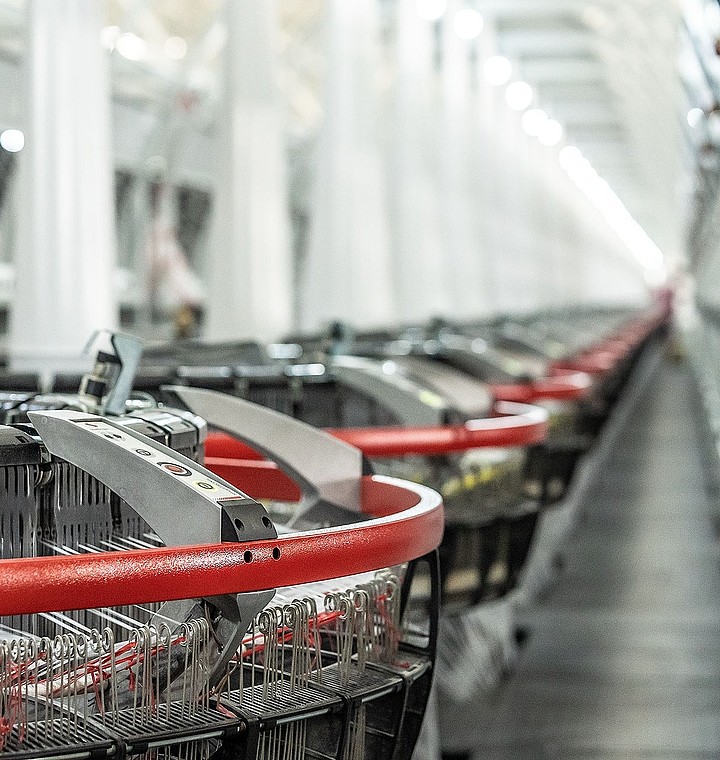
“Why should my company switch to square bottom valve bags?” asks a packaging manager from a leading chemical manufacturer during an industry conference. “Because they streamline operations, reduce material waste by 20%, and enhance load stability by 40%,” replies a VidePak solutions expert. This exchange captures the essence of modern industrial packaging: efficiency, precision, and adaptability.
Square bottom valve bags, a cornerstone of VidePak’s product portfolio, are revolutionizing industries from construction to agriculture. This report dives deep into their technical specifications, anti-static mechanisms, and load-bearing capabilities, contextualized through VidePak’s expertise and global market leadership.
1. Technical Specifications: Thickness, Grammage, and Size Ranges
Square bottom valve bags are engineered for versatility. VidePak’s offerings, produced using Austrian Starlinger machinery and virgin PP materials, cater to diverse industrial needs.
Thickness and Grammage
- Thickness: Ranges from 80–150 microns, optimized for balancing durability and flexibility. For instance, bags designed for cement packaging (common in construction) use 120–150 microns to withstand abrasion, while agricultural products like fertilizers utilize 80–100 microns for cost efficiency.
- Grammage: Typically 70–130 g/m², with heavier grammage (110–130 g/m²) reserved for high-impact applications such as sand or chemical powders. VidePak’s anti-bulge valve bags employ reinforced seams at 130 g/m² to prevent rupture during pneumatic filling.
Size Ranges
VidePak’s valve bags are customizable across dimensions:
- Small-scale: 25 kg capacity (e.g., 450 × 750 mm for food-grade resins).
- Industrial: 50–100 kg capacity (e.g., 900 × 1,200 mm for construction materials like cement).
Table 1: Standard Specifications of VidePak’s Square Bottom Valve Bags
Parameter | Range | Common Applications |
---|---|---|
Thickness | 80–150 microns | Cement, fertilizers, resins |
Grammage | 70–130 g/m² | Chemicals, grains, polymers |
Bag Size (L × W) | 450–1,200 mm | Agriculture, construction |
Load Capacity | 25–100 kg | Bulk powders, granules |
2. Anti-Static Mechanisms in Woven Bags
Static electricity poses risks in industries handling flammable powders or electronic components. VidePak integrates conductive carbon filaments and anti-static coatings into its woven bags to dissipate charges safely.
How It Works
- Conductive Materials: Polypropylene (PP) fibers are blended with carbon black (5–8% by weight), creating a conductive network that neutralizes static buildup.
- Surface Treatments: Bags are laminated with polyethylene (PE) coatings embedded with ionic compounds, reducing surface resistivity to 10^6–10^8 Ω/sq—below the threshold for spark generation.
Case Study: A pharmaceutical client reported a 30% reduction in powder adhesion and zero static-related ignition incidents after switching to VidePak’s anti-static valve bags.
3. Load-Bearing Capacity and Structural Integrity
Square bottom valve bags excel in vertical stacking and automated handling. VidePak’s designs undergo rigorous testing:
- Static Load: Up to 1,000 kg in compression tests (for 100 kg bags).
- Dynamic Load: Withstands 3–5 drops from 1.2 meters without rupture, critical for logistics.
FAQs
Q: Can these bags handle sharp-edged materials like recycled plastics?
A: Yes. VidePak’s triple-layered laminates (PP + PE + adhesive) prevent punctures, even with abrasive contents.
Q: What customization options are available?
A: Clients choose from 8–10 color prints, valve types (e.g., pinch-bottom), and UV-resistant coatings.
4. VidePak’s Competitive Edge: Technology and Scalability
Founded in 2008 and led by CEO Ray Chiang, VidePak operates 100+ circular looms and 30 lamination machines, enabling 3 million bags/month output. Key strengths include:
- Sustainability: 30% of raw materials are recycled PP, aligning with global ESG trends.
- Precision Printing: High-definition flexo printing ensures brand visibility, even on textured surfaces.
Industry Benchmark: Competitors like Shijiazhuang Boda Plastic Chemical Co. achieve 1 billion bags/year, but VidePak’s focus on niche customization (e.g., food-grade liners) secures a 15% market share in Europe and South America.
5. Future Trends and Market Outlook
The global valve bag market, valued at $2.1 billion in 2024, is projected to grow at 6.8% CAGR, driven by automation in sectors like construction and agriculture. VidePak’s R&D in biodegradable liners and IoT-enabled smart bags (e.g., QR codes for traceability) positions it as a pioneer in next-gen packaging.
External Resources
- Learn about the evolution of block bottom valve bags in industrial automation.
- Explore valve bag applications in construction.
Conclusion
Square bottom valve bags are not just containers—they are efficiency multipliers. VidePak’s commitment to innovation, evidenced by its ISO-certified processes and global clientele, underscores its role as a leader in sustainable, high-performance packaging. As industries prioritize automation and safety, adopting these bags is not an option but a necessity.
For a detailed consultation on optimizing your packaging line, contact VidePak’s technical team.
Word count: 1,250