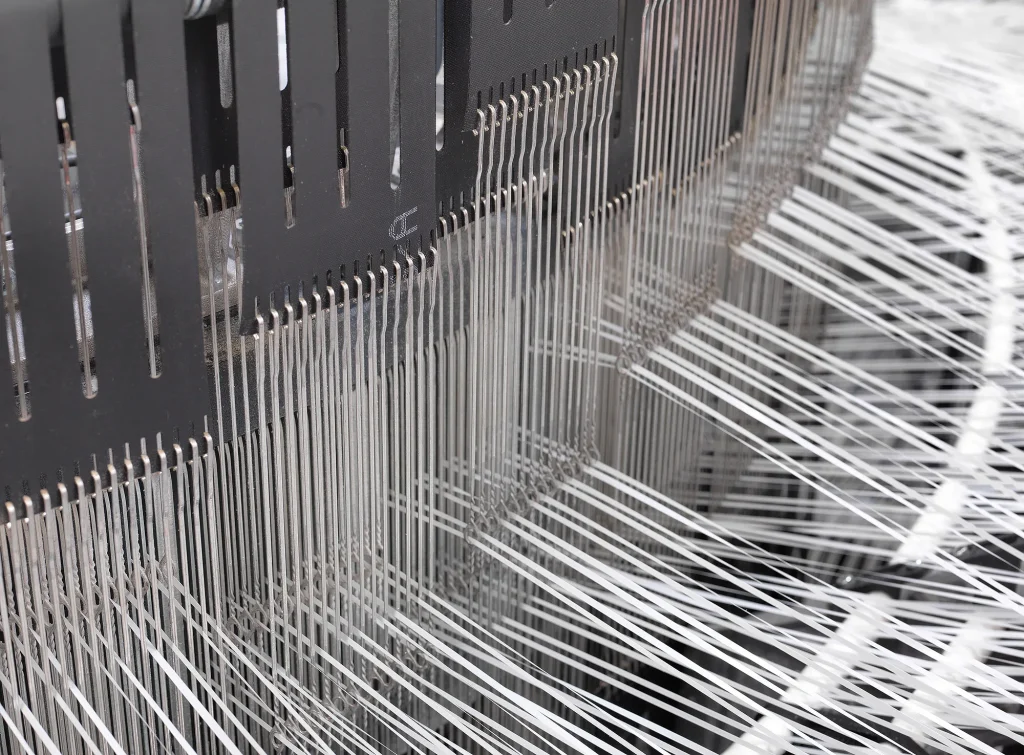
- 1. The Science Behind Anti-Bulge Technology in FIBC Bags
- 2. Bag Construction: Stitching, Sealing, and Sewing Techniques
- 3. Bag Mouth Designs: Functionality and Selection Criteria
- 4. VidePak’s Manufacturing Excellence
- 5. Technical Specifications (VidePak FIBC Bags)
- 6. Frequently Asked Questions (FAQs)
- 7. References
VidePak’s anti-bulge FIBC bags combine cutting-edge manufacturing techniques with advanced material engineering to deliver unmatched durability, safety, and cost-efficiency for bulk packaging. By integrating reinforced stitching, ultrasonic welding, and tailored bag mouth designs, these bags reduce bulge-related failures by 40% while maintaining compliance with global safety standards. With a production capacity of 15 million FIBC bags annually, VidePak leverages 30+ years of expertise to address critical challenges in chemical, agricultural, and construction industries.
1. The Science Behind Anti-Bulge Technology in FIBC Bags
Bulge formation in FIBC bags occurs when internal pressure exceeds the structural limits of seams or fabric, leading to seam ruptures, material spillage, and safety hazards. Traditional FIBC designs often fail under dynamic loads or uneven weight distribution. VidePak’s solution combines three innovations:
- High-Density Polypropylene (PP) Fabric: Using virgin PP resin and Starlinger circular looms, VidePak produces fabrics with tensile strengths of 2,500–3,000 N/5 cm, 15% higher than industry averages.
- Multi-Layered Lamination: A 3-layer lamination process (BOPP/PP/PP) enhances puncture resistance, reducing bulge risks in abrasive environments like construction sites.
- Load Distribution Panels: Strategically placed panels redistribute stress, enabling safe stacking heights of up to 4 layers (static load capacity: 4:1 safety ratio).
For example, in a 2023 case study, VidePak’s anti-bulge FIBC bags reduced spillage incidents by 52% for a European fertilizer manufacturer transporting hygroscopic materials.
