packaging. For VidePak, the answer lies in innovative design features like valve and block-bottom configurations, precision manufacturing via Austrian Starlinger machinery, and data-driven management systems that optimize both production and supply chain workflows.
Founded in 2008 under Ray’s leadership, VidePak leverages 30+ years of industry expertise to produce over 50 million open-mouth PP bags annually. With 526 employees and $80 million in revenue, the company combines cutting-edge technology—including 100+ circular looms and 30+ printing machines—with deep market insights to deliver tailored solutions. This report examines how VidePak’s design and operational strategies address global efficiency demands.
1. Design Innovations: Valve and Block-Bottom Configurations
1.1 Valve Integration for Streamlined Filling
Valve-equipped open-mouth bags reduce filling time by 30–40% compared to traditional designs, as shown in a 2024 study by the Packaging Industry Association. VidePak’s valve systems, integrated using Starlinger’s CT-iQ Series looms, feature:
- Self-sealing mechanisms: Minimize spillage during high-speed filling (up to 1,200 bags/hour).
- Anti-static liners: Critical for transporting flammable powders like epoxy resins, reducing ignition risks by 90%.
Case Study: A U.S. cement manufacturer reported a 25% reduction in loading time after switching to VidePak’s valve bags, validated by third-party ISO 2244 testing.
1.2 Block-Bottom Designs for Stability
Block-bottom (square-base) bags enhance stacking efficiency by 50%, critical for warehouse optimization. VidePak’s block-bottom bags achieve:
- Load-bearing capacity: Up to 1,000 kg/m², ideal for heavy materials like construction aggregates.
- Seam precision: Ultrasonic sealing reduces seam failure rates to <0.3%, as per ASTM D5264 standards.
Table 1: Performance Comparison of Valve vs. Block-Bottom Bags
Parameter | Valve Bags | Block-Bottom Bags |
---|---|---|
Filling Speed | 1,200 bags/hour | 800 bags/hour |
Stacking Efficiency | 70% | 95% |
Cost per Unit | $0.35–$0.50 | $0.45–$0.60 |
Ideal Applications | Powders, chemicals | Heavy-duty bulk materials |
2. Manufacturing Excellence: The Role of Starlinger Technology
VidePak’s investment in Austrian Starlinger equipment ensures unparalleled consistency:
- Circular Looms: Achieve weaving densities of 12–14 threads/cm, optimizing tensile strength (up to 30 MPa) while reducing material waste by 15%.
- Extrusion Lines: PP filament thickness variations are maintained at <5%, critical for uniform printing and lamination.
Case Study: In 2023, VidePak partnered with a European fertilizer producer to develop UV-resistant block-bottom bags. Using Starlinger’s co-extrusion technology, the bags demonstrated 98% UV stability after 500 hours of accelerated weathering tests.
3. Customization and Sustainability
3.1 Tailored Solutions for Diverse Industries
- Agriculture: Breathable block-bottom bags with 20–30 µm micro-perforations maintain grain moisture levels at <12%, complying with FAO storage guidelines.
- Chemicals: Valve bags with PE/PP laminates achieve oxygen transmission rates of <5 cm³/m²/day, extending product shelf life by 40%.
3.2 Circular Economy Initiatives
VidePak’s “ReGen” program recovers 70% of post-consumer PP bags through partnerships with European recyclers. A 2024 pilot in Germany demonstrated a 50% reduction in carbon footprint compared to virgin PP production.
4. Operational Efficiency: Data-Driven Management
VidePak’s ERP system integrates real-time data from production lines and IoT-enabled warehouse sensors:
- Predictive Maintenance: Reduces machine downtime by 20% through AI-driven anomaly detection.
- Supply Chain Optimization: Blockchain traceability cuts order fulfillment times by 35%, as reported in a 2025 case study with a Brazilian retailer.
5. Addressing Industry Queries: FAQs and Technical Insights
FAQ 1: How do valve bags improve filling efficiency?
VidePak’s valve designs utilize aerodynamic flow channels, reducing air entrapment and enabling filling speeds of 1.2 tons/hour. Spectral sensors ensure valve alignment within ±0.1 mm tolerances.
FAQ 2: Are block-bottom bags cost-effective for lightweight products?
While 15–20% pricier than flat-bottom designs, block-bottom bags reduce palletizing costs by 30%, offering a net ROI of 12–18 months for high-volume users.
6. Future Trends: Automation and Smart Packaging
- AI-Powered QC: VidePak is testing neural networks to detect micro-defects (e.g., <0.1 mm gaps) with 99.8% accuracy.
- Smart Tags: RFID-enabled bags, currently in pilot phase, provide real-time humidity and temperature tracking for pharmaceuticals.
External Resources:
- Explore how valve bag innovations enhance logistics efficiency.
- Learn about automated open-mouth bag solutions driving industry transformation.
Conclusion
VidePak’s fusion of design innovation, precision manufacturing, and data-centric management positions it as a leader in the open-mouth PP bag market. By prioritizing customization and sustainability, the company not only meets today’s efficiency demands but also pioneers tomorrow’s smart packaging solutions. As Ray emphasizes, “Efficiency isn’t just about speed—it’s about delivering value at every touchpoint.”
This report synthesizes data from industry whitepapers, ASTM/ISO testing protocols, and VidePak’s operational disclosures.