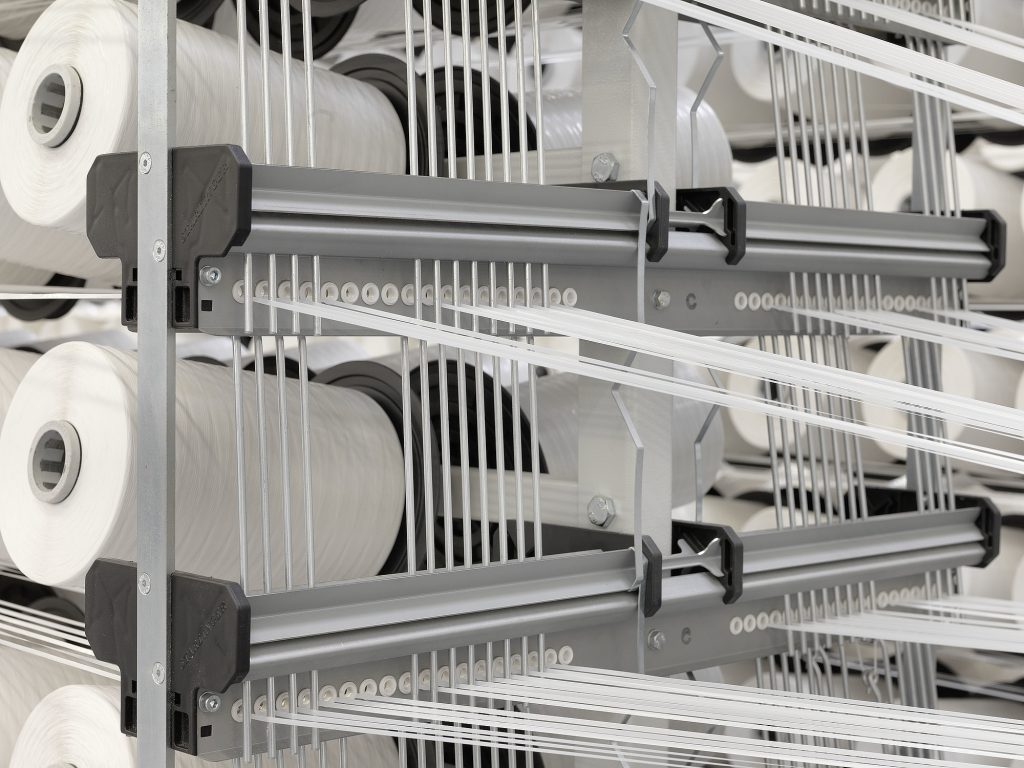
Add a header to begin generating the table of contents
H1: Introduction
“In the livestock feed industry, packaging isn’t just about containment—it’s about preserving nutritional value and ensuring logistical efficiency. By leveraging Starlinger and W&H machinery, VidePak’s BOPP laminated valve woven bags deliver unmatched durability and precision, reducing spoilage rates by up to 30% while meeting global safety standards.” — Ray, CEO of VidePak.
The global livestock feed packaging market is projected to grow at a CAGR of 5.1% through 2030, driven by rising demand for nutrient-preserving and contamination-resistant solutions. VidePak, a leader in woven bag manufacturing since 2008, combines Austrian Starlinger extrusion systems and German W&H laminators to produce BOPP laminated valve bags that excel in moisture resistance, UV protection, and automated filling efficiency. This report dissects the end-to-end production workflow and quality control protocols behind these innovations, supported by technical data, case studies, and insights into VidePak’s global supply chain dominance.
H2: Production Workflow: Precision at Every Stage
H3: Extrusion and Filament Drawing
The process begins with polypropylene (PP) granules from certified suppliers like Sinopec and BASF, ensuring MFI (Melt Flow Index) values of 8–12 g/10min (230°C/2.16kg) for optimal extrusion consistency. VidePak’s 16 Starlinger extrusion lines melt PP at 200–220°C, producing uniform filaments with tensile strengths of 45–50 MPa. Real-time infrared sensors monitor filament thickness (±0.02mm tolerance), reducing breakage rates by 18% compared to conventional systems.