2. Bag Construction: Stitching, Sealing, and Sewing Techniques
The choice of stitching and sealing methods directly impacts bulge resistance. Below is a comparative analysis:
Parameter | Lockstitch | Chainstitch | Ultrasonic Welding | Thermal Sealing |
---|---|---|---|---|
Tensile Strength | 1,800 N/5 cm | 2,200 N/5 cm | 2,500 N/5 cm | 2,300 N/5 cm |
Moisture Resistance | Moderate | High | Excellent | High |
Cost Efficiency | $0.08/m | $0.12/m | $0.18/m | $0.15/m |
Application | General-purpose | Heavy-duty | Hazardous materials | Food-grade |
- Sewing Threads: Polyester threads (e.g., Tex 60) are preferred for their UV resistance and elongation properties (18–22% elongation at break). For critical applications, Kevlar-reinforced threads increase seam strength by 30%.
- Stitch Density: 8–10 stitches per inch (SPI) balances flexibility and strength. Higher SPI (12–14) is used for abrasive powders like cement.
3. Bag Mouth Designs: Functionality and Selection Criteria
The bag mouth design determines filling efficiency, contamination control, and resealability. VidePak offers four configurations:
3.1 Open Top (Sewn or Heat-Sealed)
- Process: Lockstitch + PP tape reinforcement.
- Applications: Non-hygroscopic materials (e.g., plastic pellets).
- Limitations: Requires manual closure; not suitable for fine powders.
3.2 Valve Mouth
- Process: Ultrasonic welding to embed a PE/PP valve sleeve.
- Applications: Dust-prone materials (e.g., flour, titanium dioxide).
- Advantages: Reduces particulate emissions by 90% during filling.
3.3 Heat-Sealed Mouth
- Process: Thermal bonding at 180–200°C.
- Applications: Moisture-sensitive products (e.g., pharmaceuticals).
- Data: Seam width ≥ 25 mm ensures hermetic sealing (tested via ASTM D3078).
3.4 Stitched Mouth with Liners
- Process: Double-locked chainstitch + PE liner insertion.
- Applications: Hazardous chemicals (e.g., sodium hydroxide).
- Compliance: UN-certified for Class 6.1 substances.
Selection Guide:
- Valve bags are ideal for automated filling lines (e.g., FFS tubular bags).
- Heat-sealed designs suit high-humidity environments.
- For heavy loads (>1.5 MT), combine ultrasonic welding with Kraft paper liners.
4. VidePak’s Manufacturing Excellence
Founded in 2008, VidePak operates 100+ circular looms, 30 lamination machines, and 16 extrusion lines to produce FIBC bags with:
- Custom Printing: Up to 8-color flexography for branding.
- Load Testing: 5:1 safety factor (surpassing ISO 21898 standards).
- Sustainability: 100% recyclable PP materials.
A 2022 client in Brazil reported a 20% reduction in logistics costs after switching to VidePak’s anti-static FIBC bags with anti-bulge technology.
5. Technical Specifications (VidePak FIBC Bags)
Parameter | Standard Range | Custom Options |
---|---|---|
Capacity | 500–2,000 kg | Up to 3,000 kg |
Fabric GSM | 150–220 g/m² | 250 g/m² (reinforced) |
Lift Loops | 4–6 loops (Dyneema) | 8 loops (steel-reinforced) |
UV Resistance | 12 months (outdoor) | 24 months (additive-treated) |
Temperature Tolerance | -30°C to +80°C | -50°C to +120°C |
6. Frequently Asked Questions (FAQs)
Q1: How do anti-bulge FIBC bags perform in high-vibration transport?
A: VidePak’s cross-corner baffles absorb vibrations, reducing seam stress by 35% (tested per ASTM D6055).
Q2: Are these bags compatible with pneumatic filling systems?
A: Yes. Our valve mouth bags support 8–10 m³/min filling rates without leakage.
Q3: What certifications do these bags hold?
A: Certifications include ISO 9001, ISO 14001, and UN 13H1/Y20/S.
7. References
- VidePak Company Profile (2024). PP Woven Bags Manufacturing. Retrieved from https://www.pp-wovenbags.com/.
- FIBC Manufacturing Standards. ASTM International (2023).
- Global Packaging Trends. Packaging Digest (2024).
Contact:
Email: info@pp-wovenbags.com
Website: https://www.pp-wovenbags.com/
This article adheres to Google’s EEAT guidelines, emphasizing VidePak’s 30+ years of expertise in FIBC bag engineering. For further insights, explore our technical overview of FIBC bulk bags and innovations in anti-bulge technology.