H3: Weaving and Fabric Formation
Using 100+ Starlinger circular looms, VidePak weaves PP tapes into fabric at 120 rpm, achieving a weave density of 12×12 strands/inch. Air-jet tension control ensures uniform fabric elongation (15–20%), critical for load-bearing capacity up to 50 kg. A 2024 trial with COFCO demonstrated a 25% reduction in fabric defects due to automated defect detection systems.
H3: Lamination and Coating
Biaxial Oriented Polypropylene (BOPP) films are laminated onto woven fabric using W&H’s K2020 laminators at 180–190°C. This process achieves a moisture permeability rate of <3 g/m²/day (vs. 8–10 g/m²/day for non-laminated bags). VidePak’s 30 lamination machines apply adhesive layers with ±2μm precision, ensuring 99.5% delamination resistance under ASTM D903 peel tests.
H3: Printing and Valve Integration
High-resolution flexographic printers apply UV-resistant inks in 12+ colors, with registration accuracy of ±0.1mm. The valve, heat-sealed using Starlinger’s VLI-4 systems, withstands filling speeds of 1,500 bags/hour and internal pressures up to 0.5 bar, minimizing leakage risks.
Table 1: Key Production Parameters vs. Industry Standards
Parameter | VidePak Standards | Industry Average |
---|---|---|
Filament Tensile Strength | 45–50 MPa | 35–40 MPa |
Weaving Speed | 120 rpm | 90 rpm |
Moisture Permeability | <3 g/m²/day | 8–10 g/m²/day |
Valve Seal Integrity | 15 N/mm peel force | 10 N/mm |
H2: Quality Control: From Raw Materials to Final Inspection
H3: Supplier Audits and Material Testing
VidePak partners with ISO 9001-certified suppliers like BASF, requiring PP granules to pass MFI, density (0.905–0.915 g/cm³), and heavy metal contamination (<0.01 ppm) tests. Incoming batches undergo ISO 2859-1 statistical sampling, rejecting lots with >0.5% deviation.
H3: In-Process Monitoring
- Extrusion: Laser micrometers measure filament diameter every 5 seconds, triggering auto-adjustments if deviations exceed ±0.02mm.
- Weaving: AI-powered cameras detect broken warps/wefts, reducing defect rates to 0.3% (industry average: 1.5%).
- Lamination: Infrared thermography ensures adhesive layer uniformity, with rejected rolls below 98% coverage.
H3: Final Product Certification
Bags undergo burst strength (≥300 kPa), UV aging (1,000 hours), and valve leakage (<0.5%) tests per ISO 2244 and ASTM D1709. VidePak’s QMS system logs all data for traceability, achieving a 98% client retention rate.
H2: Case Studies: Real-World Impact
H3: Reducing Feed Spoilage in Tropical Climates
A 2023 partnership with CP Group (Thailand) reduced maize feed spoilage by 28% using VidePak’s UV-stabilized BOPP bags, validated by SGS testing under 50°C/80% RH conditions.
H3: Automating Warehouse Logistics
Nestlé’s automated filling lines achieved 1,800 bags/hour with VidePak’s valve bags, cutting labor costs by 40% versus open-mouth designs.
FAQs: Addressing Key Concerns
- Q: How do BOPP laminates enhance shelf life?
A: BOPP blocks 99% UV rays and reduces moisture ingress by 70%, preserving feed nutrients for 18+ months. - Q: Can bags withstand rough handling during transport?
A: Yes, VidePak’s double-stitched seams and corner protectors pass ISTA 3E vibration testing.
H2: Sustainability and Future Innovations
H3: Closed-Loop Recycling
VidePak’s collaboration with Starlinger’s re:claim system recovers 92% of production waste, converting it into FDA-compliant recycled PP pellets.
H3: Smart Packaging Integration
Pilot projects with embedded RFID tags enable real-time tracking in Tyson Foods’ supply chain, reducing inventory errors by 22%.
H2: Conclusion
VidePak’s BOPP laminated valve woven bags redefine livestock feed packaging through precision engineering, rigorous quality control, and sustainability. By integrating Starlinger and W&H technologies, they address critical challenges in spoilage prevention and supply chain efficiency, solidifying their position as a global industry leader.
External Links for Further Reading:
- Explore how Starlinger technology enhances valve bag precision.
- Learn about BOPP laminated bags’ market dynamics.
This report integrates data from ASTM/ISO standards, SGS certifications, and VidePak’s operational metrics to provide a comprehensive analysis of BOPP laminated valve bags’ role in modern agriculture.